A2
Pistons and conrods - exploded view |
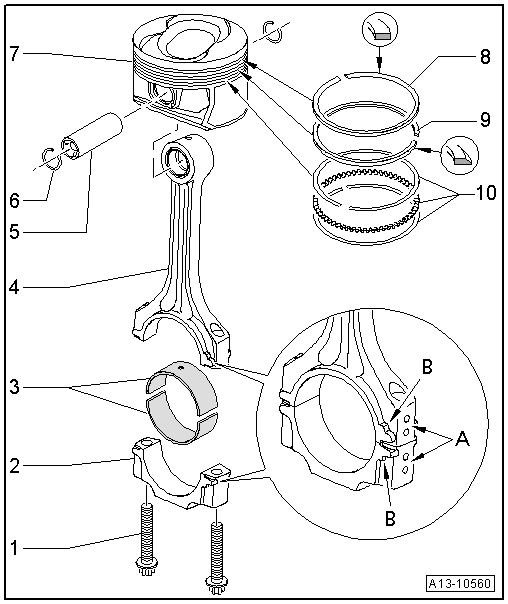
1 - | Bolt |
q | Renew |
q | Lubricate threads and contact surface |
q | 30 Nm + turn 90° further |
q | When measuring radial clearance, tighten used bolt to 30 Nm but not further |
2 - | Conrod bearing cap |
q | Mark cylinder allocation before removing -A- |
q | Installation position: marking -B- faces towards pulley end (apply marking before removal if no marking is visible) |
3 - | Bearing shells |
q | Upper bearing shell with oil hole for piston pin lubrication |
q | Mark used bearing shells for re-installation but not on bearing surface |
q | Measuring preload → Fig. |
4 - | Conrod |
q | Only renew as a complete set |
q | Mark cylinder allocation before removing -A- |
q | Installation position: marking -B- faces towards pulley end (apply marking before removal if no marking is visible) |
q | Guided axially via piston |
q | Measuring radial clearance → Chapter |
5 - | Piston pin |
q | If difficult to remove, heat piston to 60 °C |
q | Remove and install using drift -VW 222 A- |
6 - | Circlip |
q | Renew |
7 - | Piston |
q | Checking → Fig. |
q | Mark installation position and cylinder number |
q | Installation position: arrow on piston crown points to pulley end |
q | Install using piston ring clamp |
q | Checking cylinder bore → Fig. |
q | Piston and cylinder dimensions → Chapter |
8 - | Compression ring |
q | Use piston ring pliers to remove and install |
q | Pay attention to cross section |
q | Offset gap by 120° to next compression ring |
q | Inscription „TOP“ faces towards piston crown |
q | Checking ring gap → Fig. |
q | Checking ring-to-groove clearance → Fig. |
9 - | Compression ring |
q | Use piston ring pliers to remove and install |
q | Pay attention to cross section |
q | Offset gap 120° relative to adjacent oil scraper ring |
q | Inscription „TOP“ faces towards piston crown |
q | Checking ring gap → Fig. |
q | Checking ring-to-groove clearance → Fig. |
10 - | Oil scraper ring |
q | 3 parts |
q | Offset gap of top steel element of piston ring by 120° to next compression ring |
q | Offset gaps of individual parts of oil scraper ring |
q | Checking ring gap → Fig. |
q | Ring-to-groove clearance cannot be checked |
Piston ring Dimensions in mm | New | Wear limit |
1st compression ring | 0.20 … 0.50 | 1.00 |
2nd compression ring | 0.40 … 0.70 | 1.00 |
Oil scraper ring | 0.40 … 1.40 | No wear limit data available |
|
![]() |
Piston ring Dimensions in mm | New | Wear limit |
1st compression ring | 0.04 … 0.08 | 0.15 |
2nd compression ring | 0.04 … 0.08 | 0.15 |
Oil scraper ring | Cannot be measured |
|
![]() |
![]()
|
![]() |
|
![]() |