A3 Mk2
|
Grease G 600 003 | Outer joint |
Total quantity | 120 g |
In joint | 80 g |
In boot | 40 g |
Grease G 000 605 | Triple roller joint |
Total quantity | 140 g |
In joint | 70 g |
In boot | 70 g |
![]()
|
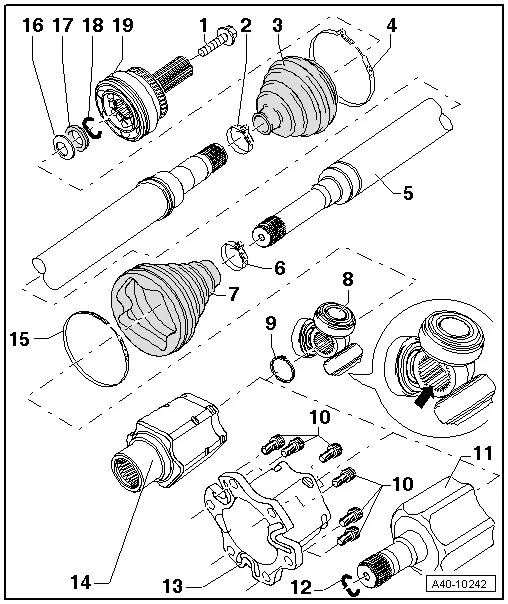
1 - | Bolt |
q | Always renew if removed |
q | Different versions; for correct version refer to → Electronic parts catalogue |
q | Hexagon bolt = 200 Nm + turn 180° further; loosening and tightening → Chapter |
q | Twelve-point ribbed bolt = 70 Nm + turn 90° further; loosening and tightening → Chapter |
q | Twelve-point bolt without ribbing = 200 Nm + turn 180° further; loosening and tightening → Chapter |
q | Before securing, clean the threads in the CV joint using a thread tap. |
2 - | Hose clip |
q | Always renew if removed |
q | Tightening → Fig. or → Fig. |
3 - | Boot for constant velocity joint |
q | Check for splits and chafing |
4 - | Hose clip |
q | Always renew if removed |
q | Tightening → Fig. or → Fig. |
5 - | Profile shaft |
6 - | Hose clip |
q | Always renew if removed |
q | Tightening → Fig. or → Fig. |
7 - | Boot for triple roller joint |
q | Check for splits and chafing |
8 - | Triple roller spider with rollers |
q | Chamfer -arrow- faces towards drive shaft splines |
q | Grease splines on drive shaft lightly with grease used in joint when fitting triple roller spider onto drive shaft |
9 - | Circlip |
q | Always renew if removed |
10 - | Multi-point socket head bolt |
q | Always renew if removed |
q | Initial tightening torque: 10 Nm in diagonal sequence |
q | Tightening torque, M8: 40 Nm in diagonal sequence |
q | Tightening torque, M10: 70 Nm in diagonal sequence |
11 - | Joint body (version with splines) |
q | Before installing, grease splines on joint with G052735 |
12 - | Circlip |
q | Always renew if removed |
q | Insert in groove on shaft |
13 - | Joint body (version with bolted flange) |
14 - | Joint body (version with internal splines) |
15 - | Hose clip |
q | Always renew if removed |
q | Tightening → Fig. or → Fig. |
16 - | Dished spring |
q | Installation position → Fig. |
17 - | Spacer ring (plastic) |
q | Installation position → Fig. |
18 - | Circlip |
q | Always renew if removed |
q | Insert in groove on shaft |
19 - | Outer constant velocity joint |
q | Renew only as complete unit |
q | Removing → Fig. |
q | Checking → Chapter |
q | Greasing ⇒ see table → Anchor |
q | Installing → Anchor |
q | Drive joint onto shaft with plastic hammer until circlip engages |
q | Grease splines on drive shaft lightly with grease used in joint when fitting joint onto drive shaft |
|
![]() |
|
![]() |
|
![]() |
|
![]() |
|
![]() |
|
![]() |
|
![]() |