A4 Mk2
Dismantling and assembling pinion shaft |
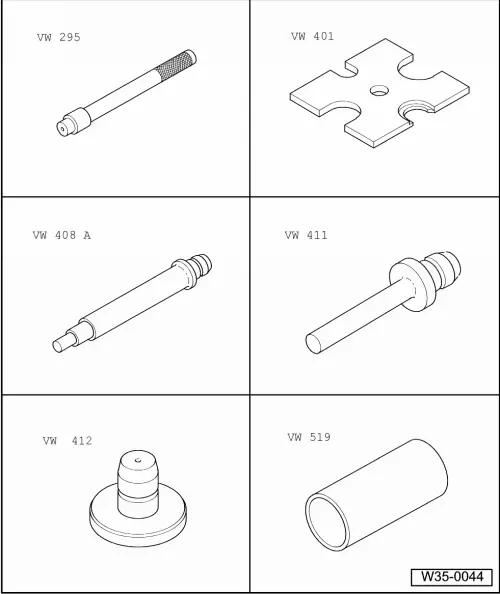
Special tools and workshop equipment required |
t | Drift -VW 295- |
t | Thrust plate -VW 401- |
t | Press tool -VW 408 A- |
t | Press tool -VW 411- |
t | Press tool -VW 412- |
t | Tube -VW 519- |
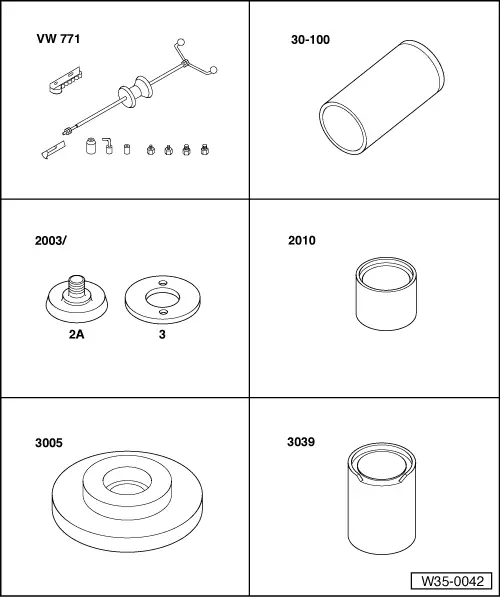
t | Multi-purpose tool -VW 771- |
t | Drift sleeve -30-100- |
t | Installing ring -2003/3- |
t | Tube -2010- |
t | Thrust plate -3005- |
t | Guide sleeve -3039- |
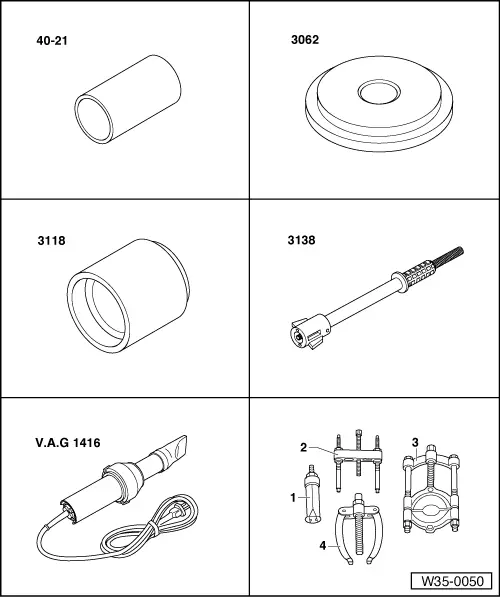
t | Press tool -40-21- |
t | Thrust pad -3062- |
t | Tube -3118- |
t | Drift -3138- |
t | Hot air blower -V.A.G 1416- |
t | -3-Splitter -Kukko 17/2- |
Pinion shaft - exploded view of components |

t | Observe the general repair instructions → Chapter. |
t | When installing new gears → Chapter „Code letters, allocation, transmission ratios, capacities“. |
t | Adjustment is required if pinion shaft, bearing plate or tapered roller bearings are being renewed → Anchor. |
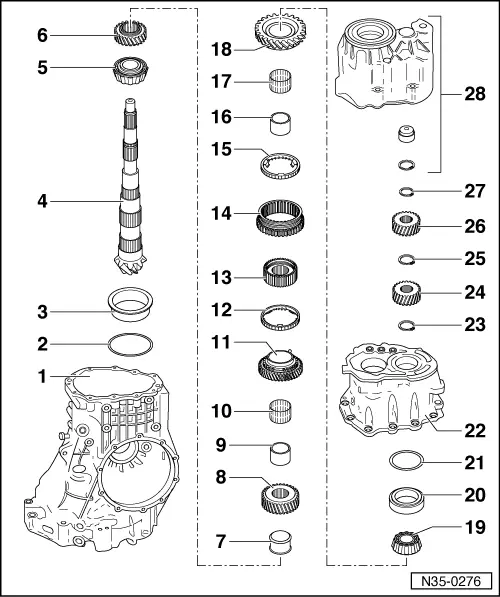
1 - | Gearbox housing |
q | Servicing → Chapter |
2 - | Shim “S3” |
q | Table of adjustments → Anchor |
3 - | Large tapered roller bearing outer race |
q | Pulling out → Fig. |
q | Pressing in → Fig. and → Fig. |
4 - | Pinion shaft |
q | Is mated with crown wheel (final drive gear set), always renew together as a set |
q | Select correct version according to code letters → Parts catalogue |
5 - | Large tapered roller bearing inner race |
q | Pressing off → Fig. |
q | Pressing on → Fig. |
q | Low-friction bearing; do not oil bearing when measuring friction torque |
6 - | 4th gear wheel |
q | Pressing off → Fig. |
q | Pressing on → Fig. |
7 - | Spacer sleeve |
8 - | 3rd gear wheel |
q | Pressing off together with → Item → Fig. |
q | Pressing on → Fig. |
9 - | Inner race for 2nd speed selector gear |
q | Pressing off together with → Item → Fig. |
q | Pressing on → Fig. |
10 - | Needle bearing for 2nd speed selector gear |
q | Lubricate with gear oil before installing |
