Freelander System Description and Operation
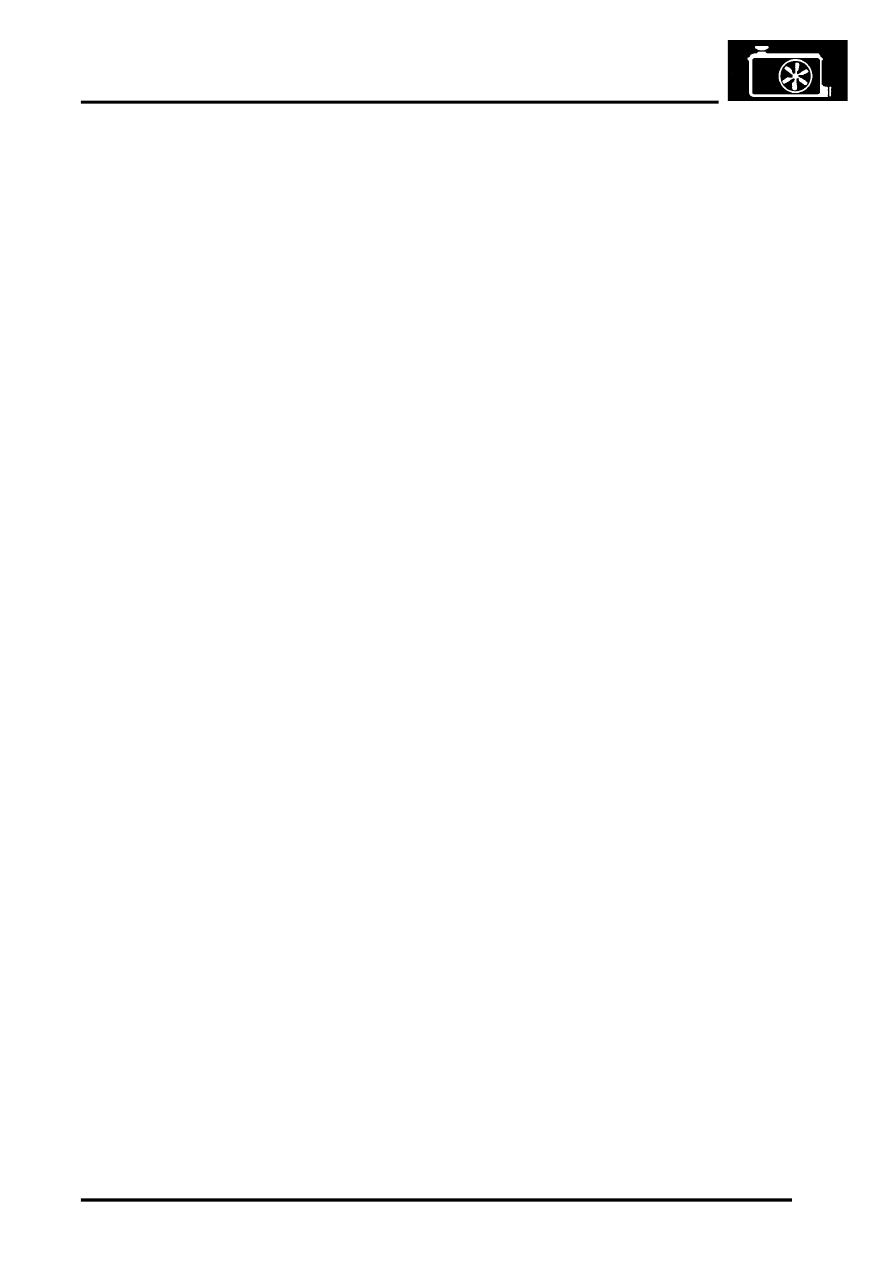
COOLING SYSTEM - K SERIES KV6
DESCRIPTION AND OPERATION
26-3-9
Heater Diverter Valve – From 2003 Model Year
At low engine speeds the heater diverter valve is closed, allowing only a bleed flow of coolant through the engine oil
and transmission fluid coolers. This increases the coolant flow through the heater matrix improving heater
performance.
