A3 Mk2
Valve gear - exploded view |
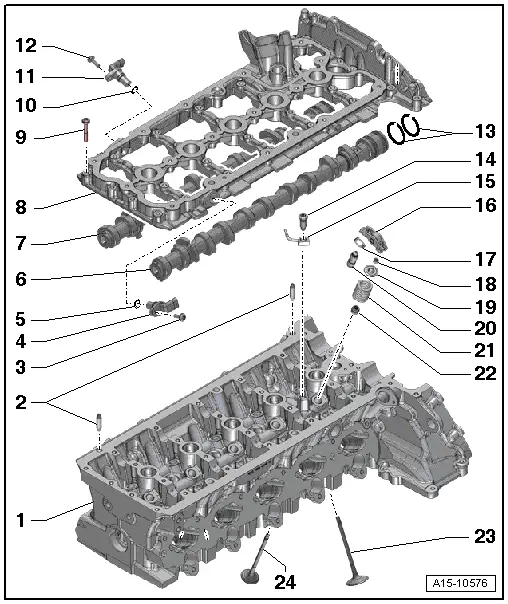
1 - | Cylinder head |
q | Checking valve guides → Chapter |
2 - | Dowel pins |
3 - | Bolt |
q | Tightening torque → Rep. gr.28 |
4 - | Hall sender 3 -G300- |
q | Exhaust side |
q | Removing and installing → Rep. gr.28 |
5 - | O-ring |
q | Renew |
6 - | Inlet camshaft |
q | Removing and installing → Chapter |
q | Measuring axial clearance → Chapter |
q | Measuring radial clearance → Chapter |
q | Runout: max. 0.04 mm |
7 - | Exhaust camshaft |
q | With additional cam for high-pressure pump |
q | Removing and installing → Chapter |
q | Measuring axial clearance → Chapter |
q | Measuring radial clearance → Chapter |
q | Runout: max. 0.04 mm |
8 - | Retaining frame |
q | With integrated camshaft bearings |
9 - | Bolt |
q | To avoid damage to retaining frame for camshafts, refer to tightening torque and sequence → Fig. |
10 - | O-ring |
q | Renew |
11 - | Hall sender -G40- |
q | Inlet side |
q | Removing and installing → Rep. gr.28 |
12 - | Bolt |
q | Tightening torque → Rep. gr.28 |
13 - | Rectangular section seals |
14 - | Bolt |
q | With pressure relief valve |
q | 27 Nm |
15 - | Oil spray jet |
16 - | Roller rocker finger |
q | Mark installation position for re-installation |
q | Check roller bearings for ease of movement |
q | Lubricate contact surface before installing |
q | Assembly: attach to hydraulic compensation element -item 20- using securing clip -item 17- |
17 - | Securing clip |
q | Not supplied separately |
q | Check for firm attachment |
18 - | Valve cotters |
19 - | Valve spring plate |
20 - | Hydraulic valve compensation element |
q | Clipped into roller rocker finger -item 16- |
q | Checking → Chapter |
q | Mark installation position for re-installation |
q | Lubricate contact surface before installing |
21 - | Valve spring |
q | Installation position → Fig. |
22 - | Valve stem oil seal |
q | Renewing with cylinder head installed → Chapter |
q | Renewing with cylinder head removed → Chapter |
23 - | Inlet valve |
q | Must not be machined; only grinding-in is permissible |
q | Mark installation position for re-installation |
q | Checking → Chapter |
q | Valve dimensions → Chapter |
q | Checking valve guides → Chapter |
24 - | Exhaust valve |
q | Must not be machined; only grinding-in is permissible |
q | Mark installation position for re-installation |
q | Checking → Chapter |
q | Valve dimensions → Chapter |
q | Checking valve guides → Chapter |
|
![]() |
Stage | Bolts | Tightening torque/angle specification | ||
1. | -1 … 29- | Screw in by hand until bolt heads make contact with retaining frame | ||
2. | -1 … 29- | Continue tightening 1 turn at a time in several stages until retaining frame makes full contact with cylinder head and a torque of 8 Nm is reached | ||
3. | -1 … 29- | 8 Nm 1) | ||
4. | -1 … 29- | turn 90° further | ||
|