A4 Mk2
Dismantling and assembling pinion shaft and hollow shaft |
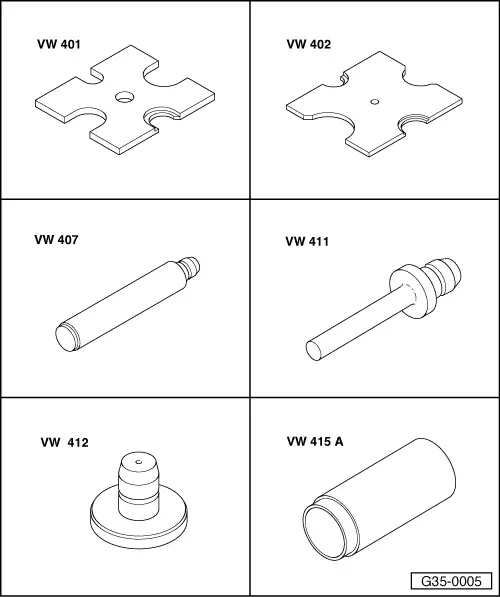
Special tools and workshop equipment required |
t | Thrust plate -VW 401- |
t | Thrust plate -VW 402- |
t | Press tool -VW 407- |
t | Press tool -VW 411- |
t | Press tool -VW 412- |
t | Tube -VW 415 A- |
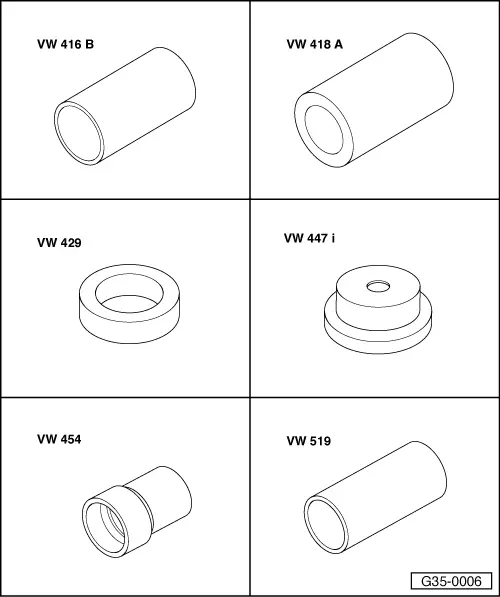
t | Tube -VW 416 B- |
t | Tube -VW 418 A- |
t | Thrust ring -VW 429- |
t | Thrust plate -VW 447 i- |
t | Press tool -VW 454- |
t | Tube -VW 519- |
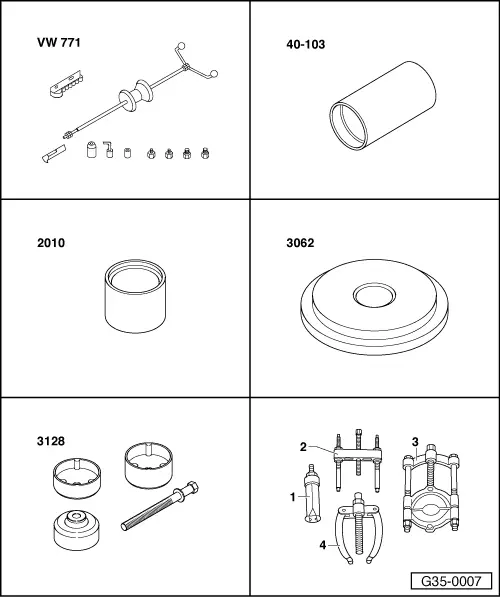
t | Multi-purpose tool -VW 771- |
t | Support -40 - 103- |
t | Tube -2010- |
t | Thrust pad -3062- |
t | Fitting tool -3128- |
t | -1-Internal puller -Kukko 21/1- |
t | -3-Splitter -Kukko 17/2- |

t | Refer to technical data → Chapter when installing new gear wheels or the final drive gear set. |
t | Adjustment work is required when renewing the parts marked with 1) → Chapter. |
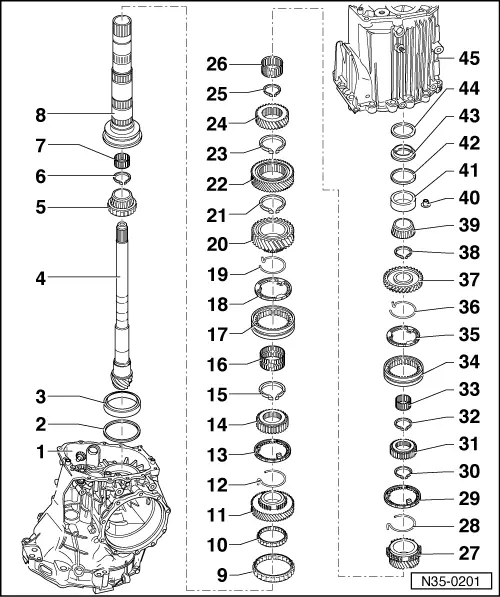
1 - | Gearbox housing 1) |
2 - | Shim “S3” |
q | Table of adjustments → Chapter |
3 - | Double tapered roller bearing outer race 1) |
q | Renew together with → Item |
q | Pulling out → Fig. |
q | Pressing in → Fig. |
4 - | Pinion shaft 1) |
q | Is mated with crown wheel, always renew together as a set |
q | Adjusting pinion shaft and crown wheel → Chapter |
5 - | Double tapered roller bearing inner race 1) |
q | Renew |
q | Will be damaged during removal |
q | Pressing off → Fig. |
q | Pressing on → Fig. |
6 - | Circlip |
q | Redetermine thickness if double tapered roller bearing is renewed → Fig. |
7 - | Needle bearing |
q | For pinion shaft in hollow shaft |
q | Lubricate with MoS2 grease |
8 - | Hollow shaft 1) |
9 - | Needle bearing for 1st gear |
10 - | Needle bearing for 1st gear |
11 - | 1st speed selector gear |
12 - | Spring |
q | Insert in 1st speed selector gear → Fig. |
q | Allocation to selector gear → Electronic parts catalogue |
13 - | Synchro-ring for 1st gear |
q | Checking for wear → Fig. |
14 - | Synchronising hub for 1st and 2nd gear |
q | Pressing off → Fig. |
q | Pressing on → Fig. |
15 - | Circlip |
q | Mark |
q | Installation position → Fig. |
q | Redetermine thickness if synchronising hub is replaced → Fig. |
16 - | Needle bearing for 2nd gear |
17 - | Locking collar for 1st and 2nd gear |
q | Installation position → Fig. |
18 - | Synchro-ring for 2nd gear |
q | Checking for wear → Fig. |
19 - | Spring |
q | Insert in 2nd speed selector gear → Fig. |
q | Allocation to selector gear → Electronic parts catalogue |
20 - | 2nd speed selector gear |
21 - | Circlip |
q | Mark |
q | Installation position → Fig. |
22 - | 3rd gear wheel |
q | Pressing off → Fig. |
q | Pressing on → Fig. |
23 - | Circlip |
q | Mark |
q | Installation position → Fig. |
q | If the 3rd gear wheel is renewed determine thickness of required new circlip → Fig. |