As the engine speed increases, the increased output from the coolant pump opens the heater diverter valve allowing
the full flow of coolant through the engine oil and transmission fluid coolers and the heater matrix.
Cooling Fan Control
The ECM controls the operation of the variable speed cooling fans via a Pulse Width Modulated (PWM) signal to the
cooling fan ECU. The cooling fan ECU regulates the voltage of a common power feed to the two fans, and relates the
voltage to the duty cycle of the PWM signal.
The ECM varies the duty cycle of the PWM signal between 3 and 90% to vary the cooling fan speed. At duty cycles
between 3 and 9% the cooling fans are off. When the duty cycle goes above 9% the cooling fans come on at minimum
speed, then increase in speed, in proportion to the increase in the duty cycle, up to maximum speed at a duty cycle
of 90%. If the duty cycle is less than 3% or more than 90%, the cooling fan ECU interprets the signal as an open or
short circuit and runs the cooling fans at maximum speed to ensure the engine and gearbox do not overheat.
The speed of the cooling fans varies between a minimum of 750 rev/min, at 6 volts and a maximum of 4000 rev/min
at nominal battery voltage. To reduce the noise from the cooling fans they are driven at slightly different speeds,
except when running at minimum and maximum speeds. Stepped speed changes occur at 1500 rev/min (RH cooling
fan), 1450 and 2600 rev/min (LH cooling fan) to improve refinement.
Control Inputs
While the engine is running, the ECM adjusts the speed of the cooling fans in response to inputs from:
l
The thermostat monitoring sensor, for engine cooling. The fans come on at minimum speed if the coolant
temperature goes above 90
°
C (194
°
F), and progressively increase to maximum speed at a coolant temperature
of 102
°
C (216
°
F).
l
The A/C system, via the instrument pack and the CAN bus, for refrigerant system cooling.
l
The EAT ECU, via the CAN bus, for gearbox cooling.
If there is a conflict between requested cooling fan speeds from the different inputs, the ECM adopts the highest
requested speed.
As part of the power down routine, when the ignition is switched off, if the ambient air temperature is more than 15
°
C
(59
°
F) the ECM samples the coolant temperature using the input from the Engine Coolant Temperature (ECT) sensor.
If the coolant temperature is more than 106
°
C (223
°
F), the ECM signals for the cooling fans to come on. The speed
of the cooling fans is in proportion to the coolant temperature, from minimum speed at >106
°
C (>223
°
F) to maximum
speed at 115
°
C (239
°
F). The cooling fans are switched off after 5 minutes or when the coolant temperature decreases
to 106
°
C (223
°
F), whichever occurs first.
Motor Protection
The cooling fan ECU monitors the speed of the cooling fans, from the current draw of the motors, and incorporates
strategies to protect the motors from electrical overload if the fans are seized or heavily loaded (e.g. by debris or
during wading).
When the duty cycle of the PWM signal indicates the cooling fans should be switched on, the cooling fan ECU initially
outputs 2.5 volts to the motors to produce a 'soft' start. When the cooling fan ECU detects the motors are running
satisfactorily, it then increases the outputs to the appropriate voltages for the required cooling fan speeds. If a motor
fails to start within 3 seconds, the cooling fan ECU switches off the output to the affected motor, waits for 5 seconds
and then tries another soft start. If the second soft start fails, after a further wait of 5 seconds the cooling fan ECU
outputs 6 volts to the motor in an attempt to get it started. If the motor starts, the cooling fan ECU then increases the
output to the appropriate voltage for the required cooling fan speed. If the motor fails to start within 4 seconds, the
cooling fan ECU switches the output off, then, provided the cooling fans are still requested on, periodically invokes
the start routine in an attempt to get the motor running.
If a cooling fan is already running and then seizes or becomes heavily loaded, the cooling fan ECU switches off the
output to the affected motor, then periodically invokes the start routine, while the cooling fans are still requested on,
in an attempt to get the motor running again.
When one of the cooling fans is not running, the cooling fan ECU runs the other cooling fan at maximum speed.