Golf Mk4
Assembly overview - repairing propshaft |
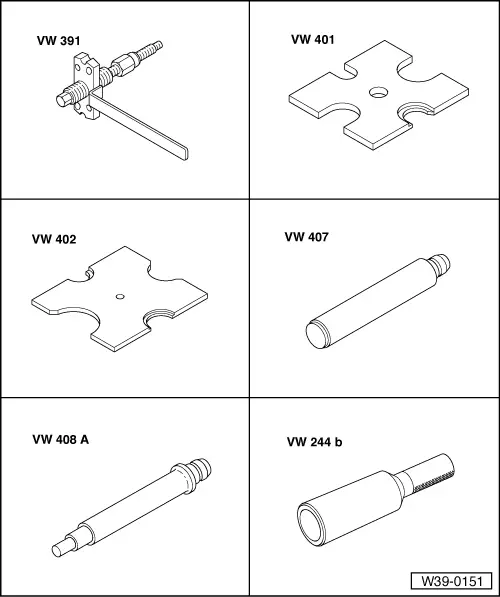
Special tools and workshop equipment required |
t | Drive shaft fitting appliance -VW 391- |
t | Pressure plate -VW 401- |
t | Pressure plate -VW 402- |
t | Press tool -VW 407- |
t | Press tool -VW 408A- |
t | Drift sleeve -VW 244B- |
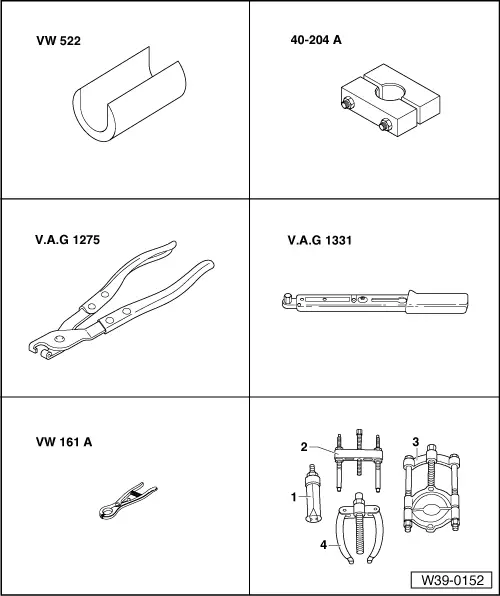
t | Support sleeve -VW 522- |
t | Tensioner -40 - 204 A- |
t | Hose clip pliers -V.A.G 1275/- |
t | Torque wrench -V.A.G 1331/- |
t | Circlip pliers -VW 161 A- |
t | Puller -2 - Kukko 18/0- |
t | Splitter -3 - Kukko 17/1- |
![]()
|
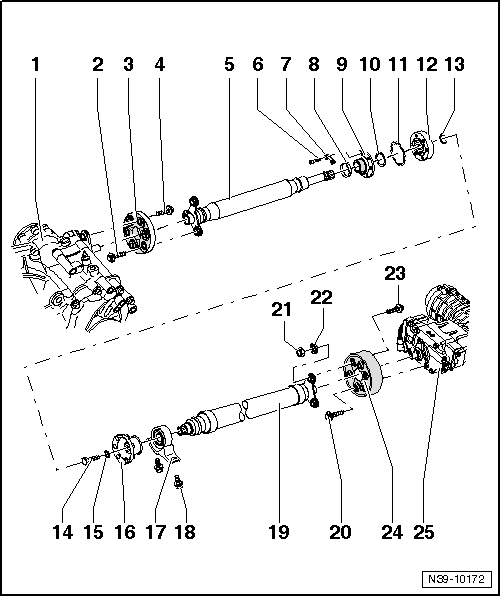
1 - | Gearbox with bevel box |
2 - | 12-point flange bolt, 60 Nm |
3 - | Flexible coupling with heat shield |
q | Removing and installing → Chapter |
q | Installation position → Fig. |
4 - | 12-point flange bolt, 60 Nm |
5 - | Front propshaft tube |
q | Do not damage centring sleeve or seal inside flange when removing and installing. |
6 - | Socket head bolt, 40 Nm |
7 - | Locking plate |
8 - | Clamp |
q | Tightening → Fig. |
9 - | Constant velocity joint boot |
q | Drive off with a drift before pressing off constant velocity joint |
q | Check for damage |
10 - | Dished washer |
q | Inner circumference serrated. |
q | Installation position: Large diameter lies against constant velocity joint. |
11 - | Seal |
q | Renewing: pull off protective foil and stick onto joint. |
12 - | Constant velocity joint |
q | Pressing off → Fig. |
q | Pressing on → Fig. |
q | Filling with grease: press 25 g grease -G6.3- into joint from each side (50 g total). Add grease if necessary when renewing joint boot. |
13 - | Retaining ring |
q | Renew |
q | Remove and install with circlip pliers -VW 161A-. |
14 - | Hexagon bolt, 45 Nm |
15 - | Washer |
q | Always renew |
16 - | Flange |
q | Pulling off → Fig. |
q | Pulling on → Fig. |
17 - | Intermediate bearing |
q | Pulling off → Fig. |
q | Installation position → Fig. |
q | Driving on → Fig. |
18 - | Bolt, 25 Nm |
19 - | Rear propshaft tube |
q | Do not damage centring sleeve or seal inside flange when removing and installing. |
20 - | 12-point flange bolt, 60 Nm |
q | Modification: from 06.99, new securing bolts with 12-point socket heads. |
q | Two of the new securing bolts might be installed with balancing discs instead of washers. |
q | Balancing washers on bolts have been discontinued with introduction of balancing nuts → Item and balancing washers → Item on bolts → Item. |
21 - | Balancing nut |
q | Not fitted on all propshafts. |
q | If flange bolt → Item is loosened, balancing nut and balancing washer → Item must not be reinstalled. |
22 - | Balancing washer |
q | Not fitted on all propshafts. |
q | If flange bolt → Item is loosened, balancing nut and balancing washer → Item must not be reinstalled. |
23 - | 12-point flange bolt, 60 Nm |
q | Modification: From 09.02 onwards, new securing bolts with balancing nuts → Item and balancing washers → Item were introduced for some propshafts |
q | Two of the new securing bolts might be installed with a balancing nut and balancing washer. |
q | If securing bolts are unscrewed, balancing washer and balancing nut are not allowed to be reinstalled |

Balancing washers in conjunction with bolt → Item are not installed then. |
24 - | Flexible coupling with vibration damper |
q | Removing and installing → Chapter |
q | Installation position → Fig. |
25 - | Rear final drive |
|
![]() |
|
![]() |
|
![]() |
|
![]() |
|
![]() |
|
![]() |
|
![]() |