Discovery II
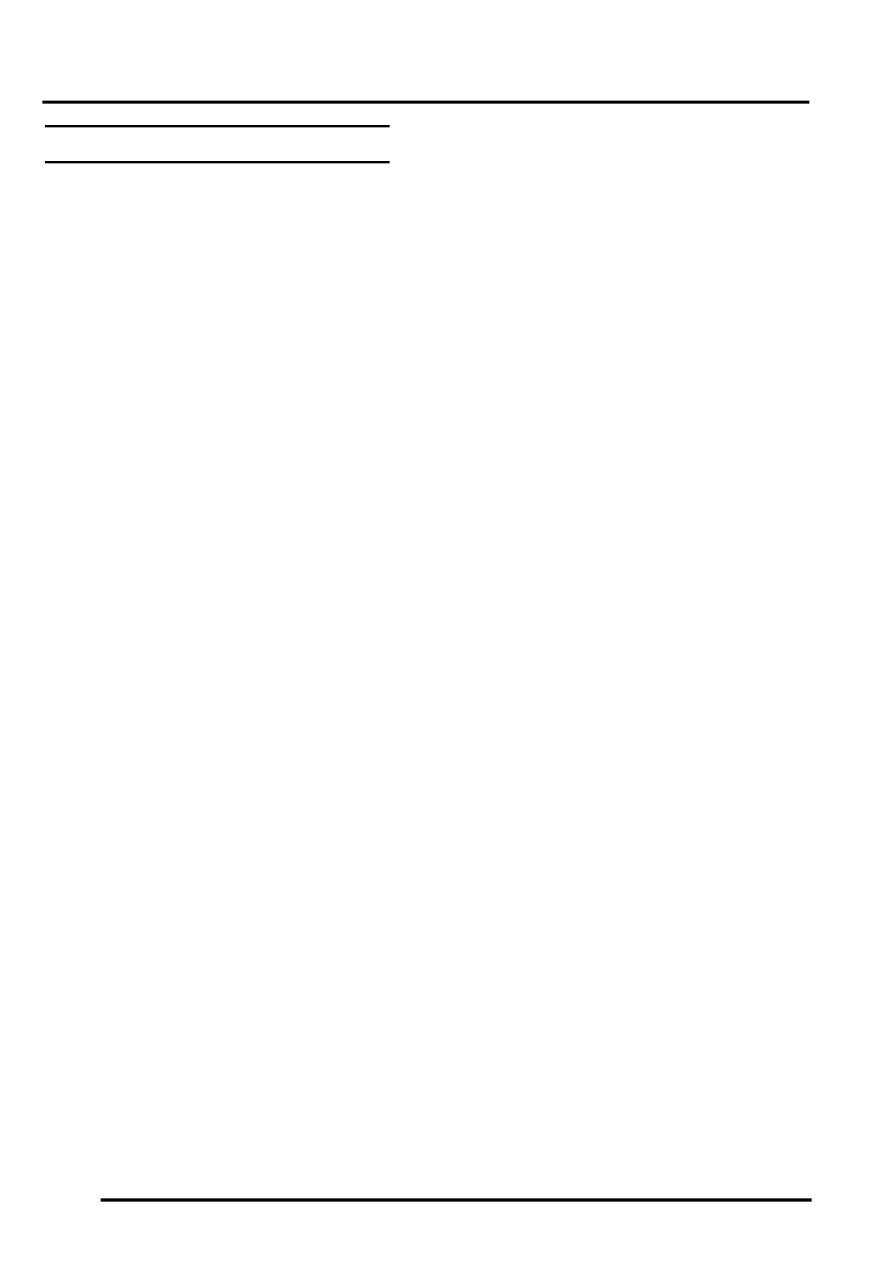
GENERAL INFORMATION
03-6
General Fitting Instructions
Component removal
Whenever possible, clean components and
surrounding area before removal.
l
Blank off openings exposed by component
removal.
l
Immediately seal fuel, oil or hydraulic lines when
apertures are exposed; use plastic caps or
plugs to prevent loss of fluid and ingress of dirt.
l
Close the open ends of oilways exposed by
component removal with tapered hardwood
plugs or conspicuous plastic plugs.
l
Immediately a component is removed, place it in
a suitable container; use a separate container
for each component and its associated parts.
l
Clean bench and provide marking materials,
labels and containers before dismantling a
component.
Dismantling
Observe scrupulous cleanliness when dismantling
components, particularly when brake, fuel or
hydraulic system parts are being worked on. A
particle of dirt or a cloth fragment could cause a
serious malfunction if trapped in these systems.
l
Blow out all tapped holes, crevices, oilways and
fluid passages with an air line. Ensure that any
'O' rings used for sealing are correctly replaced
or renewed, if disturbed during the process.
l
Use marking ink to identify mating parts and
ensure correct reassembly. Do not use a centre
punch or scriber to mark parts, they could
initiate cracks or distortion in marked
components.
l
Wire together mating parts where necessary to
prevent accidental interchange (e.g. roller
bearing components).
l
Wire labels on to all parts which are to be
renewed, and to parts requiring further
inspection before being passed for reassembly;
place these parts in separate containers from
those containing parts for rebuild.
l
Do not discard a part due for renewal until after
comparing it with a new part, to ensure that its
correct replacement has been obtained.
Cleaning components
Always use the recommended cleaning agent or
equivalent. Ensure that adequate ventilation is
provided when volatile degreasing agents are being
used. Do not use degreasing equipment for
components containing items which could be
damaged by the use of this process.
General inspection
All components should be inspected for wear or
damage before being reassembled.
l
Never inspect a component for wear or
dimensional check unless it is absolutely clean;
a slight smear of grease can conceal an
incipient failure.
l
When a component is to be checked
dimensionally against recommended values,
use the appropriate measuring equipment
(surface plates, micrometers, dial gauges etc.).
Ensure the measuring equipment is calibrated
and in good serviceable condition.
l
Reject a component if its dimensions are
outside the specified tolerances, or if it appears
to be damaged.
l
A part may be refitted if its critical dimension is
exactly to its tolerance limit and it appears to be
in satisfactory condition. Use 'Plastigauge' 12
Type PG-1 for checking bearing surface
clearances.