A3 Mk2
Removing gearbox (vehicles with 2.0 ltr. TDI common rail engine) |
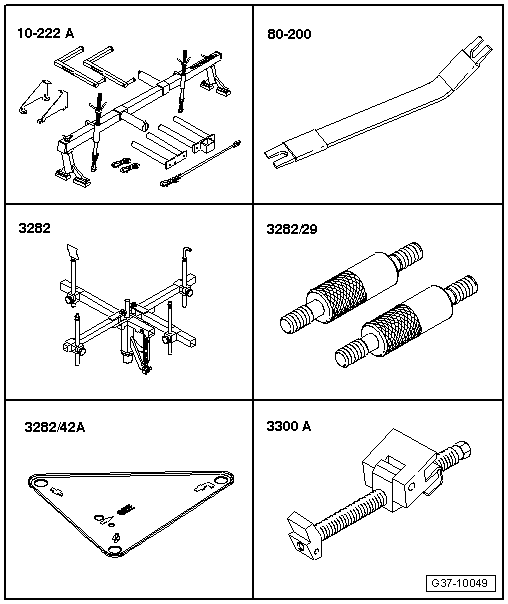
Special tools and workshop equipment required |
t | Support bracket -10 - 222 A- |
t | Removal lever -80 - |
t | Gearbox support -3282- |
t | Pin -3282/29- |
t | Adjustment plate -3282/42 A- |
t | Engine support -3300 A- |
|
|
![]() |
|
![]() |
|
![]() |
![]()
|
![]() |
![]()
|
![]() |
|
![]() |
![]()
|
![]() |
|
![]() |
|
![]() |
![]()
|
![]() |
![]()
|
![]() |
|
![]() |
|
![]() |
|
![]() |
![]()
|
![]() |
|
![]() |
|
![]() |
|
![]() |
|
![]() |
![]()
|
![]() |
|
![]() |
|
![]() |
|
![]() |
|
![]() |
|
![]() |
|
![]() |
|
![]() |
![]()
|
![]() |
|
![]() |
|
![]() |
|
![]() |
|
![]() |
![]() |
![]() |
![]() |
![]() |
|
![]() |
|
![]() |
|
![]() |