Freelander System Description and Operation
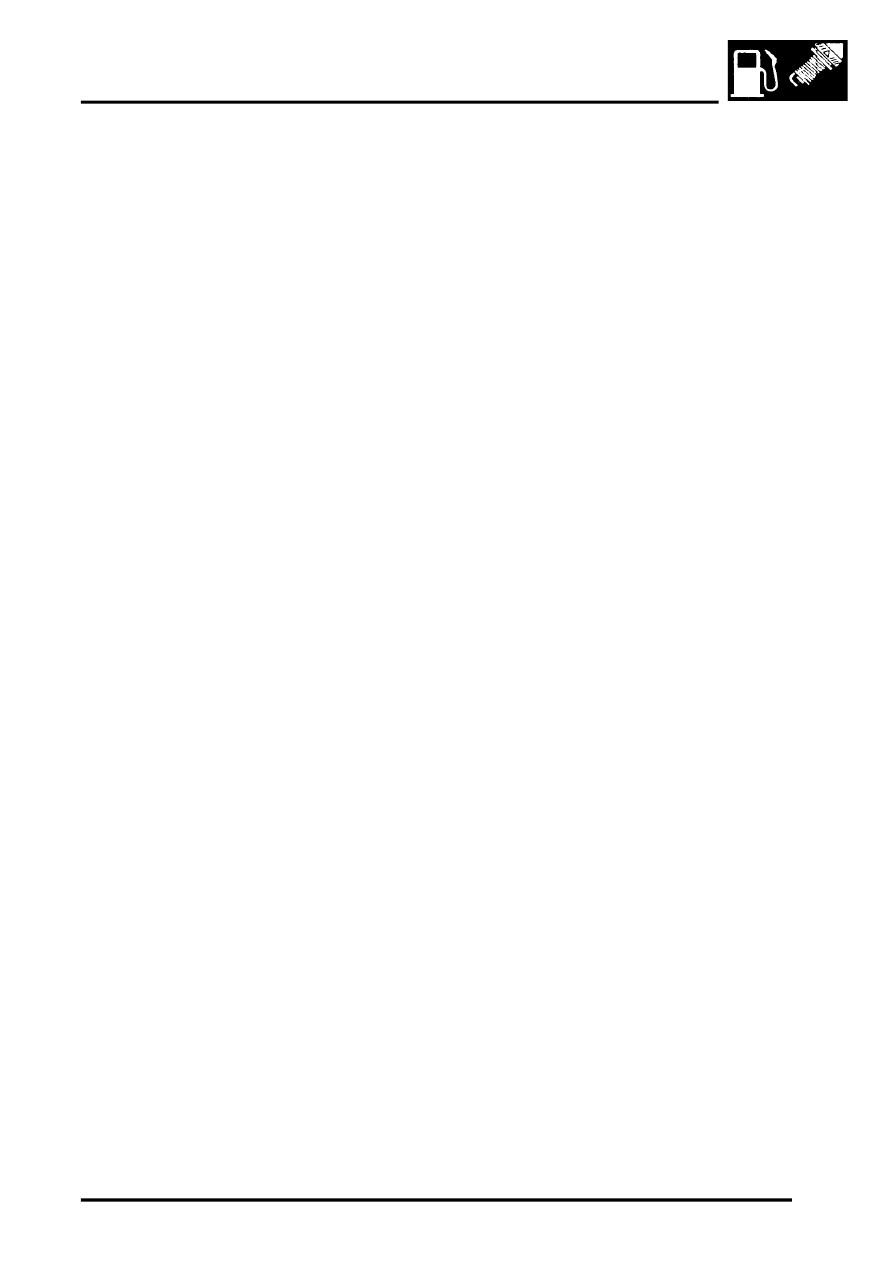
ENGINE MANAGEMENT SYSTEM - SIEMENS
DESCRIPTION AND OPERATION 18-4-29
Ignition Timing
The ECM calculates ignition timing using inputs from the following sensors:
l
CKP sensor.
l
MAF sensor.
l
Knock sensors.
l
TP sensor (idle only).
l
ECT sensor.
At start up and idle the ECM sets ignition timing by referencing the ECT and CKP sensors. Once above idle the ignition
timing is controlled according to maps stored in the ECM memory and modified according to additional sensor inputs
and any adaptive value stored in memory. The maps keep the ignition timing within a narrow band that gives an
acceptable compromise between power output and emission control. The ignition timing advance and retard is
controlled by the ECM in order to avoid combustion knock.
Knock Control
The ECM uses active knock control to prevent combustion knock damaging the engine. If the knock sensor inputs
indicate the onset of combustion knock, the ECM retards the ignition timing for that particular cylinder by 3
°
. If the
combustion knock indication continues, the ECM further retards the ignition timing, in decrements of 3
°
, for a
maximum of 15
°
from where the onset of combustion knock was first sensed. When the combustion knock indication
stops, the ECM restores the original ignition timing in increments of 0.75
°
.
To reduce the risk of combustion knock at high intake air temperatures, the ECM retards the ignition timing if the intake
air temperature exceeds 55
°
C (169
°
F). The amount of ignition retard increases with increasing air intake
temperature.
Idle Speed Control
The ECM controls the engine idle speed using a combination of fuelling, ignition timing and the electric throttle.
When the engine idle speed fluctuates the ECM initially varies the ignition timing, which produces rapid changes of
engine speed. If this fails to correct the idle speed, the ECM also adjusts the electric throttle and fuelling.
Misfire Detection
The ECM uses the CKP sensor input to monitor the engine for misfires. As the combustion charge in each cylinder is
ignited the crankshaft accelerates, then subsequently decelerates. By monitoring the acceleration/ deceleration
pulses of the crankshaft the ECM can detect misfires.
Low fuel level:
When the fuel tank is almost empty there is a risk that air may be drawn into the fuel system, due to fuel 'slosh', causing
fuel starvation and misfires. To prevent false misfire faults being logged, the ECM disables misfire detection if it
receives a low fuel level message on the CAN bus. Fuel tank content is monitored by the instrument pack, which
transmits the low fuel level message if the fuel tank content decreases to less than 15% (8.85 litres; 2.34 US galls).
Rough road disable:
When the vehicle is travelling over a rough road surface the engine crankshaft is subjected to torsional vibrations
caused by mechanical feedback from the road surface through the transmission. To prevent misinterpretation of these
torsional vibrations as a misfire, the misfire monitor is disabled when a road surface exceeds a roughness limit
programmed into the ECM. The roughness of the road is calculated by the ABS modulator, from the four ABS sensor
inputs, and transmitted to the ECM on the CAN bus.