Freelander System Description and Operation
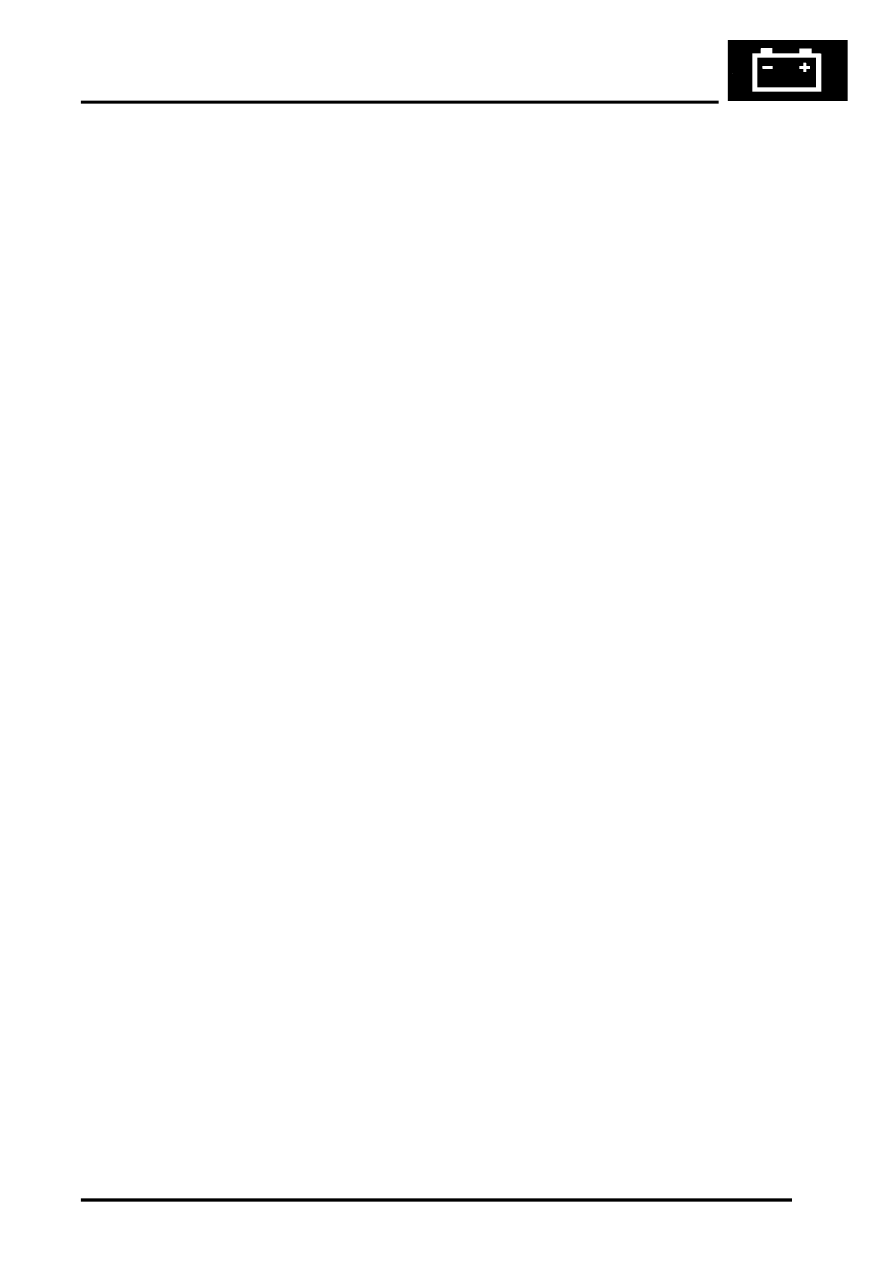
INSTRUMENTS
DESCRIPTION AND OPERATION
88-7
Powered/Unpowered Modes
Powered mode is the standard operational condition for the instrument pack. In this condition the pack receives a
permanent 12V battery supply, no ignition supply or CAN messages. The microprocessor is also off but the real time
clock will remain powered.
Unpowered mode is entered when the vehicle battery is disconnected. When the power supply is restored, the pack
will resume powered mode.
Diagnostic Mode
To enter diagnostic mode, the instrument pack must first be in normal or standby normal mode and TestBook or
another diagnostic tool must be connected to the diagnostic socket. The instrument pack will enter diagnostic mode
when it receives a valid message on the ISO 9141 K Line. Confirmation of access to this mode is given by a 'dIAg'
message in the LCD.
Diagnostic mode is exited by receipt of a message from the diagnostic tool to terminate diagnostics. Removal of the
ignition switch position II battery supply or disconnection of the diagnostic communication to the socket will also
terminate the diagnostic mode.
Crank Mode
When the starter motor is cranking the engine, the current drain may cause the values of inputs and CAN messages
to become corrupted or invalid. The instrument pack senses that cranking is operative when ignition switch positions
II and III are active and the ignition feed from switch position II falls to approximately 3V.
During cranking, all inputs to gauges are suspended and the gauges will remain in their pre-crank state. The odometer
display is not affected.
Standby Normal Mode
Standby normal mode is used if an incorrect CAN standard message is received and also allows access to
diagnostics. In this mode all CAN transmissions are terminated and the pack will not respond to any CAN messages
received. All conventionally wired warning lamps will function normally and the pack can enter diagnostic mode if
required. A fault flag is recorded in the EEPROM for the CAN standard message fault.
Low Battery Operation
If the permanent battery supply voltage falls to below 8V, CAN message transmissions will be suspended and
received CAN messages will be ignored, analogue gauges will read zero and warning lamp operation is suspended.
When the voltage rises above 8V, normal instrument pack operation is resumed.
Speedometer
The speedometer is electronically operated and contains an LCD. Each model has a maximum scale indication of 136
mph (220 km/h).
The speedometer is driven by CAN messages from the ABS ECU. The messages are generated by an ABS wheel
speed sensor which produces pulses as the reluctor rotates. The instrument pack microprocessor processes the
incoming CAN message from the ABS ECU and converts it into electrical signals for speedometer operation.
If the CAN message fails for more than 64ms the microprocessor will terminate speedometer operation and record a
fault flag. The recorded fault can be accessed using TestBook.