Leon Mk2
Dismantling and assembling output shaft for 3rd and 4th gear |
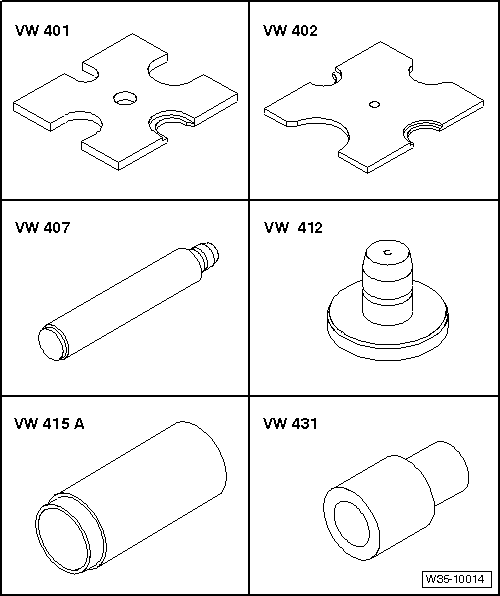
Special tools and workshop equipment required |
t | Pressure plate -VW 401- |
t | Pressure plate -VW 402- |
t | Press die. -VW 407- |
t | Press die. -VW 412- |
t | Tube -VW 415 A- |
t | Thrust piece -VW 431- |
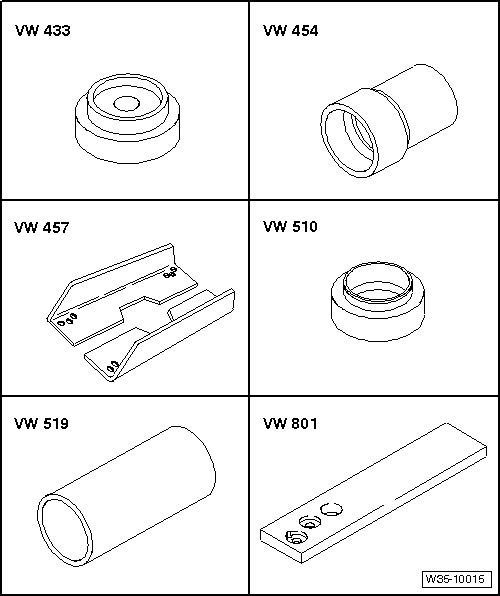
t | Thrust piece -VW 433- |
t | Thrust piece -VW 454- |
t | Support rails -VW 457- |
t | Thrust pad -VW 510- |
t | Tube -VW 519- |
t | Support plate -VW 801- |
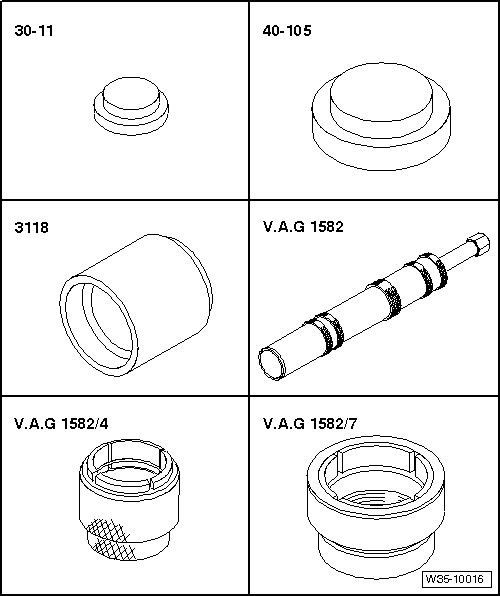
t | Tightening plate -30 - 11- |
t | Tightening plate -40 - 105- |
t | Thrust piece -3118- |
t | Roller bearing bush extractor -V.A.G 1582- |
t | Adapter -V.A.G 1582/4- |
t | Adapter -V.A.G 1582/7- |
|
|
![]() |
|
![]() |
![]()
|
![]() |
|
![]() |
|
![]() |
Dimension -a- | Installation dimension | Wear limit |
3rd and 4th gears | 0.75 … 1.25 mm | 0.3 mm |
|
![]() |
Dimension -a- | Installation dimension | Wear limit |
3rd gear | 1.0 … 1.8 mm | 0.5 mm |
4th gear | 1.0 … 1.9 mm | 0.5 mm |
|
|
![]() |
|
![]() |
|
![]() |
|
![]() |
|
![]() |
|
![]() |
|
![]() |
|
![]() |
|
![]() |
![]()
|
![]() |
![]()
|
![]() |
|
![]() |
|
![]() |
|
![]() |
|
![]() |
|
![]() |
|
![]() |