A4 Mk2
Dismantling and assembling pinion shaft and hollow shaft |
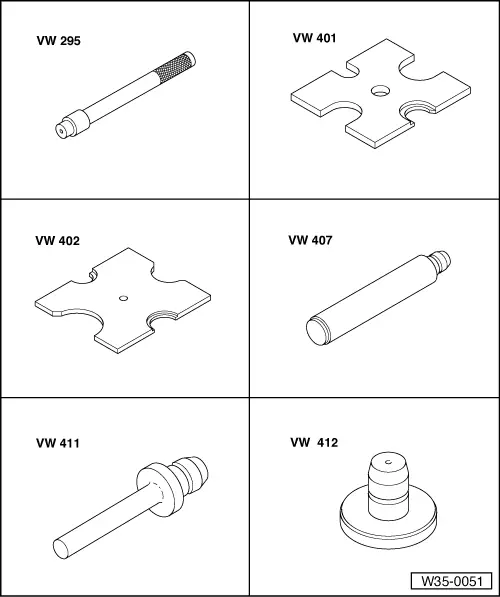
Special tools and workshop equipment required |
t | Drift -VW 295- |
t | Thrust plate -VW 401- |
t | Thrust plate -VW 402- |
t | Press tool -VW 407- |
t | Press tool -VW 411- |
t | Press tool -VW 412- |
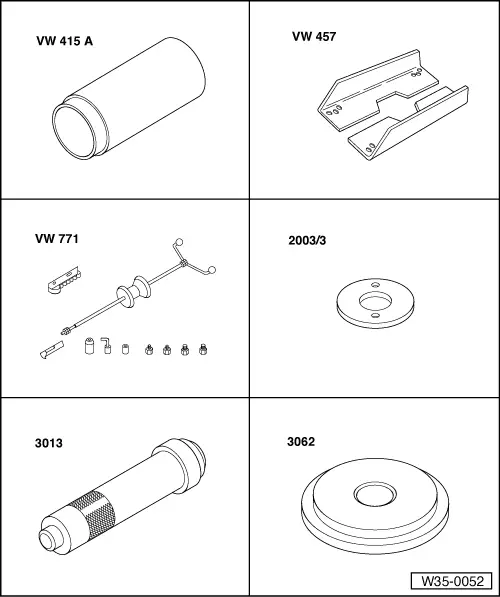
t | Tube -VW 415 A- |
t | Support rails -VW 457- |
t | Multi-purpose tool -VW 771- |
t | Installing ring -2003/3- |
t | Punch -3013- |
t | Thrust pad -3062- |

t | Press tool -3118- |
t | Drift -3138- |
t | Hot air blower -V.A.G 1416- |
t | -1-Internal puller -Kukko 21/1- |
t | -3-Splitter -Kukko 17/2- |
Exploded view |

t | When installing new gears or final drive gear set → Chapter „Code letters, allocation, transmission ratios, capacities“. |
t | Adjustment work is required when renewing the parts marked with 1) → Anchor. |
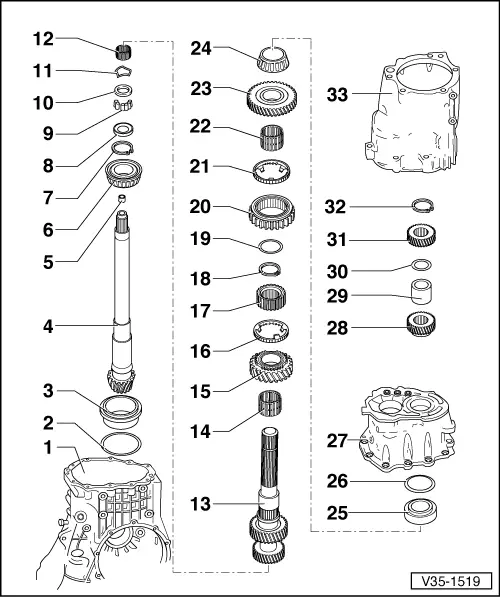
1 - | Gearbox housing |
q | Servicing → Chapter |
2 - | Shim “S3” |
q | Table of adjustments → Anchor |
3 - | Outer race for large tapered roller bearing 1) |
q | Pulling out → Fig. |
q | Pressing in → Fig. and → Fig. |
4 - | Pinion shaft 1) |
q | Paired with crown wheel (final drive gear set) |
q | Adjusting pinion shaft and crown wheel → Chapter |
5 - | Needle roller bearing for flange shaft/pinion shaft |
q | Pulling out → Fig. |
q | Driving in → Fig. |
6 - | Inner race for large tapered roller bearing 1) |
q | Pressing off → Fig. |
q | Pressing on → Fig. |
q | Low-friction bearing; do not oil bearing when measuring friction torque |
7 - | Circlip |
q | Re-determining thickness → Fig. |
8 - | Flange ring |
q | Installation position → Anchor |
9 - | Tapered rollers |
q | 23 x |
q | Installation position → Anchor |
10 - | Support ring |
q | Installation position → Anchor |
11 - | Corrugated spring |
12 - | Needle bearing for pinion shaft/hollow shaft |
q | Lubricate with gear oil before installing |
13 - | Hollow shaft with 3rd and 4th gear wheels 1) |
14 - | Needle bearing for 2nd speed selector gear |
q | Split |
q | Lubricate with gear oil before installing |
15 - | 2nd speed selector gear |
q | Pressing off → Fig. |
q | Before installing, fit spring and slide needle bearing onto hollow shaft |
