Golf Mk4
Dismantling and assembling differential |
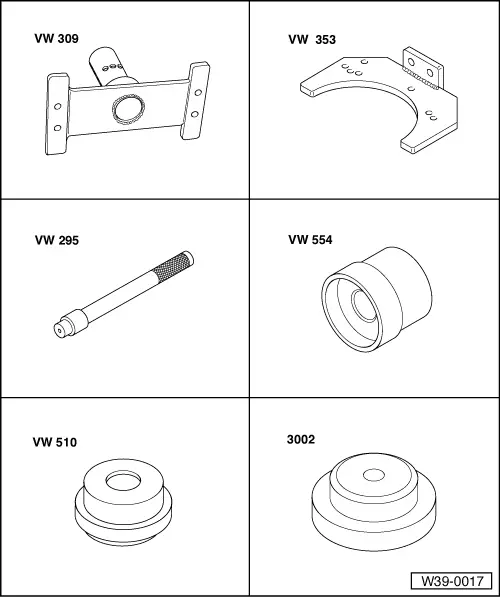
Special tools and workshop equipment required |
t | Support plate -VW 309- |
t | Gearbox support -VW 353- |
t | Drift -VW 295- |
t | Thrust piece -VW 554- |
t | Thrust pad -VW 510- |
t | Thrust piece -3002- |

t | Puller -V.A.G 1582- |
t | Grip -V.A.G 1582/3- |
t | Press tool -VW 412- |
t | Thrust piece -VW 454- |
t | Thrust plate -VW 401- |
t | Thrust plate -VW 402- |
|
|
![]() |
|
![]() |

t | Heat tapered roller bearing inner race to 100° C before installing. |
t | Always renew both tapered roller bearings together as a set. |
t | If tapered roller bearings, differential cage, gearbox housing or clutch housing are renewed, adjust differential → Chapter. |
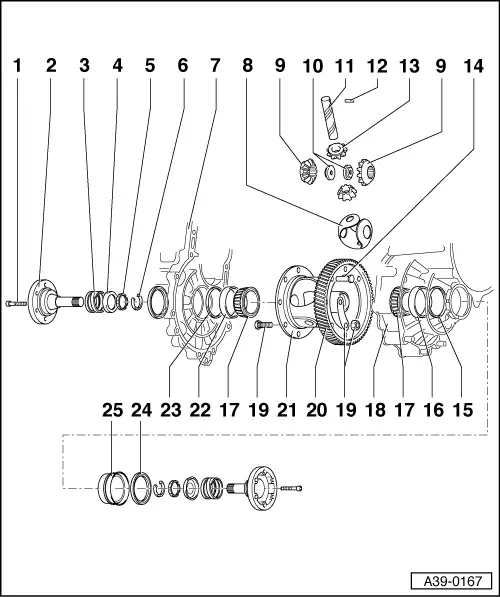
1 - | Hexagon socket head bolt, 25 Nm |
q | Screw into threaded piece → Item. |
2 - | Flange shaft |
q | Removing and installing → Chapter |
3 - | Compression spring for flange shaft |
q | Installed behind flange shafts |
4 - | Thrust washer |
q | Installation position: shoulder faces spring, lugs face tapered ring |
5 - | Tapered ring |
q | With grooves to engage in thrust washer |
q | Installation position: taper towards differential cage |
6 - | Retaining ring |
q | Holds tapered ring, thrust washer and spring in position when flange shaft is removed. |
7 - | Gearbox housing |
8 - | One-piece thrust washer |
q | Coat with gearbox oil when installing |
9 - | Large differential bevel gear |
q | Installing → Fig. |
10 - | Threaded piece |
q | Installing → Fig. |
11 - | Differential pinion pin |
q | Drive out using drift |
q | Installing → Fig. |
12 - | Spring pin |
q | For securing differential pinion pin |
q | Removing and installing → Fig.. |
13 - | Small differential bevel gear |
q | Installing → Fig. |
14 - | Rivet |
q | Only in production |
q | Drilling out → Fig. |
15 - | Shim S2 |
q | Always 1 mm thick |
16 - | Tapered roller bearing outer race |
q | Driving out → Fig.. First remove sleeve ( → Item). |
q | Driving in → Fig. |
17 - | Tapered roller bearing inner race |
q | Pulling off → Fig. |
q | Pressing on → Fig. |
18 - | Clutch housing |
19 - | Repair kit |
q | Only for Service department. |
q | Installing → Fig. |
q | Hexagon nut, 65 Nm |
20 - | Final drive gear wheel |
q | Riveted in production. |
q | Paired with output shaft. Renew only as a set. |
q | Pressing off → Fig.. |
q | Installation position → Fig. |
q | Heat to 100 °C before installing. |
q | Fit to differential cage → Fig. |
q | Bolted → Fig.. |
21 - | Differential cage |
22 - | Tapered roller bearing outer race |
q | Driving out → Fig. |
q | Driving in → Fig. |
23 - | Shim S1 |
q | Determining thickness → |
24 - | Seal |
q | Renewing → Chapter |
25 - | Sleeve |
q | To support oil seal. |
q | Removing and installing → Fig. |
|
![]() |
|
![]() |
![]()
|
![]() |
|
![]() |
|
![]() |
![]()
|
![]() |
|
![]() |
|
![]() |
|
![]() |
|
![]() |
|
![]() |
|
![]() |