A4 Mk3
Exploded view - output shaft |
Exploded view - removing and installing selector fork cluster, input shaft, 1st, 2nd and reverse gears on output shaft → Chapter |
Dismantling and assembling output shaft → Chapter |

t | Refer to technical data when installing new gears or output shaft → 6-speed manual gearbox 0B1, front-wheel drive; Rep. gr.00. |
t | Lubricate all needle bearings and synchro-rings with gear oil before installing. |
t | When renewing synchro-rings, renew inner ring, intermediate ring and synchro-ring for the corresponding gear together. |
t | If synchro-rings are not being renewed, make sure they are re-installed on the same gear. |
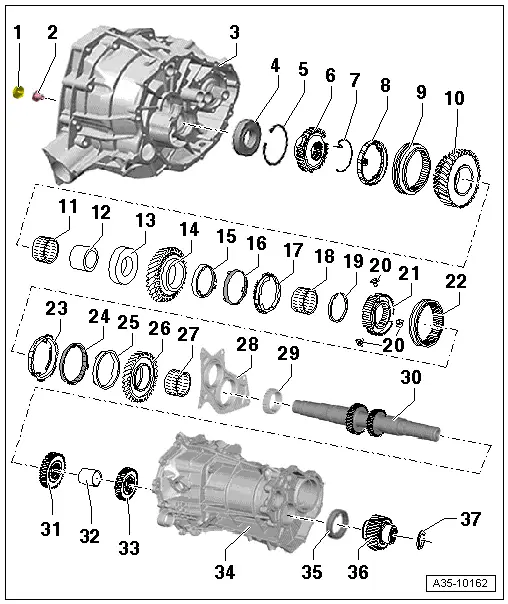
1 - | Sealing cap |
q | With oil guide |
q | For output shaft |
q | Removing and installing → Chapter |
2 - | Bolt |
q | 200 Nm |
q | For output shaft |
q | Apply locking fluid -AMV 185 101 A1- when fitting |
q | To loosen, heat bolt to approx. 80 °C if necessary using hot air blower -V.A.G 1416- |
3 - | Gearbox housing |
4 - | Ball bearing |
q | For output shaft |
q | Removing and installing → Item |
5 - | Circlip |
q | Note installation position → Fig. |
6 - | Reverse gear synchro-hub |
q | Removing and installing → Chapter |
7 - | Synchro-spring |
q | Insert in drilling in reverse gear synchro-hub |
8 - | Synchro-ring for reverse gear |
q | Checking for wear → Fig. |
9 - | Reverse gear locking collar |
q | Installation position → Fig. |
10 - | Reverse selector gear |
q | Installation position → Fig. |
11 - | Needle bearing |
q | For reverse gear |
12 - | Needle bearing inner race |
q | For reverse gear |
q | Removing and installing → Chapter |
13 - | Thrust washer |
q | For 1st speed and reverse selector gears |
14 - | 1st speed selector gear |
15 - | Inner ring for 1st gear |
q | Installation position → Fig. |
q | Distinguishing inner rings for 1st and 2nd gear → Fig. |
q | Checking for wear → Fig. |
q | Renew if scored or if there are visible traces of wear |
16 - | Intermediate ring for 1st gear |
q | Installation position → Fig. |
q | Checking for wear → Fig. |
17 - | Synchro-ring for 1st gear |
q | Installation position → Fig. |
q | Checking for wear → Fig. |
q | Renew if scored or if there are visible traces of wear |
18 - | Needle bearing |
q | For 1st gear |
19 - | Circlip |
q | Determining thickness → Anchor |
20 - | Thrust block |
q | 3x |
q | Installing → Fig. |
21 - | Synchro-hub for 1st and 2nd gear |
q | Installation position → Fig. |
22 - | Locking collar for 1st and 2nd gear |
q | Installation position → Fig. |
23 - | Synchro-ring for 2nd gear |
q | Installation position → Fig. |
q | Checking for wear → Fig. |
q | Renew if scored or if there are visible traces of wear |
24 - | Intermediate ring for 2nd gear |
q | Installation position → Fig. |
q | Checking for wear → Fig. |
25 - | Inner ring for 2nd gear |
q | Installation position → Fig. |
q | Distinguishing inner rings for 1st and 2nd gear → Fig. |
q | Renew if scored or if there are visible traces of wear |
26 - | 2nd speed selector gear |
27 - | Needle bearing |
q | For 2nd gear |
28 - | Bearing mounting |
q | Carries bearings for input shaft and output shaft in gearbox cover |
q | → Item |
29 - | Roller bearing |
q | For output shaft |
q | Pressing off → Fig. |
q | Pressing on → Fig. |
q | Always renew |
30 - | Output shaft |
q | With splines for 5th and 6th gear |
31 - | 3rd gear wheel |
q | Pressing off → Fig. |
q | Installation position: high inside collar faces 4th gear |
q | Pressing on → Fig. |
32 - | Spacer sleeve |
33 - | 4th gear wheel |
q | Pressing off → Fig. |
q | Installation position: high inside collar faces spur gear → Item |
q | Pressing on → Fig. |
34 - | Gearbox cover |
35 - | Roller bearing |
q | Bearing for spur gear in gearbox cover |
q | Removing and installing → Item |
36 - | Spur gear |
q | Drive gear for side shaft / pinion shaft (spur gearing) |
q | Removing and installing → Chapter |
37 - | Circlip |
q | Determining thickness → Anchor |
q | Fit in annular groove on output shaft |
|
![]() |
|
![]() |
|
![]() |
Gap -a- | Wear limit |
Inner ring for 1st gear | 0.6 mm |
![]()
|
![]() |
Gap -a- | Wear limit |
1st and 2nd gear | 0.7 mm |
![]()
|
|
![]() |