Leon Mk1
I - Assembly overview - subframe, anti-roll bar, lower wishbone up to model year 2000 |
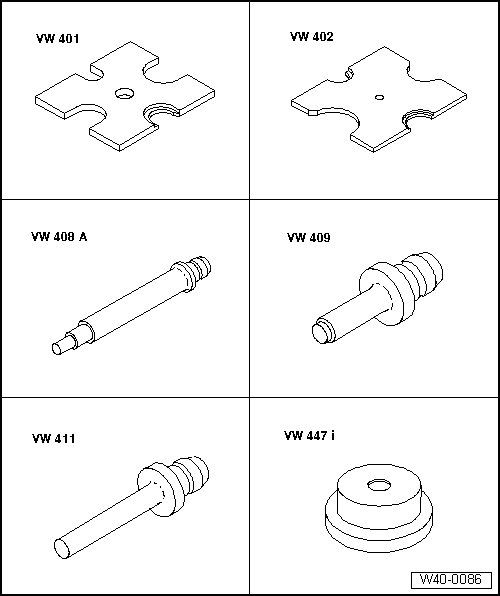
Special tools and workshop equipment required |
t | Press plate -VW 401- |
t | Press plate -VW 402- |
t | Press tool -VW 408 A- |
t | Press tool -VW 409- |
t | Press tool -VW 411- |
t | Thrust plate -VW 447 i- |
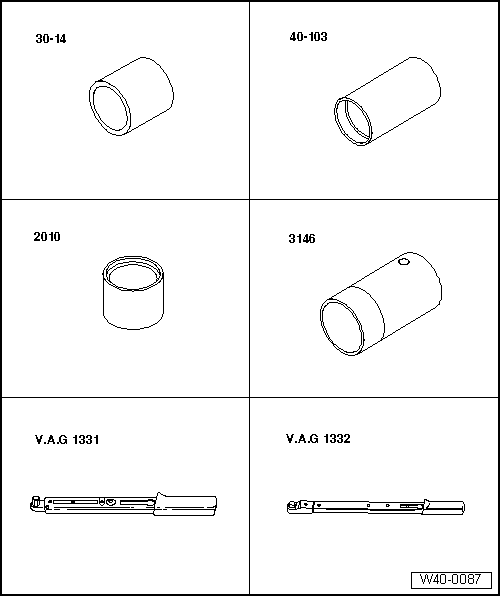
t | Tube -30-14- |
t | Support -40-103- |
t | Tube -2010- |
t | Tube -3146- |
t | Torque wrench -V.A.G 1331- |
t | Torque wrench -V.A.G 1332- |

t | If a vehicle has to be moved after removing the drive shaft, first install outer joint and tighten to 50 Nm otherwise the wheel bearing will be damaged. |
t | It is not permitted to carry out welding and straightening operations on load bearing suspension components or those components which locate the wheels. |
t | Always renew self-locking nuts. |
t | Always renew corroded nuts and bolts. |
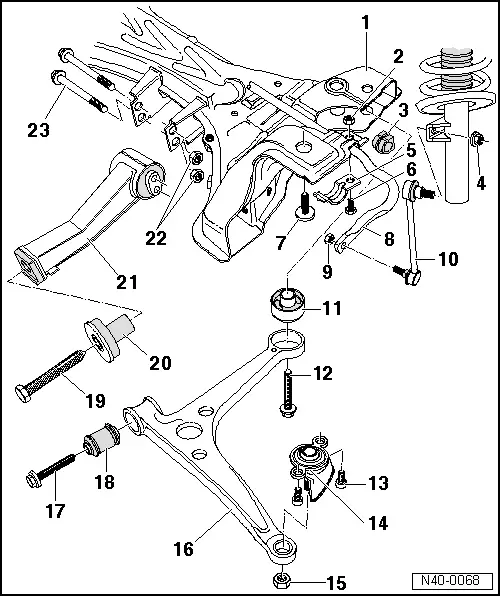
1 - | Subframe |
After installing check position of steering wheel during a test drive. |
If steering wheel is not in straight ahead position the front axle toe must be checked and if necessary adjusted! |
2 - | Hexagon nut |
q | 55 Nm |
3 - | Rubber bush |
4 - | Nut |
q | 100 Nm |
q | Self-locking |
q | Renew each time after removing. |
5 - | Clamp |
6 - | Hexagon bolt |
7 - | Hexagon bolt |
q | M14 x 1.5 x 65 |
q | 150 Nm and turn 90° further. |
q | Renew each time after removing. |
8 - | Anti-roll bar |
q | Removing and installing → Chapter. |
9 - | Nut |
q | 100 Nm |
q | Allocation → Electronic Parts Catalogue “ETKA”. |
10 - | Coupling rod |
11 - | Rear wishbone mounting |
q | Pressing out → Fig.. |
q | Installation position → Fig.. |
q | Pressing in → Fig.. |
12 - | Hexagon bolt |
q | M14 x 1.5 x 95 |
q | 150 Nm and turn 90° further. |
q | Check rear bonded rubber bush is correctly positioned in the subframe before tightening → Fig.. |
q | Renew each time after removing. |
13 - | Allen head bolt, 55 Nm |
14 - | Swivel joint |
q | Removing and installing → Chapter. |
15 - | Nut |
q | 30 Nm and turn 90° further. |
q | Self-locking |
q | Renew each time after removing. |
q | Brace with 7 mm Allen key while fitting the nut. |
16 - | Suspension link |
q | Installation position in subframe → Fig. |
q | Removing and installing → Chapter. |
17 - | Hexagon bolt |
q | M14 x 1.5 x 90 |
q | 90 Nm and turn 90° further. |
q | Renew each time after removing. |
18 - | Front wishbone mounting |
q | Pressing out → Fig.. |
q | Pressing in → Fig.. |
19 - | Hexagon bolt |
q | 60 Nm and turn 90° further |
q | Always renew after removing |
If the pendulum support, item → Item, is made of aluminium, the specified torque is 70 Nm. |
Modifications to the screw → Chapter. |
20 - | Rubber bush |
21 - | Pendulum support |
At the start of production, supports with two and three holes for subframe mounting were produced. |
After a short startup phase, these were replaced by a support with one hole. |
Only the support with one hole will be supplied as a replacement part. |
If this support is installed in a vehicle which was previously fitted with a different support, two spacers must be attached, each 2.5 mm thick. |
Other modifications to the pendulum support → Chapter. |
22 - | Hexagon nut |
q | Renew each time after removing. |
23 - | Hexagon bolt |
q | 100 Nm |
q | Always renew after removing |
|
![]() |
![]()
|
![]() |
|
![]() |
|
![]() |
|
![]() |
|
![]() |