A4 Mk2
Dismantling and assembling input shaft |
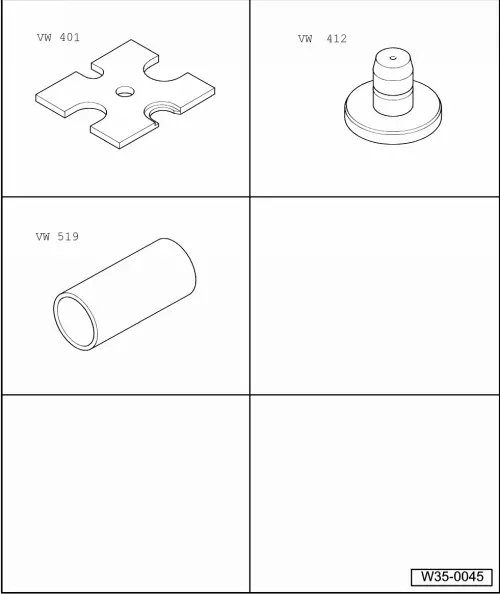
Special tools and workshop equipment required |
t | Thrust plate -VW 401- |
t | Press tool -VW 412- |
t | Tube -VW 519- |
t | Feeler gauge |
Exploded view |

When installing new gears → Chapter „Code letters, allocation, transmission ratios, capacities“. |
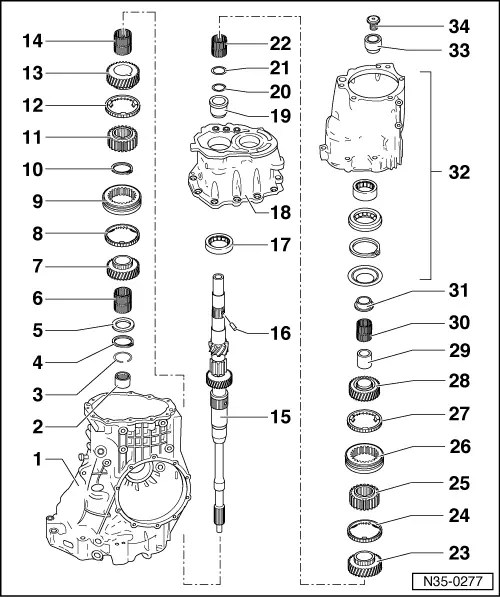
1 - | Gearbox housing |
q | Servicing → Chapter |
2 - | Needle bearing |
q | For input shaft |
q | Pulling out → Fig. |
q | Driving in → Fig. |
3 - | Circlip |
q | For needle bearing |
4 - | Circlip |
q | For input shaft |
5 - | Thrust washer |
6 - | Needle bearing for 4th gear |
q | Mark before removing |
q | Do not interchange with needle bearing for 3rd gear |
q | Lubricate with gear oil before installing |
7 - | 4th speed selector gear |
q | Insert spring before installing → Fig. |
q | After installing, check axial clearance with a feeler gauge (0.15 ... 0.35 mm) |
8 - | Synchro-ring for 4th gear |
q | Checking for wear → Fig. |
9 - | Locking collar |
q | Is paired with synchronising hub |
q | Mark before removing → Anchor |
10 - | Circlip |
q | Redetermine thickness if synchronising hub is being renewed → Fig. |
q | Installation position: ends coincide with groove in synchronising hub |
11 - | Synchronising hub for 3rd and 4th gear |
q | Pressing off → Fig. |
q | Installation position: → Fig. |
q | Pressing on → Fig. |
12 - | Synchro-ring for 3rd gear |
q | With molybdenum coating |
q | Checking for wear → Fig. |
13 - | 3rd speed selector gear |
q | Insert spring before installing → Fig. |
q | After pressing on → Item, check axial clearance with a feeler gauge (0.15 ... 0.35 mm) |
14 - | Needle bearing for 3rd gear |
q | Mark before removing |
q | Do not interchange with needle bearing for 4th gear |
q | Lubricate with gear oil before installing |
15 - | Input shaft |
16 - | Spring pin |
q | Drive in when renewing input shaft → Fig. |
17 - | Roller bearing |
q | For input shaft |
q | Pressing out and pressing in → Fig. |
18 - | Intermediate housing |
q | Servicing → Chapter |
19 - | Inner race for roller bearing |
q | Remove and fit by hand |
20 - | Circlip |
21 - | Thrust washer for needle bearing for 6th gear |
q | Installation position: shoulder towards circlip, smooth contact surface towards needle bearing → Anchor |
22 - | Needle bearing for 6th gear |
q | Lubricate with gear oil before installing |
23 - | 6th speed selector gear |
q | Insert spring before installing → Fig. |
q | After installing, check axial clearance with a feeler gauge (0.15 ... 0.35 mm) |
24 - | Synchro-ring for 6th gear |
q | Checking for wear → Fig. |
25 - | Synchronising hub for 5th and 6th gear |
q | Pulling off → Anchor |
q | Driving on → Anchor |
q | Installation position: projecting centre hub towards 5th speed selector gear |
26 - | Locking collar |
q | Is paired with synchronising hub |
q | Mark before removing → Anchor |
27 - | Synchro-ring for 5th gear |
q | Checking for wear → Fig. |
28 - | 5th speed selector gear |
q | Insert spring before installing → Fig. |
q | After installing, check axial clearance → Anchor |
29 - | Inner race for 5th speed selector gear |
q | Pulling off → Anchor |
q | Driving on → Anchor |
30 - | Needle bearing for 5th gear |
q | Lubricate with gear oil before installing |
31 - | 1st inner race for input shaft ball bearing |
q | Pulling off → Anchor |
q | Driving on → Anchor |
32 - | End cover |
q | Servicing → Chapter |
33 - | 2nd inner race for ball bearing for input shaft |
q | Pulling off → Anchor |
q | Driving on → Anchor |
34 - | Multi-point socket head bolt, 150 Nm |
q | Loosening and tightening → Anchor |
|
![]() |
![]()
|
![]() |
|
![]() |
Available circlips - Thickness in mm 1) | ||||
1.90 | 1.96 | 2.02 | ||
1.93 | 1.99 | 2.05 | ||
|
|
|
![]() |
|
![]() |
|
![]() |
|
![]() |