A3 Mk2
![]() |
|
![]() |
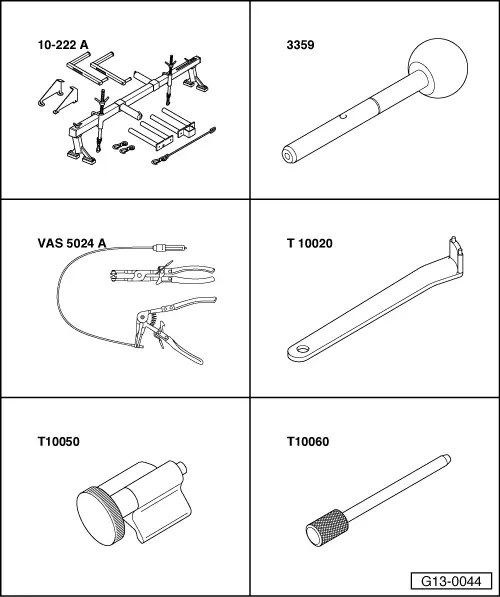
Special tools and workshop equipment required |
t | Support bracket -10-222 A- |
t | Diesel injection pump locking pin -3359- |
t | Hose clip pliers -VAS 6340- or -VAS 5024 A- |
t | Pin wrench -T10020- |
t | Crankshaft stop -T10050- for engines with circular crankshaft sprocket |
t | Locking pin -T10060 A- or -T10060- |
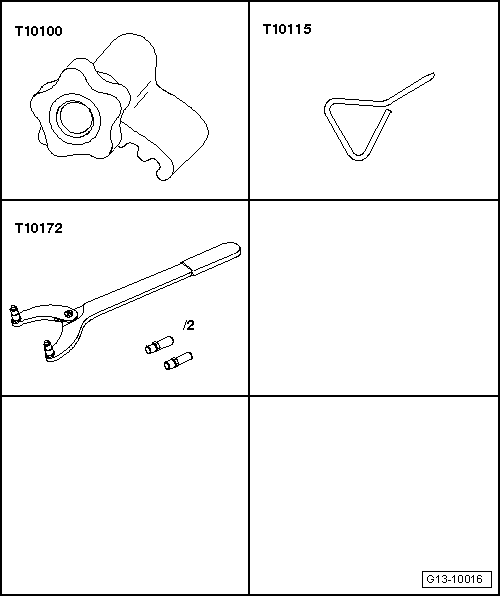
t | Crankshaft stop -T10100- for engines with oval crankshaft sprocket |
t | Locking pin -T10115- |
t | Counterhold tool -T10172- |
t | Locking fluid → Parts catalogue |
|
![]() |
![]()
|
![]() |
|
![]() |
|
![]() |
|
![]() |
|
![]() |
![]() |
![]() |
|
![]() |
|
![]() |
|
![]() |
|
![]() |
|
![]() |
|
![]() |
|
![]() |
|
![]() |
|
![]() |
|
![]() |
![]()
|
![]() |
![]()
|
![]() |
![]()
|
![]() |
|
![]() |
![]()
|
![]() |
|
![]() |
|
![]() |
![]()
![]()
|
![]() |
|
![]() |
|
![]() |
![]()
|
![]() |
![]()
|
![]() |
Component | Nm | |||||||||
Tensioning roller for toothed belt to cylinder head | 20 + 45° 1) | |||||||||
Camshaft sprocket to hub | 25 | |||||||||
Toothed belt cover (bottom) to cylinder block | 10 2) | |||||||||
Toothed belt cover (centre) to cylinder block | 10 2) | |||||||||
Engine mounting to body | 50 | |||||||||
Connecting bracket to engine mounting/body | 20 + 90° 3)4) | |||||||||
Tensioner for poly V-belt to bracket for ancillaries | 23 | |||||||||
Air pipes to engine | 8 | |||||||||
|