300Tdi Engine
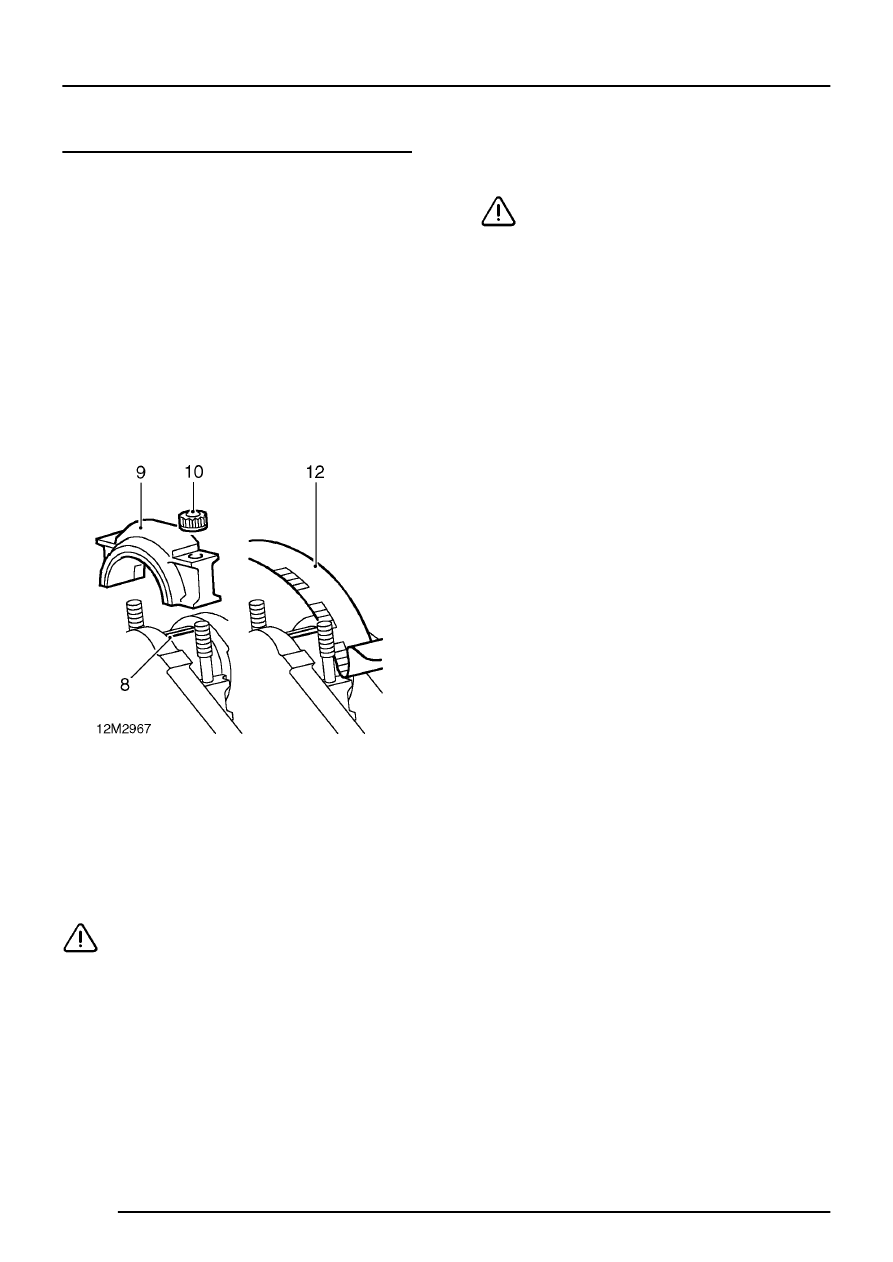
ENGINE
62
OVERHAUL
Big-end bearing clearance - checking
1. Fit pistons and connecting rods.
2. Degrease new big-end bearing shells.
3. Fit big-end bearing shells to connecting rods
ensuring that tag is located in recess in
connecting rod.
4. Fit big-end bearing shells to bearing caps
ensuring that tag is located in recess in cap.
5. Temporarily fit crankshaft pulley bolt and rotate
crankshaft to bring numbers 1 and 4 journals to
BDC.
6. Remove all traces of oil from crankshaft
journals.
7. Pull numbers 1 and 4 connecting rods on to
crankshaft journals, remove plastic tubing from
connecting rod bolts.
8. Place a strip of Plastigage across width of
numbers 1 and 4 big-end journals.
9. Fit bearing caps and shells to connecting rods
ensuring that reference marks on caps and
rods are aligned.
10. Fit big-end bearing cap nuts and tighten to 59
Nm.
CAUTION: Do not rotate crankshaft.
11. Remove big-end bearing caps and shells.
12. Measure widest portion of Plastigage on
crankshaft journals using the scale supplied;
the graduation that corresponds to the widest
portion of Plastigage indicates big-end bearing
clearance.
Big-end bearing clearance = 0.025 to 0.075
mm
13. If big-end bearing clearances are incorrect, use
a combination of standard and oversize
bearing shells and re-check clearance.
CAUTION: Retain selected shells with their
respective connecting rods and caps.
14. Remove all traces of Plastigage using an oily
rag.
15. Repeat above procedures for numbers 2 and 3
big-end bearings.