A4 Mk2
![]()
|
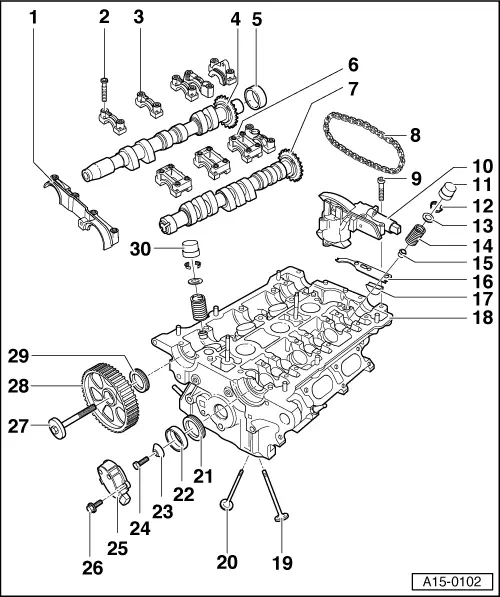
1 - | Double bearing cap |
q | Before installing, coat contact surfaces of front and rear bearing caps lightly with sealant → Fig.; Sealant → Parts catalogue |
2 - | 10 Nm |
3 - | Bearing cap on exhaust camshaft |
q | Watch position of dowel sleeve |
q | Note installation position and allocation → Anchor |
4 - | Exhaust camshaft |
q | Checking axial clearance → Chapter |
q | Removing and installing → Chapter |
q | Check radial clearance with Plastigage (bucket tappets removed) |
q | Radial clearance: wear limit: 0.1 mm |
q | Runout: max. 0.01 mm |
5 - | Cap |
q | Renewing → Chapter |
6 - | Bearing cap on inlet camshaft |
q | Watch position of dowel sleeve |
q | Note installation position and allocation → Anchor |
7 - | Inlet camshaft |
q | Checking axial clearance → Chapter |
q | Removing and installing → Chapter |
q | Check radial clearance with Plastigage (bucket tappets removed) |
q | Radial clearance: wear limit: 0.1 mm |
q | Runout: max. 0.01 mm |
8 - | Drive chain |
q | Installing → Anchor |
9 - | 10 Nm |
10 - | Mechanical camshaft adjuster |
q | With inlet camshaft control valve 1 -N205- |
q | Before removing, lock in position with chain tensioner retainer -3366- → Chapter |
11 - | Hydraulic bucket tappet (inlet valve) |
q | Checking → Chapter |
q | Removing and installing → Chapter |
q | Do not interchange (mark allocation) |
q | Place down with contact surface facing downwards |
q | Check axial clearance of camshaft before installing → Chapter |
q | Lubricate contact surface |
12 - | Valve cotters |
13 - | Valve spring plate |
14 - | Valve spring |
15 - | Valve stem oil seal |
q | Renewing → Chapter |
16 - | Rubber/metal gasket |
q | Renew |
17 - | Seal |
q | Renew |
18 - | Cylinder head |
q | See note → Chapter |
q | Checking valve guides, grinding-in valve seats → Chapter |
q | Machining valve seats → Chapter |
19 - | Exhaust valve |
q | Do not machine, only grinding-in is permitted |
q | Valve dimensions → Fig. |
q | Checking valve guides, grinding-in valve seats → Chapter |
20 - | Inlet valve |
q | Do not machine, only grinding-in is permitted |
q | Valve dimensions → Fig. |
q | Checking valve guides, grinding-in valve seats → Chapter |
21 - | Oil seal |
q | Note direction of rotation |
q | Renewing → Chapter and → Chapter |
22 - | Rotor for Hall sender |
q | Note fitting position (notch on camshaft) |
23 - | Washer |
q | Conical |
24 - | 25 Nm |
25 - | Hall sender |
26 - | 10 Nm |
27 - | 55 Nm |
28 - | Camshaft sprocket |
29 - | Oil seal |
q | Note direction of rotation |
q | Renewing → Chapter |
30 - | Hydraulic bucket tappet (exhaust valve) |
q | Checking → Chapter |
q | Removing and installing → Chapter |
q | Do not interchange (mark allocation) |
q | Place down with contact surface facing downwards |
q | Check axial clearance of camshaft before installing → Chapter |
q | Lubricate contact surface |
![]()
|
![]() |
Dimension | Inlet valve | Exhaust valve | |
Ø a | mm | 26.80 … 7.00 | 29.80 … 30.00 |
Ø b | mm | 5.96 … 5.97 | 5.94 … 5.95 |
c | mm | 104.84 … 105.34 | 103.64 … 104.14 |
α | ∠° | 45 | 45 |
|
|
![]() |