LW2 V6-3.0L VIN R (2000)
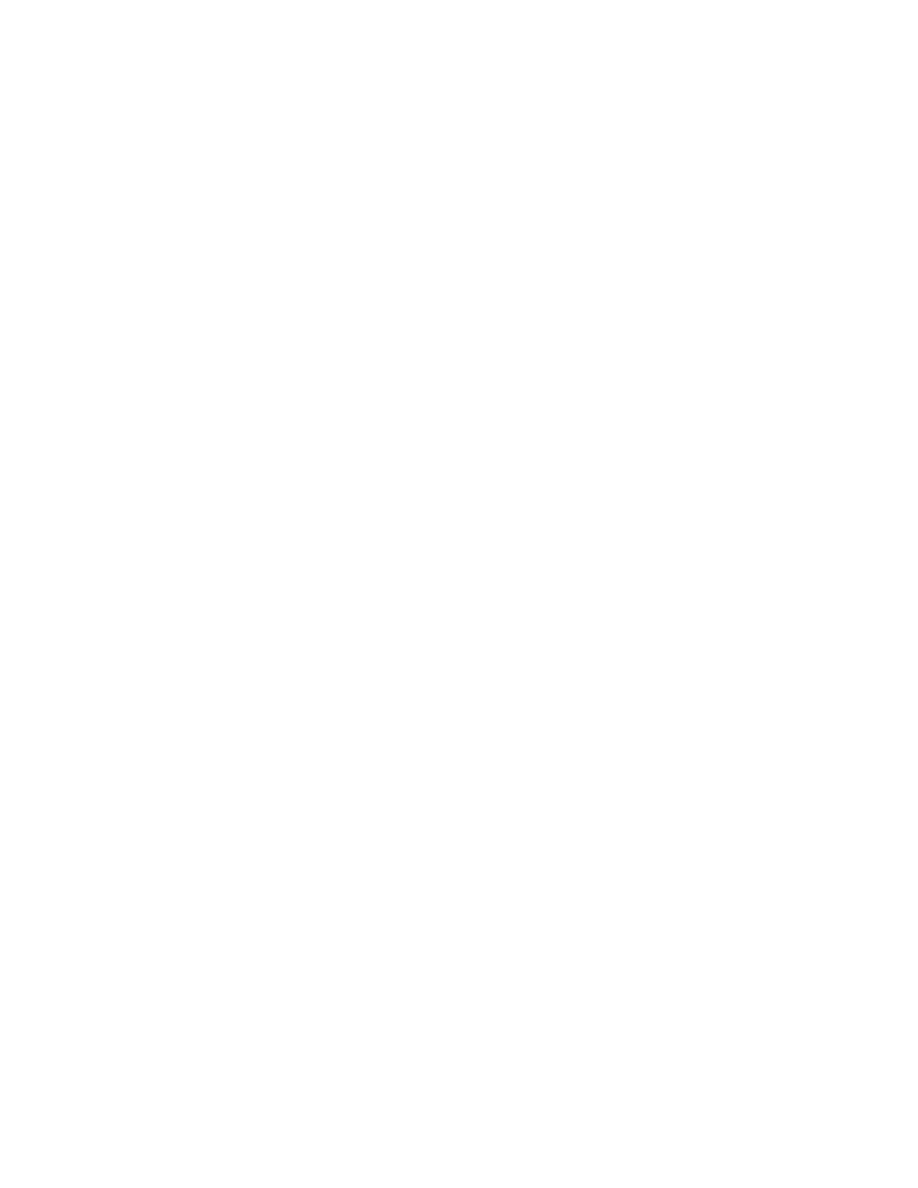
metal-to-metal contact areas between pads, pad guides, caliper and knuckles are clean and lubricated with a thin layer of high temperature silicone
grease. Brake noise is caused by a "slip-stick" vibration of brake components. While intermittent brake noise may be normal, performing 3 -4 aggressive
stops may temporarily reduce or eliminate most brake squeal. If the noise persists, a brake dampening compound may be applied to the back of each pad.
This allows parts to slide freely and not vibrate when moving relative to each other.
The following noises are characteristics of all braking systems and are unavoidable. They may not indicate improper operation of the brake system.
Squeak/Squeal Noise:
-
Occurs with front semi-metallic brake pads at medium speeds when light to medium pressure is applied to the brake pedal.
