Discovery II
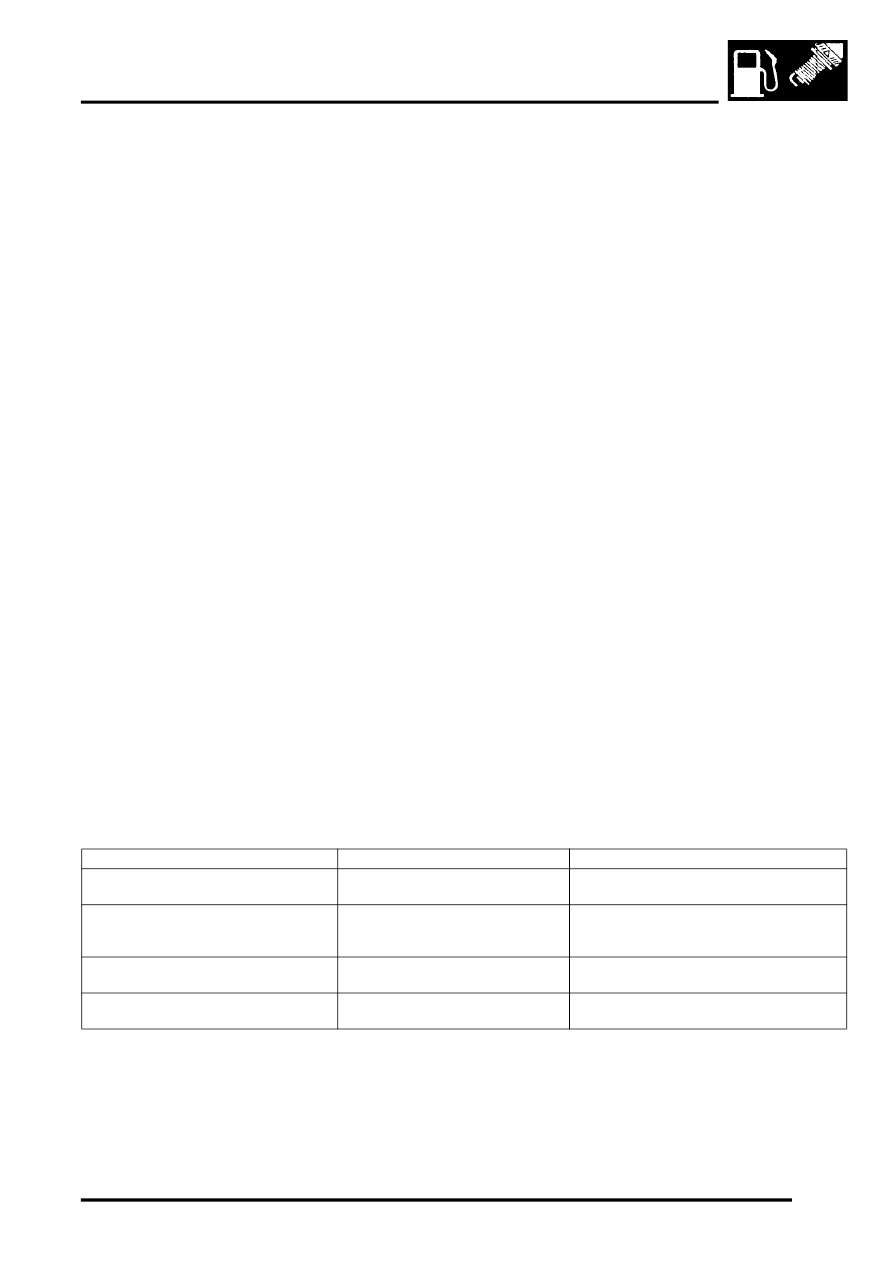
EMISSION CONTROL - V8
DESCRIPTION AND OPERATION 17-2-37
Lambda Heater Diagnostic
The system determines the heater current and supply voltage so that the heater's resistance can be calculated. After
the engine has been started, the system waits for the heated oxygen sensors to warm up, then calculates the
resistance from the voltage and current measurements. If the value is found to be outside of the upper or lower
threshold values, then the fault is processed (the MIL light is illuminated on NAS vehicles).
Lambda Period Diagnostic
The pre-catalytic converter sensors are monitored. As the sensors age, the rich to lean and the lean to rich switching
delays increase, leading to increased emissions if the lambda control becomes inaccurate. If the switching period
exceeds a defined limit, the sensor fault is stored in the ECM diagnostic memory (the MIL light is illuminated on NAS
vehicles).
Post-Catalytic Converter Lambda Adaptation Diagnostic (NAS only)
On NAS vehicles the ageing effects of the pre-catalytic converter sensors are compensated for by an adaptive value
derived from the post-catalytic converter sensors. This is a long term adaption which only changes slowly. For a rich
compensation the additive value is added to the rich delay time. For a lean compensation, the adaptive value is added
to the lean delay time. The adaptive time is monitored against a defined limit, and if the limit is exceeded, the fault is
stored in the ECM's diagnostic memory and the MIL light is illuminated on the instrument pack.
Catalyst Monitoring Diagnostic
On NAS specification vehicles the catalysts are monitored both individually and simultaneously for emission pollutant
conversion efficiency. The conversion efficiency of a catalyst is monitored by measuring the oxygen storage, since
there is a direct relationship between these two factors. The closed loop lambda control fuelling oscillations produce
pulses of oxygen upstream of the catalyst, as the catalyst efficiency deteriorates its ability to store oxygen is
decreased. The amplitudes of the signals from the pre-catalytic and post-catalytic converter heated oxygen sensors
are compared. As the oxygen storage decreases, the post-catalytic converter sensor begins to follow the oscillations
of the pre-catalytic converter heated oxygen sensors. Under steady state conditions the amplitude ratio is monitored
in different speed / load sites. There are three monitoring areas, and if the amplitude ratio exceeds a threshold in all
three areas the catalyst conversion limit is exceeded; the catalyst fault is stored in the diagnostic memory and the MIL
light is illuminated on the instrument pack. There is a reduced threshold value for both catalysts monitored as a pair.
In either case, a defective catalyst requires replacement of the downpipe assembly.
In the case of a catalytic converter failure the following failure symptoms may be apparent:
l
MIL light on after 2 driving cycles (NAS market only).
l
High exhaust back pressure if catalyst partly melted.
l
Excessive emissions
l
Strong smell of H
2
S (rotten eggs).
Oxygen sensor voltages can be monitored using TestBook/T4, the approximate output voltage from the heated
oxygen sensors with a warm engine at idle and with closed loop fuelling active are shown in the table below:
Measurement
Normal catalyst
Defective catalyst
Pre-catalytic heated oxygen sensors
~ 100 to 900 mV switching @ ~ 0.5
Hz
~ 100 to 900 mV switching @ ~ 0.5 Hz
Post-catalytic heated oxygen sensors
~ 200 to 650 mV, static or slowly
changing
~ 200 to 850 mV, changing up to same
frequency as pre-catalytic heated oxygen
sensors
Amplitude ratio (LH HO
2
sensors & RH
HO
2
sensors)
<0.3 seconds
>0.6 seconds (needs to be approximately
0.75 seconds for single catalyst fault)
Number of speed/load monitoring areas
exceeded (LH & RH)
0
>1 (needs to be 3 for fault storage)