q | After installing, check axial clearance with a feeler gauge (0.15 ... 0.35 mm) |
16 - | Synchro-ring for 2nd gear |
q | With molybdenum coating |
q | Checking for wear → Fig. |
17 - | Synchronising hub for 1st and 2nd gear |
q | Pressing off → Fig. |
q | Pressing on → Fig. |
q | Installation position: flush hub towards 2nd speed selector gear |
18 - | Circlip |
q | Removing and installing → Fig. |
q | Re-determining thickness → Fig. |
19 - | Shim for needle bearing for 1st speed selector gear |
q | Removing and installing → Fig. |
20 - | Locking collar for 1st and 2nd gear |
q | Installation position: splines for reverse gear towards synchro-ring for 2nd gear |
21 - | Synchro-ring for 1st gear |
q | Checking for wear → Fig. |
22 - | Needle bearing for 1st speed selector gear |
q | Lubricate with gear oil before installing |
23 - | 1st speed selector gear |
q | Before installing, insert spring → Fig. |
q | After pressing on → Item, check axial clearance (0.15 ... 0.35 mm) |
24 - | Inner race for small tapered roller bearing 1) |
q | Pressing off → Fig. |
q | Pressing on → Fig. |
q | Low-friction bearing; do not oil bearing when measuring friction torque |
25 - | Outer race for small tapered roller bearing 1) |
q | Driving out → Fig. |
q | Pressing in → Fig. |
26 - | Shim “S4” |
q | Table of adjustments → Anchor |
27 - | Intermediate housing 1) |
q | Servicing → Chapter |
28 - | 6th gear wheel |
q | Pressing off → Anchor |
q | Pressing on → Anchor |
q | Installation position: shoulder towards inner race for small tapered roller bearing |
29 - | Spacer sleeve |
30 - | Shim |
q | Re-determining thickness → Anchor |
31 - | 5th gear wheel |
q | Pulling off → Anchor |
q | Driving on → Anchor |
32 - | Circlip for 5th gear wheel |
q | Re-determining thickness → Anchor |
33 - | End cover |
q | Servicing → Chapter |
![]()
|
![]() |
|
![]() |
|
![]() |
|
![]() |
|
![]() |
|
![]() |
![]()
|
![]() |
|
![]() |
|
![]() |
Available circlips - Thickness in mm 1) | ||||
2.34 | 2.40 | 2.46 | ||
2.36 | 2.42 | 2.48 | ||
2.38 | 2.44 | |||
|
|
![]()
|
![]() |
|
![]() |
|
![]() |
![]()
|
![]() |
|
![]() |
|
![]() |
Available circlips - Thickness in mm 1) | ||||
1.90 | 1.96 | 2.02 | ||
1.93 | 1.99 | |||
|
|
|
![]() |
|
![]() |