-
Occasionally a noise may occur on rear brakes during the first few stops or with cold brakes and/or high humidity.
Grinding Noise:
-
Common to rear brakes and some front disc brakes during initial stops after the vehicle has been parked overnight.
-
Caused by corrosion on the metal surfaces during vehicle non-use. Usually disappears after a few stops.
Groan Noise:
A groan type noise may be heard when stopping quickly or moving forward slowly from a complete stop. This is normal. On vehicles equipped with
ABS, a groan or moan type noise during hard braking applications or loose gravel, wet or icy road conditions is a normal function of the ABS activation.
Frequently Asked Questions
KEY POINTS - FREQUENTLY ASKED QUESTIONS
-
Q: Which lathe is essential for performing brake work, the bench or on-car?
A: Dealers must have a well maintained bench lathe and well maintained on-car lathe. These lathes need to be calibrated on a monthly basis.
BOTH lathes are essential to providing quality brake service.
-
Q: Why is it necessary to use a dial indicator to check runout?
A: Both the bench lathe and the on-car lathe will yield EXCELLENT results, but NO LATHE guarantees that the "installed rotor" will meet GM's
lateral runout specification. This is why GM insists on the dial indicating of all rotors.
-
Q: When should the measurement be taken using a dial indicator?
A: ALL rotors are to be dial indicated after resurfacing and mounting on the vehicle hub, regardless of whether the technician uses the bench lathe
or the on-car lathe.
-
Q: What is the expected tip life for an on-car lathe?
A: The geometry and composition of the Pro-Cut tips are designed for "single pass" cutting. When using the Pro-Cut the cutting depth should be
set to take all material needed to get below rust grooves, eliminate all run-out and resurface the entire disc in a single pass. Cuts of 0.1016-0.381
mm (0.004-0.015 in) will provide the best surface finish and the optimal tip life. No "skim cut" or "finish cut" is needed. Failure to follow this
procedure will shorten tip life. The Pro-Cut tips will last between 7-12 cuts per corner. With three usable corners, a pair of tips is good for at least
21 cuts.
-
Q: Why does GM recommend the use of single-pass (referred to as "positive rake") bench and on-car brake lathes?
A: GM Service and GM Brake Engineering have performed competitive evaluations on a significant number of bench and on-car brake lathes.
These tests measured critical performance characteristics such as flatness, surface finish and the ability of the lathe to repeat accuracy over many
uses. In each test, single-pass lathe designs out-performed the competitors. Single-pass brake lathes are more productive requiring less time to
perform the same procedure.
-
Q: Is it OK to leave the caliper/pads installed while cutting rotors using an on-car lathe?
A: On-car lathes should never be used with the pads and calipers installed on the vehicle. The debris from cutting the rotors can contaminate the
brake pads/calipers which can lead to other brake concerns and comebacks.
-
Q: What is the best way to correct for excessive lateral runout on vehicles with hubless rotors?
A: Regardless of the type of lathe used to resurface hubless rotors, on-car or bench lathe, the preferred method to correct for excessive lateral
runout is the Brake Align Runout Correction Plate System. This warranty policy for correction of lateral runout applies to ALL model vehicle,
therefore it is essential to inventory a FULL assortment of Brake Align Correction Plates, and a full assortment of sizes, (.003",.006", and.009").
-
Q: Is it necessary to measure for LRO on new OEM rotors?
A: All new GM rotors must also be dial indicated after installation. New rotors are NEVER to be resurfaced on any type of lathe.
-
Q: What labor operation can be used to claim the time for measuring and/or correcting for LRO?
A: Applicable labor operations include the time for performing a final LRO measurement in the base time allowance. Refer to the "Warranty
Information" section of this bulletin in instances where additional time for correcting LRO to meet specification is necessary.
-
Q: What information needs to be documented on the customer service order?
A: Any claim that is submitted using the labor operations in this bulletin, must have the Original Rotor Thickness, Refinish Rotor Thickness and
LRO documented on the customer service order. For more information, refer to the "Customer Service Order / Warranty Claim Required
Documentation" section of this bulletin.
All Warranty customer service orders paid by GM, are subject to review for compliance, documentation of lateral runout measurements and the
use of Brake Align Plates and may be debited where the repair does not comply with this procedure.
Brake Warranty
BRAKE WARRANTY