Octavia Mk1
![]()
|
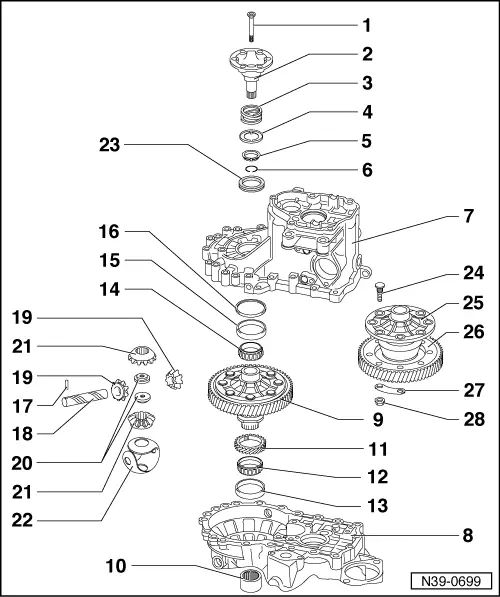
1 - | Screw, 25 Nm |
q | screw to threaded connector to attach the flange shaft (⇒ Pos. 20) |
2 - | Flange shaft |
q | with hole for conical screw |
q | removing and installing → Chapter |
3 - | Pressure spring for flange shaft |
q | fitted behind flange shaft |
4 - | Thrust washer |
q | Fitting position: Flange to pressure spring, leg to conical ring |
5 - | Conical ring |
q | with slots for thrust washer catch |
q | Fitting position: Cone towards differential gear housing |
6 - | Circlip |
q | holds the conical ring, stop disc and pressure spring in position when the flange shaft is removed |
7 - | Gearbox housing |
8 - | Clutch housing |
9 - | Differential gear housing |
q | with riveted pinion for final drive |
q | when replacing the final drive pinion bore out the rivet heads → Fig. |
q | Secure pinion for final drive with screws → Fig. |
10 - | Coupling sleeve to angle gearbox |
q | pressed onto differential housing |
q | pulling off and pressing on only with the differential housing removed |
q | remove → Fig. |
q | pressing on → Fig. |
11 - | Drive wheel for speedometer |
q | before pressing on the inner ring place it on the differential gear housing up to the stop |
12 - | Inner ring/tapered-roller bearing |
q | before removal, pull off coupling sleeve (⇒ Pos. 10) |
q | remove → Fig. |
q | pressing on → Fig. |
13 - | Outer ring/tapered-roller bearing |
q | extracting → Fig. |
q | installing → Fig. |
14 - | Inner ring/tapered-roller bearing |
q | remove → Fig. |
q | pressing on → Fig. |
15 - | Outer ring/tapered-roller bearing |
q | extracting → Fig. |
q | installing → Fig. |
16 - | Adjusting washer |
q | for the differential gear |
q | Determine thickness → Chapter |
17 - | Tensioning sleeve |
q | to secure the differential bevel gear shaft |
q | removing and installing → Fig. |
18 - | Differential bevel gear shaft |
q | drive out with -MP3-510- |
q | installing → Fig. |
19 - | Differential bevel gear small |
q | installing → Fig. |
20 - | Threaded part |
21 - | Differential bevel gear large |
q | installing → Fig. |
22 - | Stop disc compound |
q | insert with gear oil |
23 - | Gasket ring |
q | replace → Chapter |
24 - | Screw |
25 - | Differential gear housing |
q | screwed to pinion for final drive → Fig. |
26 - | Pinion for final drive |
q | series riveted |
q | screw → Fig. |
q | heat to 100 °C before fitting |
q | pressing off → Fig. |
q | Fitting position → Fig. |
q | place on differential housing → Fig. |
q | is paired with the output shaft, replace together |
27 - | Shim |
28 - | 70 Nm |
|
![]() |
|
![]() |
![]()
|
![]() |
|
![]() |
|
![]() |
![]()
|
![]() |
|
![]() |
|
![]() |
|
![]() |
|
![]() |
|
![]() |
|
![]() |
|
![]() |
|
![]() |