Golf Mk4
Assembly overview - output shaft |
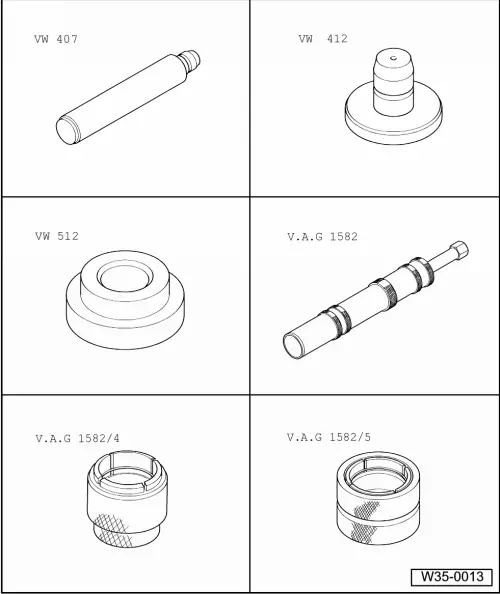
Special tools and workshop equipment required |
t | Press tool -VW 407- |
t | Press tool -VW 412- |
t | Thrust pad -VW 512- |
t | Puller -V.A.G 1582- |
t | Adapter -V.A.G 1582/4- |
t | Adapter -V.A.G 1582/5- |
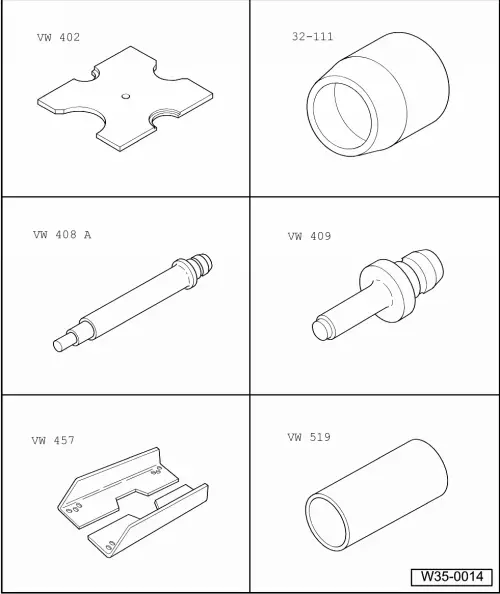
t | Pressure plate -VW 402- |
t | Thrust piece -32 - 111- |
t | Press tool -VW 408 A- |
t | Press tool -VW 409- |
t | Support rails -VW 457- |
t | Tube -VW 519- |
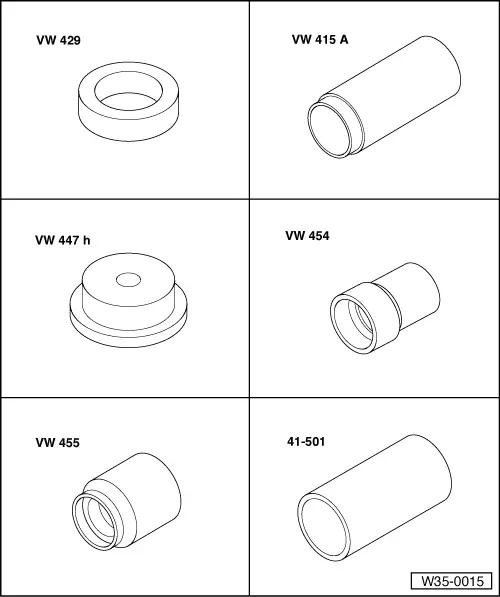
t | Thrust ring -VW 429- |
t | Tube -VW 415 A- |
t | Thrust pad -VW 447 H- |
t | Thrust piece -VW 454- |
t | Installing sleeve -VW 455- |
t | Drift sleeve - 41 - 501- |
|
|
![]() |
![]()
![]()
|
![]() |
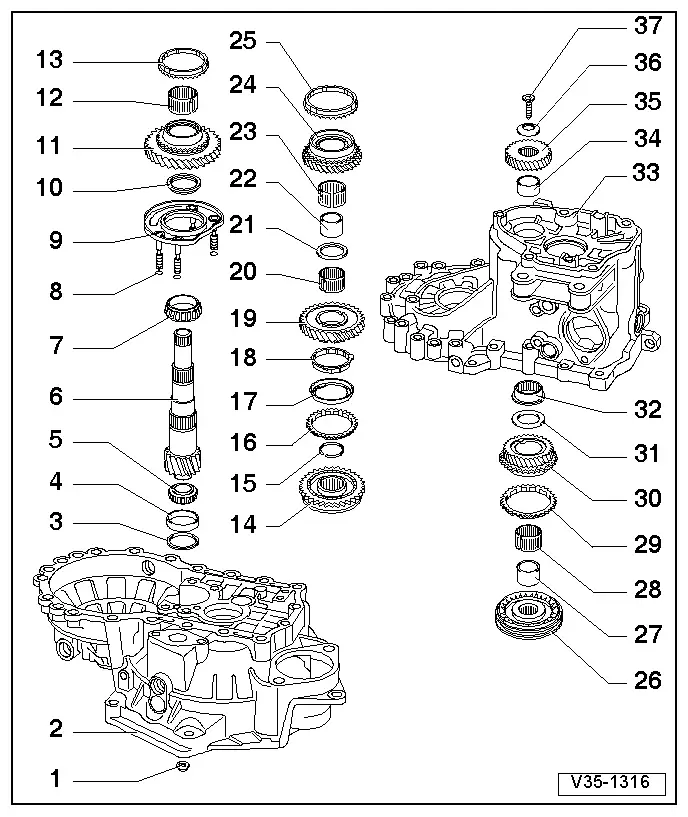
1 - | Hexagon nut |
q | → Item |
2 - | Clutch housing |
3 - | Shim |
q | Determining thickness → Chapter |
4 - | Small tapered roller bearing outer race |
q | Removing → Fig. |
q | Pressing in → Fig. |
5 - | Small tapered roller bearing inner race |
q | Pulling off → Fig. |
q | Pressing on → Fig. |
6 - | Output shaft |
q | Paired with final drive gear wheel. Always renew as a set. |
q | Adjusting → Chapter |
7 - | Large tapered roller bearing inner race |
q | Pulling off → Fig. |
q | Pressing on → Fig. |
8 - | Seal |
q | Always renew |
q | Place sealing rings (Qty. 4) on bearing support bolts |
9 - | Bearing support |
q | With large tapered roller bearing outer race and bolts |
q | Change outer race only together with large tapered roller bearing and bearing support |
10 - | Thrust washer |
q | Shoulder of thrust washer faces tapered roller bearing |
11 - | Synchromeshed gear for 1st gear |
q | From gearbox date 04 09 0 onwards, 1st gear synchronisation was changed → Chapter |
12 - | Needle bearing |
q | For 1st gear |
13 - | Synchro-ring for 1st gear |
q | Check for wear → Fig. |
q | Identification → Fig. |
q | Distinguishing → Fig. |
q | From gearbox date 04 09 0 onwards, 1st gear synchronisation was changed → Chapter |
14 - | Locking collar with synchro-hub for 1st and 2nd gears |
q | After removing retaining ring → Item, pull off via bearing support → Fig. |
q | Dismantling → Fig. |
q | Assembling locking collar and synchro-hub → Fig. |
q | Installation position → Fig. |
q | Pressing on → Fig. |
q | From gearbox date 04 09 0 onwards, 1st gear synchronisation was changed → Chapter |
15 - | Retaining ring |
16 - | Synchro-ring for 2nd gear |