11 - | 2nd speed selector gear |
q | Pressing off → Fig. |
q | Before installing, fit spring and slide needle bearing onto pinion shaft |
q | After installing, check axial clearance with a feeler gauge (0.15 ... 0.35 mm) |
12 - | Synchro-ring for 2nd gear |
q | With molybdenum coating |
q | Checking for wear → Fig. |
13 - | Synchronising hub for 1st and 2nd gear |
q | Pressing off → Fig. |
q | Pressing on → Fig. |
q | Installation position: flush hub towards 2nd speed selector gear |
14 - | Locking collar for 1st and 2nd gear |
q | Installation position: groove for selector fork faces towards 1st speed selector gear |
15 - | Synchro-ring for 1st gear |
q | Checking for wear → Fig. |
16 - | Inner race for 1st speed selector gear |
q | Pressing off → Fig. |
q | Pressing on → Fig. |
17 - | Needle bearing for 1st speed selector gear |
q | Lubricate with gear oil before installing |
18 - | 1st speed selector gear |
q | Before installing, insert spring → Fig. |
q | After pressing on → Item, check axial clearance with a feeler gauge (0.15 ... 0.50 mm) |
19 - | Small tapered roller bearing inner race |
q | Pressing off → Fig. |
q | Pressing on → Fig. |
q | Low-friction bearing; do not oil bearing when measuring friction torque |
20 - | Small tapered roller bearing outer race |
q | Driving out → Fig. |
q | Pressing in → Fig. |
21 - | Shim “S4” |
q | Table of adjustments → |
22 - | Bearing plate |
q | Servicing → Chapter |
23 - | Circlip |
q | Re-determining thickness → Anchor |
24 - | 6th gear wheel |
q | Pressing off → Anchor |
q | Pressing on → Anchor |
q | Installation position: shoulder towards inner race for small tapered roller bearing |
25 - | Circlip |
q | Re-determining thickness → Anchor |
26 - | 5th gear wheel |
q | Pulling off → Anchor |
q | Driving on → Anchor |
27 - | Circlip |
28 - | End cover |
q | Servicing → Chapter |
![]()
|
![]() |
|
![]() |
|
![]() |
|
![]() |
|
![]() |
|
![]() |
|
![]() |
![]()
|
![]() |
![]()
|
![]() |
|
![]() |
|
![]() |
|
![]() |
|
![]() |
|
![]() |
|
![]() |
|
![]() |
|
![]() |
|
![]() |