Golf Mk4
Dismantling and assembling pistons and conrods |
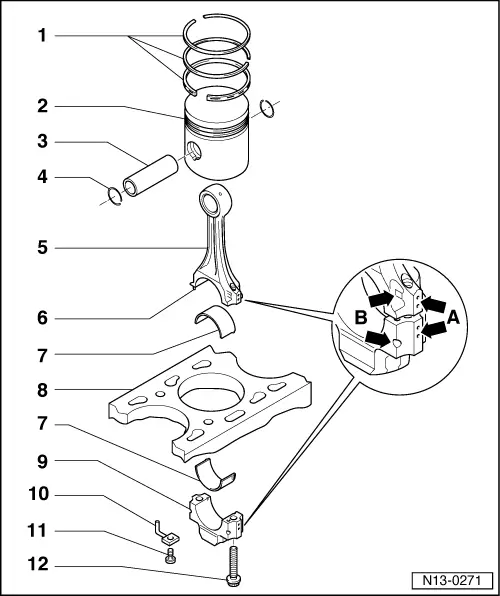
1 - | Piston rings |
q | Offset gaps by 120°. |
q | Remove and install using piston ring pliers. |
q | “TOP” faces towards piston crown. |
q | Checking ring gap → Fig.. |
q | Checking ring-to-groove clearance → Fig.. |
2 - | Piston |
q | With combustion chamber. |
q | Mark installation position and cylinder number. |
q | Installation position and allocation of piston to cylinder → Fig. |
q | Arrow on piston crown points to pulley end. |
q | Install using piston ring clamp. |
q | If piston skirt is cracked, renew piston. |
q | Checking piston projection at TDC → Chapter. |
3 - | Piston pin |
q | If difficult to remove, heat piston to 60 °C. |
q | Remove and install with drift -VW 222 A-. |
4 - | Circlip |
5 - | Conrod |
q | Renew as set only. |
q | Mark cylinder number -A- |
q | Installation position: marking -B- faces towards pulley end |
6 - | Fitted pin |
q | The dowel pins must sit firmly in the conrod, not in the cover |
7 - | Bearing shell |
q | Observe different types: on engine code AHF, ASV, upper bearing shell (towards piston) is made of a more wear resistant material and can be identified by a black line on the bearing surface in the area of the joint. |
q | Note installation position. |
q | Do not interchange used bearing shells. |
q | Ensure retaining lug fits tightly in recess |
q | Axial clearance wear limit: 0.37 mm. |
q | Measure radial clearance with Plastigage: Wear limit: 0.08 mm, do not rotate crankshaft when measuring radial clearance. |
8 - | Cylinder block |
q | Checking cylinder bores → Fig.. |
q | Piston and cylinder dimensions → Chapter. |
9 - | Conrod bearing cap |
q | Note installation position. |
10 - | Oil spray jet |
q | For piston cooling. |
11 - | 25 Nm |
q | Insert without sealant. |
12 - | Conrod bolt, 30 Nm + 1/4 turn (90°) further |
q | Renew. |
q | Oil threads and contact surface. |
q | Use old bolts to measure radial clearance. |
|
![]() |
Piston ring dimensions in mm | New | Wear limit |
1st compression ring | 0.20 …0.40 | 1.0 |
2nd compression ring | 0.20 …0.40 | 1.0 |
Oil scraper ring | 0.25 …0.50 | 1.0 |
|
![]() |
Piston ring dimensions in mm | New | Wear limit |
1st compression ring | 0.06 …0.09 | 0.25 |
2nd compression ring | 0.05 …0.08 | 0.25 |
Oil scraper ring | 0.03 …0.06 | 0.15 |
![]()
|
![]() |