A4 Cabriolet Mk2
Removing and installing sump |
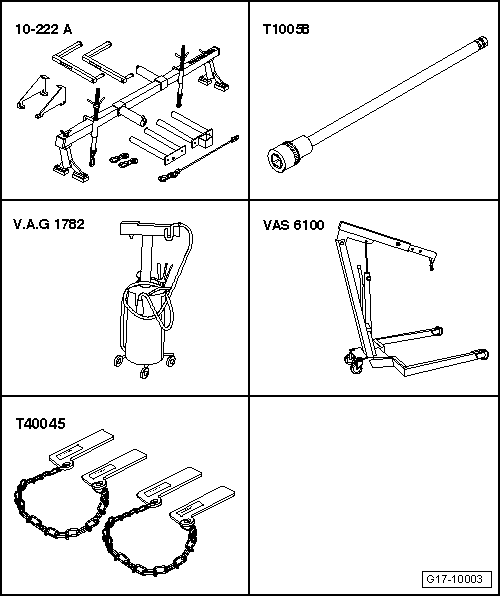
Special tools and workshop equipment required |
t | Support bracket -10 - 222 A- |
t | Allen key (long reach) -T10058- |
t | Used oil collection and extraction unit -V.A.G 1782- |
t | Workshop hoist -VAS 6100- |
t | Mud wing compensation plate -T40045- |
t | Electric drill with plastic brush attachment |
t | Safety goggles |
t | Sealant → Electronic parts catalogue |
![]()
|
|
![]() |
|
![]() |
|
![]() |
|
![]() |
|
![]() |
|
![]() |
|
![]() |
|
![]() |
|
![]() |
|
![]() |
|
![]() |
![]()
|
![]() |
![]()
|
![]() |
|
![]() |
|
![]() |
|
![]() |
|
![]() |
![]()
|
![]() |
|
![]() |
|
![]() |
|
![]() |
|
![]() |
|
![]() |
![]() |
![]() |
![]()
|
![]() |
|
![]() |
![]()
|
![]() |
![]() |
![]() |
|
![]() |
|
![]() |
Component | Nm | |
Sump to: | M7 | 15 |
Cylinder block | M10 | 40 |
Sump to gearbox | 45 | |
Engine mounting to subframe | 23 | |
Engine mounting to engine support | 23 | |
Oil drain plug | 30 | |
Stop for torque reaction support to sump - vehicles up to 05.2003 | 28 | |
Torque reaction support to sump - vehicles from 06.2003 onwards | 23 |