Golf Mk4
Repairing valve gear |

t | Cylinder heads which have cracks between the valve seats or between a valve seat insert and the spark plug thread can be used further without reducing service life, provided the cracks do not exceed a maximum of 0.3 mm in width, or when no more than the first 4 turns of the spark plug thread are cracked. |
t | When new bucket tappets have been installed the engine must not be started for about 30 minutes. (Otherwise valves will contact pistons.) Then turn crankshaft two full revolutions. |
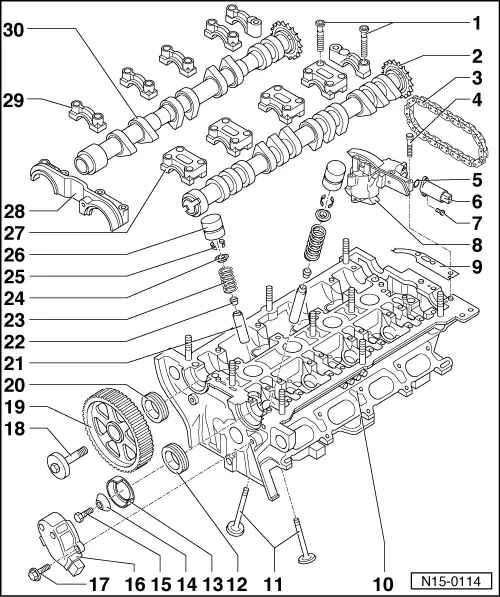
1 - | 10 Nm |
2 - | Inlet camshaft |
q | Checking axial clearance → Fig.. |
q | Removing and installing → Chapter. |
q | Check radial clearance with plastigage, wear limit: 0.1 mm. |
q | Runout: max. 0.01 mm. |
3 - | Drive chain |
q | Before removing, mark direction of rotation (installation position) → Chapter. |
4 - | 10 Nm |
5 - | O-ring |
q | Renew. |
6 - | Inlet camshaft control valve 1 -N205- |
q | Only engine codes AGN, AUM, AUQ. |
7 - | 3 Nm |
q | Only engine codes AGN, AUM, AUQ. |
8 - | Camshaft adjuster |
q | Only engine codes AGN, AUM, AUQ. |
q | Engine codes AGU, AQA, ARZ: chain tensioner. |
q | Before removing, lock in position with chain tensioner retainer -3366- → Chapter. |
9 - | Gasket |
q | Rubber/metal gasket. |
q | Renew. |
10 - | Cylinder head |
q | Reworking valve seats → Chapter. |
q | Reworking sealing surface → Fig.. |
q | Sealing transition points → Fig. and → Fig.. |
11 - | Valves |
q | Do not rework, only lapping-in is permitted. |
q | Valve dimensions → Fig.. |
q | Exhaust valves with sodium filling: Observe disposal instructions → Fig.. |
12 - | Seal |
q | Renew → Chapter. |
13 - | Screen |
q | For Hall sender -G40- / Hall sender 2 -G163-. |
q | When installing note fixing arrangement. |
14 - | Washer |
q | Conical. |
15 - | 25 Nm |
16 - | Hall sender -G40- / Hall sender 2 -G163- |
17 - | 10 Nm |
18 - | 65 Nm |
q | Use counterhold tool -3036- to loosen and tighten. |
19 - | Camshaft pulley |
q | Observe installation position: the small web of camshaft pulley faces outwards and the TDC mark for No. 1 cylinder is visible. |
20 - | Seal |
q | Renew → Chapter. |
21 - | Valve guide |
q | Checking → Chapter. |
22 - | Valve stem seal |
q | Renew → Chapter. |
23 - | Valve spring |
q | Removing and installing: cylinder head removed: use valve spring tool -3362-, installed: → Chapter. |
24 - | Valve spring plate |
25 - | Cotters |
26 - | Bucket tappet |
q | Do not interchange. |
q | With hydraulic valve clearance compensation. |
q | Checking → Chapter. |
q | Store with cam contact surface downwards. |
q | Before installing check camshaft axial clearance → Fig.. |
q | Oil contact surface. |
27 - | Inlet camshaft bearing cap |
q | Installation position and installation sequence → Chapter |
28 - | Double bearing cap |
q | Must seat on dowel sleeves. |
q | Lightly coat contact surfaces with sealant -AMV 174 004 01-, observe installation position and installation sequence → Chapter. |
q | Sealing transition points between double bearing cap and cylinder head → Fig.. |
29 - | Exhaust camshaft bearing cap |
q | Installation position and installation sequence → Chapter |
30 - | Exhaust camshaft |
q | Checking axial clearance → Fig.. |
q | Removing and installing → Chapter. |
q | Check radial clearance with plastigage, wear limit: 0.1 mm. |
q | Runout: max. 0.01 mm. |
|
![]() |
![]()
|
![]() |
Dimension | Inlet valve | Exhaust valve | |
Ø a | mm | 26.9 | 29.9 |
Ø b | mm | 5.963 | 5.943 |
c | mm | 104.84...105.34 | 103.64...104.14 |
α | ∠° | 45 | 45 |
![]()
|
|
![]() |
|
![]() |