q | Identification → Fig. |
q | Distinguishing → Fig. |
q | Check for wear → Fig. |
q | Assemble so that notches engage in locking pieces of locking collar → Item |
17 - | Outer ring |
q | Insert in synchro-ring → Item; installation position → Fig. |
q | Renew if scored |
18 - | Synchro-ring |
q | (Inner ring) |
q | Check for wear → Fig. |
q | Check lugs for scoring |
q | Installation position → Fig. |
19 - | Synchromeshed gear for 2nd gear |
q | Installation position → Fig. |
20 - | Needle bearing |
q | For 2nd gear |
21 - | Thrust washer |
22 - | Sleeve for 3rd gear needle bearing. |
q | Pressing off with synchromeshed gear for 2nd gear → Fig. |
q | Pressing on → Fig. |
23 - | Needle bearing |
q | For 3rd gear |
24 - | Synchromeshed gear for 3rd gear |
25 - | Synchro-ring for 3rd gear |
q | Check for wear → Fig. |
26 - | Locking collar with synchro-hub for 3rd and 4th gears |
q | Press off with 2nd gear synchromeshed gear → Item and 3rd gear → Item → Fig.. |
q | Dismantling → Fig. |
q | Installation position, locking collar and synchro-hub → Fig. |
q | Assembling locking collar and synchro-hub → Fig. |
q | Pressing on → Fig. |
27 - | Sleeve |
q | For needle bearing |
q | Press off with locking collar and synchro-hub for 3rd and 4th gears → Item |
q | Pressing on → Fig. |
28 - | Needle bearing |
q | For 4th gear |
29 - | Synchro-ring for 4th gear |
q | Check for wear → Fig. |
30 - | Synchromeshed gear for 4th gear |
31 - | Thrust washer |
32 - | Needle bearing |
q | For output shaft |
q | Removing and installing → Chapter |
33 - | Gearbox housing |
34 - | Sleeve |
q | For output shaft needle roller bearing |
q | Pressing off → Fig. |
q | Pressing on → Fig. |
35 - | Gear wheel for 5th gear |
q | Removing and installing → Chapter |
36 - | Dished washer |
q | Installation position → Anchor |
37 - | Torx socket head bolt M10 |
q | → Item |
|
![]() |
|
![]() |
|
![]() |
|
![]() |
![]()
|
![]() |
|
![]() |
|
![]() |
|
![]() |
Gap “a” | Installation (new) dimension | Wear limit |
1st gear 3rd gear 4th gear | 1.0 ... 1.7 mm 1.0 … 1.7 mm 1.0 … 1.7 mm | 0.5 mm |
|
![]() |
|
![]() |
|
![]() |
|
![]() |
|
![]() |
![]()
|
![]() |
|
![]() |
Gap “a” | Installation (new) dimension | Wear limit |
2nd gear | 1.2 ... 1.8 mm | 0.5 mm |
|
![]() |
|
![]() |
Gap “a” | Installation (new) dimension | Wear limit |
2nd gear | 0.75 ... 1.25 mm | 0.3 mm |
|
![]() |
|
![]() |
|
![]() |
|
![]() |
|
![]() |
|
![]() |
|
![]() |
|
![]() |
|
![]() |