A3 Mk2
Removing and installing cylinder head |
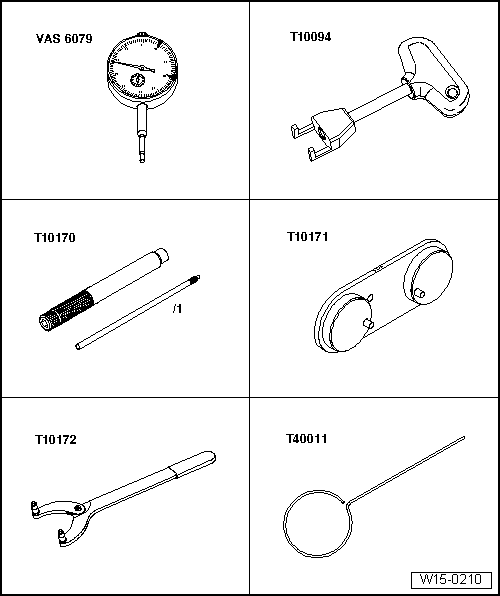
Special tools and workshop equipment required |
t | Dial gauge -VAS 6079- |
t | Puller -T10094- |
t | Adapter for dial gauge -T10170- |
t | Camshaft clamp -T10171- |
t | Counterhold tool -T10172- |
t | Locking pin -T40011- |
|
|
![]() |
|
![]() |
|
![]() |
|
![]() |
|
![]() |
|
![]() |
|
![]() |
|
![]() |
|
![]() |
|
![]() |
|
![]() |
|
![]() |
![]()
|
![]() |
![]()
|
![]() |
|
![]() |
![]()
|
![]() |
|
![]() |
|
![]() |
|
![]() |
|
![]() |
|
![]() |
|
![]() |
|
![]() |
![]()
|
![]() |
|
![]() |
|
![]() |
|
![]() |
|
![]() |
|
![]() |
![]()
|
![]() |
![]()
|
![]() |
|
![]() |
|
![]() |
|
![]() |
![]()
|
![]() |
|
![]() |
![]()
|
![]() |
|
![]() |
|
![]()
|
|
![]() |
|
![]() |
![]()
|
![]() |
![]()
|
![]() |
|
![]() |
|
![]() |
|
![]() |
Component | Nm | |||||||
Camshaft adjuster to camshaft | 40 + 90° 1)2)3) | |||||||
Camshaft sprocket to camshaft | 50 + 90° 2)3) | |||||||
Spark plugs in cylinder head | 30 | |||||||
Sealing caps to camshaft housing | 10 | |||||||
Engine lifting eye to timing chain cover | 20 | |||||||
Pressure control valve for crankcase breather system to timing chain cover | 10 | |||||||
Coolant pump pulley to coolant pump | 20 | |||||||
Thermostat housing to cylinder head | 10 | |||||||
High-pressure pipes | High-pressure pump | 15 | ||||||
to: | Fuel rail | 15 | ||||||
High-pressure pump bracket | 7 | |||||||
EGR connecting pipe to exhaust gas recirculation valve -N18- | 8 | |||||||
Throttle valve module -J338- to intake manifold | 7 | |||||||
|