A4 Mk2
![]()
|
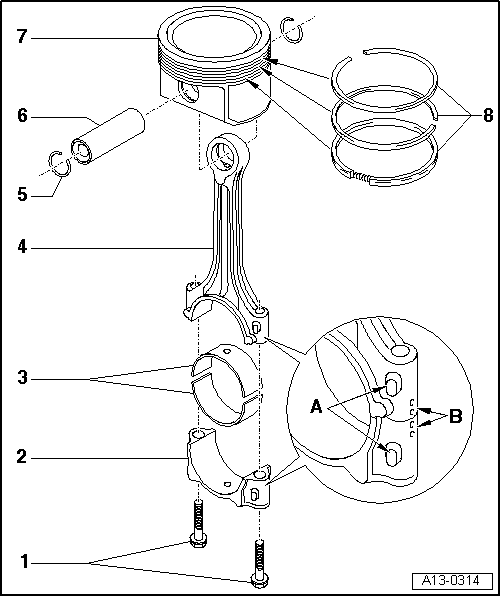
1 - | Conrod bolt, 30 Nm + 90° (1/4 turn) further |
q | Renew |
q | Lubricate threads and contact surface |
q | Use old bolts when measuring radial clearance |
q | To measure radial clearance, tighten to 30 Nm but do not turn further |
2 - | Conrod bearing cap |
q | Mark cylinder number -B- |
q | Installation position: Markings -A- face towards pulley end |
3 - | Bearing shells |
q | Upper bearing shell with oil hole for piston pin lubrication |
q | Installation position → Fig. |
q | Do not interchange used bearing shells (mark positions) |
q | Axial clearance (new): 0.10 ... 0.35 mm; wear limit: 0.40 mm |
q | Check radial clearance with Plastigage: New: 0.01 ... 0.05 mm; Wear limit: 0.12 mm. Do not rotate crankshaft when checking radial clearance |
4 - | Conrod |
q | Only renew as a complete set |
q | Mark cylinder number -B- |
q | Installation position: Markings -A- face towards pulley end |
q | With oil drilling for piston pin lubrication |
5 - | Circlip |
6 - | Piston pin |
q | If difficult to move, heat piston to approx. 60 °C |
q | Remove and install using drift -VW 222 A- |
7 - | Piston |
q | Checking → Fig. |
q | Mark installation position and cylinder number |
q | Arrow on piston crown points to pulley end |
q | Install using piston ring clamp |
q | Piston and cylinder dimensions → Chapter |
q | Checking cylinder bore → Fig. |
8 - | Piston rings |
q | Offset gaps by 120° |
q | Use piston ring pliers to remove and install |
q | “TOP” must face towards piston crown |
q | Checking ring gap → Fig. |
q | Checking ring-to-groove clearance → Fig. |
Piston ring (in mm) | New | Wear limit |
1st compression ring | 0.20 … 0.40 | 0.8 |
2nd compression ring | 0.20 … 0.40 | 0.8 |
Oil scraper ring | 0.25 … 0.50 | 0.8 |
|
![]() |
Piston ring (in mm) | New | Wear limit |
1st compression ring | 0.06 … 0.09 | 0.20 |
2nd compression ring | 0.05 … 0.08 | 0.20 |
Oil scraper ring | 0.03 … 0.06 | 0.15 |
|
![]() |
|
![]() |
|
![]() |
|
![]() |