Leon Mk1
Repairing drive shaft, vehicles with manual gearbox 006 and automatic gearbox 099 |

Special tools and workshop equipment required |
t | Spindle -3207- |
t | Pliers -3340- |
t | Pliers -V.A.G 1275- |
t | Torque wrench -V.A.G 1331- |
t | Torque wrench -V.A.G 1332- |
t | Clamp tensioners -V.A.G 1682- |
|
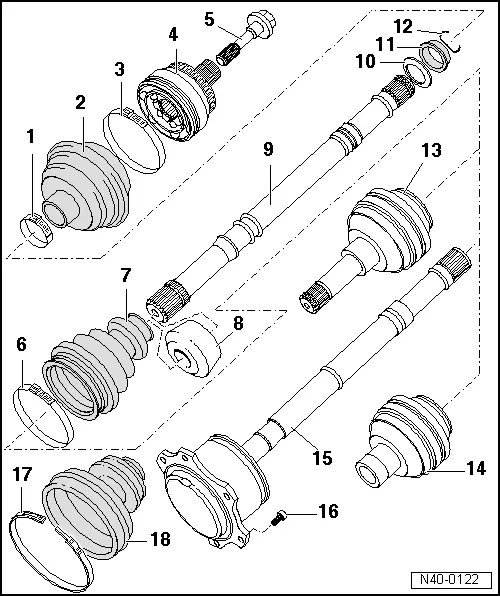
1 - | Clamp-type clip |
q | Renew. |
q | Tensioning → Fig.. |
2 - | Bellows for outer constant velocity joint |
q | Check for tears and chafing, renew if necessary. |
3 - | Clamp-type clip |
q | Renew. |
q | Tensioning → Fig.. |
4 - | Outer constant velocity joint |
q | Renew only complete. |
q | Pressing off → Fig.. |
q | Installing: drive onto shaft with plastic hammer until compressed circlip seats. |
q | Greasing → . |
q | Checking → Chapter. |
5 - | Hexagon bolt |
q | 150 Nm and turn 90° further. |
q | Renew each time after removing. |
6 - | Clamp-type clip |
q | Renew. |
q | Tension with -V.A.G 1275-. |
7 - | Bellows for inner constant velocity joint |
q | Check for tears and chafing, renew if necessary. |
q | Clean drive shaft thoroughly before installing new drive shaft bellows. |
8 - | Vibration damper |
q | Installation position → Fig.. |
9 - | Drive shaft |
10 - | Dished washer |
q | Installation position → Fig.. |
11 - | Thrust washer |
q | Installation position → Fig.. |
12 - | Circlip |
q | Renew. |
q | Remove and install with long nosed pliers. |
13 - | Left inner constant velocity joint |
q | Renew only complete. |
q | Driving off → Fig.. |
q | Greasing → . |
q | Checking → Chapter. |
14 - | Right inner constant velocity joint |
q | Renew only complete. |
q | Driving off → Fig.. |
q | Greasing → . |
q | Checking → Chapter. |
15 - | Drive shaft with outer joint (triple roller) |
q | Vehicles with 4-cyl. engine and automatic gearbox. |
q | Servicing inner joint is not possible. |
q | Renew if damaged. |
16 - | Allen head bolt |
q | Tighten using diagonal sequence to 10 Nm. |
q | Tighten to 70 Nm. |
q | Renew each time after removing. |
17 - | Clamp-type clip |
q | Tensioning → Fig.. |
18 - | Bellows for inner constant velocity joint (triple roller) |
q | Vehicles with 4-cyl. engine and automatic gearbox. |
q | Remove outer constant velocity joint if joint bellows is to be renewed. |
q | Clean drive shaft thoroughly before installing new drive shaft bellows. |
|
![]() |
![]()
|
![]() |
|
![]() |
|
![]() |
|
![]() |
|
![]() |
|
![]() |