A4 Cabriolet Mk2
Removing and installing sump (top section) |
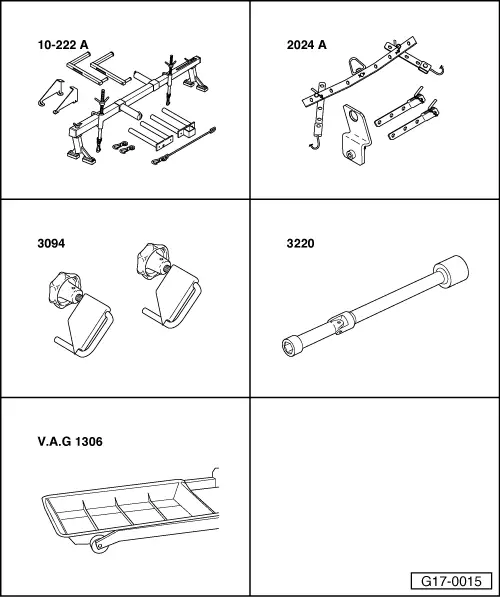
Special tools and workshop equipment required |
t | Support bracket -10-222 A- |
t | Lifting tackle -2024 A- |
t | Hose clamps for hoses up to 25 mm Ø -3094- |
t | U/J extension and socket, 10 mm -3220- |
t | Drip tray for workshop hoist -VAS 6208- or -V.A.G 1306- |
|
|
![]() |
|
![]() |
|
![]() |
|
![]() |
|
![]() |
|
![]() |
|
![]() |
|
![]() |
|
![]() |
![]() |
![]() |
|
![]() |
![]()
|
![]() |
![]()
|
![]() |
|
![]() |
|
![]() |
![]()
|
![]() |
|
![]() |
|
![]() |
![]()
|
![]() |
|
![]() |
![]()
|
![]() |
![]()
|
![]() |
|
![]() |
![]()
|
![]() |
|
![]() |
|
![]() |
|
![]() |
![]()
|
![]() |
|
![]() |
|
![]() |
![]()
|
![]() |
|
![]() |
|
![]() |
![]()
|
![]() |
|
![]() |
Component | Nm | |
Sump (top section) to cylinder block and sealing flanges | M7 | 16 |
M8 | 22 | |
Sump (top section) to gearbox | 45 | |
Bracket for noise insulation to subframe | 10 | |
Continued coolant circulation pump -V51- to sump (top section) | 10 | |
Engine mounting to subframe | 23 | |
Reservoir bracket to body | 10 | |
Refrigerant line bracket to sump | 10 | |
Secondary air pump bracket to longitudinal member | 10 | |
Oil cooler to sump (top section) | 30 | |
Guide tube for oil dipstick to secondary air pipe | 10 |