Leon Mk1
Repairing valve gear |

t | Cylinder heads which have cracks between the valve seats or between a valve seat insert and the spark plug thread can be used further without reducing service life, provided the cracks do not exceed a maximum of 0.3 mm in width, or when no more than the first 4 turns of the spark plug thread are cracked. |
t | When new bucket tappets have been installed the engine must not be started for about 30 minutes. (Otherwise valves will contact pistons.) Then turn crankshaft two full revolutions. |
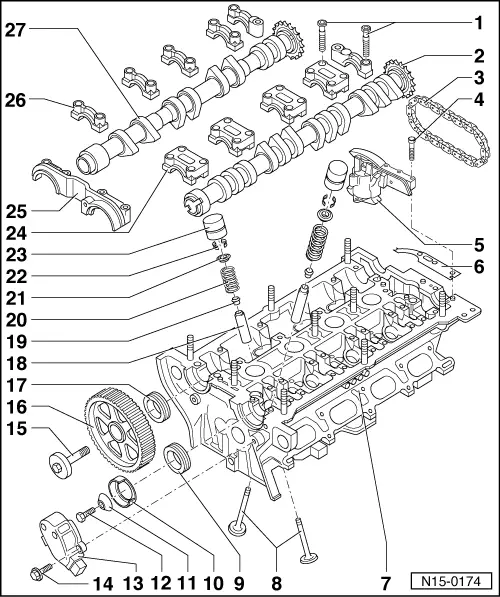
1 - | 10 Nm |
2 - | Inlet camshaft |
q | Checking axial clearance → Fig.. |
q | Removing and installing → Chapter. |
q | Check radial clearance with plastigage, wear limit: 0.1 mm. |
q | Runout: max. 0.01 mm. |
3 - | Drive chain |
q | Before removing, mark direction of rotation (installation position) → Chapter, Removing and installing camshafts. |
4 - | 10 Nm |
5 - | Chain tensioner |
q | Must seat on dowel sleeves. |
q | Only rotate engine when chain tensioner is installed. |
q | Secure with chain tensioner retainer -3366- before removing → Chapter, Removing and installing camshafts. |
q | Seal transitions between chain tensioner/cylinder head → Fig. |
6 - | Rubber/metal gasket |
q | Replacement → Chapter, Removing and installing camshafts. |
7 - | Cylinder head |
q | Removing and installing → Chapter. |
q | Reworking valve seats → Chapter. |
q | Reworking sealing surface → Fig.. |
q | Sealing transition points → Fig. and → Fig.. |
8 - | Valves |
q | Do not rework, only lapping-in is permitted. |
q | Valve dimensions → Fig.. |
q | Exhaust valves with sodium filling: Observe disposal instructions → Fig.. |
9 - | Seal |
q | Renewing → Chapter. |
10 - | Trim |
q | For Hall sender. |
q | When installing note fixing arrangement. |
11 - | Washer |
q | Conical. |
12 - | 25 Nm |
13 - | Hall sender -G40- housing |
q | Check Hall sender -G40- → Rep. Gr.28. |
14 - | 10 Nm |
15 - | 65 Nm |
q | Use counterhold tool -3036- to loosen and tighten |
16 - | Camshaft pulley |
q | Note installation position: the narrow web of camshaft pulley faces outwards and the TDC No. 1 cylinder marking is visible. |
q | Note position when installing toothed belt → Chapter, removing, installing and tensioning toothed belt. |
17 - | Seal |
q | Renewing → Chapter. |
18 - | Valve guide |
q | Checking → Chapter. |
19 - | Valve stem oil seal |
q | Renewing → Chapter. |
20 - | Valve spring |
q | Removing and installing: |
Cylinder head removed: With valve spring tool -3362- and press piece -3362/1-. |
Cylinder head installed: → Chapter, Renewing valve stem oil seals |
21 - | Valve spring plate |
22 - | Cotters |
23 - | Bucket tappet |
q | Do not interchange. |
q | With hydraulic valve clearance compensation. |
q | Checking → Chapter. |
q | Store with cam contact surface downwards |
q | Before installing, check camshaft axial clearance → Fig.. |
q | Oil contact surface. |
24 - | Inlet camshaft bearing cap |
q | Observe installation position and installation sequence → Chapter, Removing and installing camshaft. |
25 - | Double bearing cap |
q | Must seat on dowel sleeves. |
q | Lightly coat contact surface with sealing compound -AMV 174 004 01-, observe installation position and installation sequence → Chapter, Removing and installing camshaft. |
q | Seal transition points between double bearing cap and cylinder head → Fig.. |
26 - | Exhaust camshaft bearing cap |
q | Observe installation position and installation sequence → Chapter, Removing and installing camshaft. |
27 - | Exhaust camshaft |
q | Checking axial clearance → Fig.. |
q | Removing and installing → Chapter. |
q | Check radial clearance with plastigage, wear limit: 0.1 mm. |
q | Runout: max. 0.01 mm. |
|
![]() |
![]()
|
![]() |
Dimension | Inlet valve | Exhaust valve | |
Ø a | mm | 26.9 | 29.9 |
Ø b | mm | 5.963 | 5.943 |
c | mm | 104.84...105.34 | 103.64...104.14 |
α | ∠° | 45 | 45 |
![]()
|
|
![]() |
|
![]() |