A1
Exploded view - dismantling and assembling input shaft |
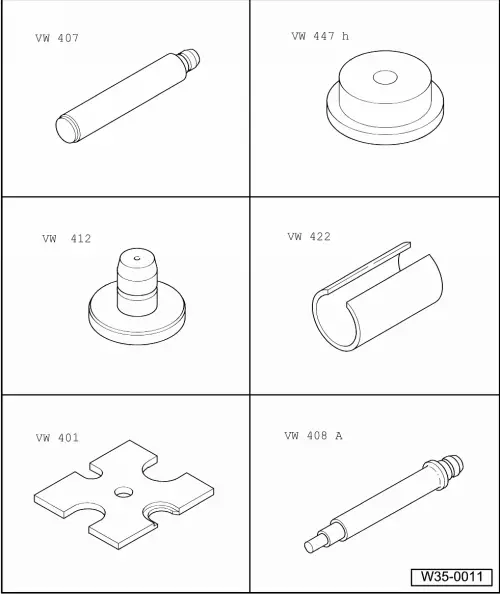
Special tools and workshop equipment required |
t | Press tool -VW 407- |
t | Thrust plate -VW 447 H- |
t | Press tool -VW 412- |
t | Tube -VW 422- |
t | Thrust plate -VW 401- |
t | Thrust plate -VW 402- |
t | Press tool -VW 408 A- |
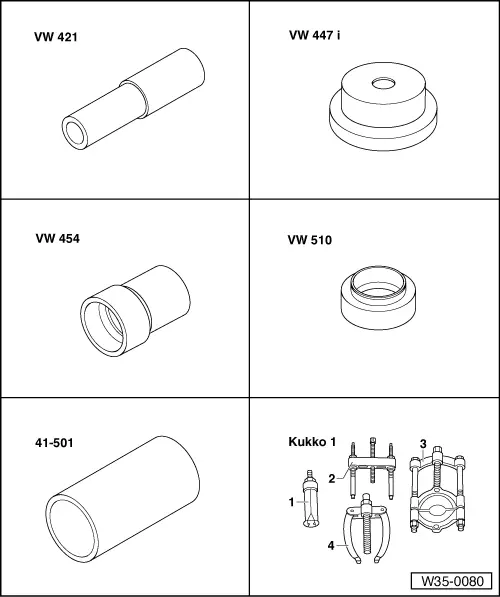
t | Tube -VW 421- |
t | Press tool -VW 454- |
t | Thrust plate -VW 447 i- |
t | Thrust pad -VW 510- |
t | Drift sleeve -41-501- |
t | -3-Splitter -Kukko 17/1- |

t | When fitting new gear wheels or input shaft, refer to technical data → Chapter and → Electronic parts catalogue. |
t | The input shaft must be re-adjusted if the position of tapered roller bearings is affected when renewing parts. Refer to table of adjustments → Chapter. |
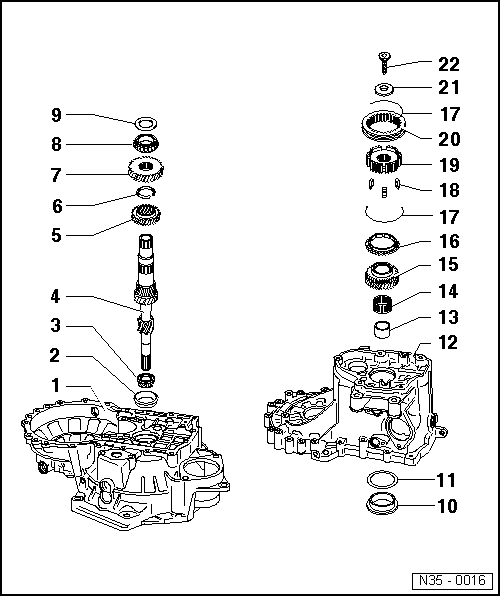
1 - | Clutch housing |
2 - | Tapered roller bearing outer race |
q | Pressing out → Fig. |
q | Pressing in → Fig. |
3 - | Tapered roller bearing inner race |
q | Pressing off → Fig. |
q | Pressing on → Fig. |
4 - | Input shaft |
q | Adjusting → Chapter |
5 - | 3rd gear wheel |
q | Installation position: Collar faces 4th gear |
q | Pressing off → Fig. |
q | Pressing on → Fig. |
6 - | Circlip |
q | Always renew |
7 - | 4th gear wheel |
q | Pressing off with tapered roller bearing outer race and sleeve → Fig. |
q | Pressing on → Fig. |
q | Shoulder faces towards 3rd gear |
8 - | Tapered roller bearing inner race |
q | Pressing off with 4th gear wheel and sleeve → Fig. |
q | Pressing on → Fig. |
9 - | Thrust washer |
10 - | Tapered roller bearing outer race |
q | Pressing out → Fig. |
q | Pressing in → Fig. |
11 - | Shim |
q | Determining thickness → Chapter |
12 - | Gearbox housing |
13 - | Sleeve |
q | For needle bearing |
q | Press off with 4th gear wheel and tapered roller bearing inner race → Fig. |
q | Pressing on → Fig. |
q | Fit thrust washer → Item before installing |
14 - | Needle bearing |
15 - | 5th speed selector gear |
q | Pull off together with 5th gear synchro-hub → Chapter |
16 - | 5th gear synchro-ring |
q | With cast locking pieces → Fig. |
q | Checking for wear → Fig. |
17 - | Spring |
q | Offset version → Fig. |
q | Installation position → Fig. |
18 - | Locking pieces (3x) |
q | Installation position → Fig. |
19 - | 5th gear synchro-hub |
q | Pulling off individually → Chapter |
q | Pulling off together with gearbox housing → Chapter |
q | Dismantling and assembling → Fig. |
20 - | 5th gear locking collar |
q | Removing and installing → Chapter |
21 - | Dished spring |
q | Installation position → Fig. |
22 - | Bolt |
q | Tightening torque → Item |
q | Always renew |
q | Fitted piece on bolt head holds dished spring in position → Fig. |
|
![]() |
|
![]() |
|
![]() |
|
![]() |
|
![]() |
|
![]() |
|
![]() |
|
![]() |
|
![]() |
|
![]() |
|
![]() |
|
![]() |
|
![]() |
|
![]() |
|
![]() |