24 - | 4th gear wheel |
q | Pressing off → Fig. |
q | Pressing on → Fig. |
25 - | Circlip |
q | Mark |
q | Installation position → Fig. |
q | If the 4th gear wheel is renewed determine thickness of required new circlip → Fig. |
26 - | Needle bearing |
27 - | 5th speed selector gear |
28 - | Spring |
q | Insert in 5th speed selector gear → Fig. |
q | Allocation to selector gear → Electronic parts catalogue |
29 - | Synchro-ring for 5th gear |
q | Checking for wear → Fig. |
30 - | Circlip |
q | Mark |
q | Installation position → Fig. |
31 - | 5th gear and reverse gear synchronising hub |
q | Pressing off → Fig. |
q | Pressing on → Fig. |
32 - | Circlip |
q | Mark |
q | Installation position → Fig. |
q | Redetermine thickness if synchronising hub is replaced → Fig. |
33 - | Needle bearing |
q | For reverse gear |
34 - | 5th and reverse gear locking collar |
q | Installation position → Fig. |
35 - | Synchro-ring for reverse gear |
q | Checking for wear → Fig. |
36 - | Spring |
q | Insert in reverse selector gear → Fig. |
q | Allocation to selector gear → Electronic parts catalogue |
37 - | Reverse selector gear |
38 - | Circlip |
q | Mark |
q | Installation position → Fig. |
39 - | Tapered roller bearing inner race 1) |
q | Pressing off → Fig. |
q | Pressing on → Fig. |
40 - | Bush |
q | Secures outer race for small tapered roller bearing |
q | Pulling out → Fig. |
q | Need not be fitted after the small tapered roller bearing has been renewed |
41 - | Tapered roller bearing outer race 1) |
q | Pressing out → Fig. |
q | Pressing in → Fig. |
42 - | Shim “S4” |
q | Table of adjustments → Chapter |
43 - | Ring |
q | For rubber washer |
q | For correct version, refer to → Electronic parts catalogue |
44 - | Rubber washer |
q | Compensates length variations |
q | For correct version, refer to → Electronic parts catalogue |
45 - | Gearbox cover |
|
![]() |
|
![]() |
|
![]() |
|
![]() |
|
![]() |
|
![]() |
|
![]() |
|
![]() |
|
![]() |
|
![]() |
|
![]() |
|
![]() |
|
![]() |
|
![]() |
Circlip thickness (mm) | ||
1.90 | 1.96 | 2.02 |
1.93 | 1.99 |
|
Circlip thickness (mm) | ||
2.50 |
|
![]() |
Circlip thickness (mm) | ||
1.90 | 1.98 | 2.06 |
1.94 | 2.02 |
|
Circlip thickness (mm) | ||
1.86 | 1.94 | |
1.90 | 1.98 |
|
Circlip thickness (mm) | ||
2.00 |
|
![]() |
Circlip thickness (mm) | ||
1.90 | 1.96 | 2.02 |
1.93 | 1.99 | 2.05 |
|
Circlip thickness (mm) | ||
2.50 |
|
|
![]() |
|
![]() |
|
![]() |
|
![]() |
|
![]() |
|
![]() |
|
![]() |
|
![]() |
|
![]() |
A | Reverse gear wheel with chamfered surface | Both types of locking collar can be installed (with chamfered surface or with large shoulder) |
B | Reverse gear wheel without chamfered surface | Install only locking collar with large shoulder; do not use locking collar with chamfered edge |