Leon Mk1
|

Special tools and workshop equipment required |
t | Support bridge -T10323- |
t | Adjusting gauge -T10425- |
t | Extractor -T10427- |
t | Ruler -T40100- |
This »section« explains how to calculate thickness of shims in gearbox housing. 4 shims are installed in total. One shim on each secondary shaft. Differential does not have a shim here either. |
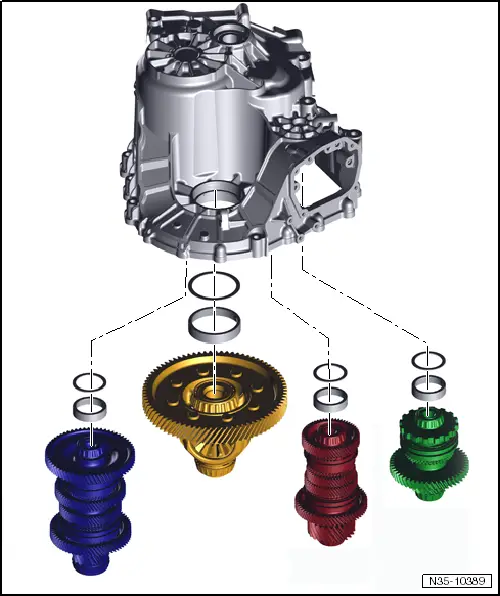
Procedure: |
First calculate how »high« shafts stand in clutch housing. |
Then measure how »deep« gearbox housing is. |
Subtract both »heights« from one another. |
Bearing preload is stated for each shaft in working procedure. Therefore, follow this procedure exactly, please. |
Each shaft has a different preload, therefore follow the instruction precisely and note the different preloads. |
The correct shim can then be calculated in each case. |
For information about installation of shims and bearing races after »calculation«, refer to → Chapter. |
l | Do not insert differential yet. Output shafts 1, 2 and 3 are in their bearings. |
|
|
![]() |
![]()
|
![]() |
|
![]() |
|
![]() |
|
![]() |
|
![]() |
|
![]() |
|
![]() |
|
![]() |
|
![]() |
|
![]() |
|
![]() |
|
![]() |
|
![]() |
|
![]() |
![]()
|
![]() |
|
![]() |
|
![]() |
|
![]() |
|
![]() |
|
![]() |
|
![]() |
![]()
|
![]() |
|
![]() |
Calculated shim thickness in gearbox housing for output shaft 1 | Shim to be installed (in millimetres) | |
from | to | |
0,625 | 0,674 | 0,65 |
0,675 | 0,724 | 0,70 |
0,725 | 0,774 | 0,75 |
0775 | 0,824 | 0,80 |
0,825 | 0,874 | 0,85 |
0,875 | 0,924 | 0,90 |
0,925 | 0,974 | 0,95 |
0,975 | 1,024 | 1,00 |
1,025 | 1,074 | 1,05 |
1,075 | 1,124 | 1,10 |
1,125 | 1,174 | 1,15 |
1,175 | 1,224 | 1,20 |
1,225 | 1,274 | 1,25 |
1,275 | 1,324 | 1,30 |
1,325 | 1,374 | 1,35 |
1,375 | 1,424 | 1,40 |
1,425 | 1,474 | 1,45 |
1,475 | 1,524 | 1,50 |
1,525 | 1,574 | 1,55 |
1,575 | 1,624 | 1,60 |
1,625 | 1,674 | 1,65 |
1,675 | 1,724 | 1,70 |
1,725 | 1,774 | 1,75 |
1,775 | 1,824 | 1,80 |
1,825 | 1,874 | 1,85 |
|
![]() |
|
![]() |
![]()
|
![]() |
|
![]() |
Calculated shim thickness in gearbox housing for output shaft 2 | Shim to be installed (in millimetres) | |
from | to | |
0,625 | 0,674 | 0,65 |
0,675 | 0,724 | 0,70 |
0,725 | 0,774 | 0,75 |
0775 | 0,824 | 0,80 |
0,825 | 0,874 | 0,85 |
0,875 | 0,924 | 0,90 |
0,925 | 0,974 | 0,95 |
0,975 | 1,024 | 1,00 |
1,025 | 1,074 | 1,05 |
1,075 | 1,124 | 1,10 |
1,125 | 1,174 | 1,15 |
1,175 | 1,224 | 1,20 |
1,225 | 1,274 | 1,25 |
1,275 | 1,324 | 1,30 |
1,325 | 1,374 | 1,35 |
1,375 | 1,424 | 1,40 |
1,425 | 1,474 | 1,45 |
1,475 | 1,524 | 1,50 |
1,525 | 1,574 | 1,55 |
1,575 | 1,624 | 1,60 |
1,625 | 1,674 | 1,65 |
1,675 | 1,724 | 1,70 |
1,725 | 1,774 | 1,75 |
1,775 | 1,824 | 1,80 |
1,825 | 1,874 | 1,85 |
|
![]() |
|
![]() |
![]()
|
![]() |
|
![]() |
Calculated shim thickness in gearbox housing for output shaft 3 | Shim to be installed (in millimetres) | |
from | to | |
0,625 | 0,674 | 0,65 |
0,675 | 0,724 | 0,70 |
0,725 | 0,774 | 0,75 |
0775 | 0,824 | 0,80 |
0,825 | 0,874 | 0,85 |
0,875 | 0,924 | 0,90 |
0,925 | 0,974 | 0,95 |
0,975 | 1,024 | 1,00 |
1,025 | 1,074 | 1,05 |
1,075 | 1,124 | 1,10 |
1,125 | 1,174 | 1,15 |
1,175 | 1,224 | 1,20 |
1,225 | 1,274 | 1,25 |
1,275 | 1,324 | 1,30 |
1,325 | 1,374 | 1,35 |
1,375 | 1,424 | 1,40 |
1,425 | 1,474 | 1,45 |
1,475 | 1,524 | 1,50 |
1,525 | 1,574 | 1,55 |
1,575 | 1,624 | 1,60 |
1,625 | 1,674 | 1,65 |
1,675 | 1,724 | 1,70 |
|
![]() |
|
![]() |
|
![]() |
|
![]() |
|
![]() |
|
![]() |
|
![]() |
|
![]() |
Calculated shim thickness of differential | Shim to be installed (in millimetres) | |
from | to | |
0,625 | 0,674 | 0,65 |
0,675 | 0,724 | 0,70 |
0,725 | 0,774 | 0,75 |
0775 | 0,824 | 0,80 |
0,825 | 0,874 | 0,85 |
0,875 | 0,924 | 0,90 |
0,925 | 0,974 | 0,95 |
0,975 | 1,024 | 1,00 |
1,025 | 1,074 | 1,05 |
1,075 | 1,124 | 1,10 |
1,125 | 1,174 | 1,15 |
1,175 | 1,224 | 1,20 |
1,225 | 1,274 | 1,25 |
1,275 | 1,324 | 1,30 |
1,325 | 1,374 | 1,35 |
1,375 | 1,424 | 1,40 |
|
![]() |