A4 Mk2
Dismantling and assembling pinion shaft up to 05.03 |
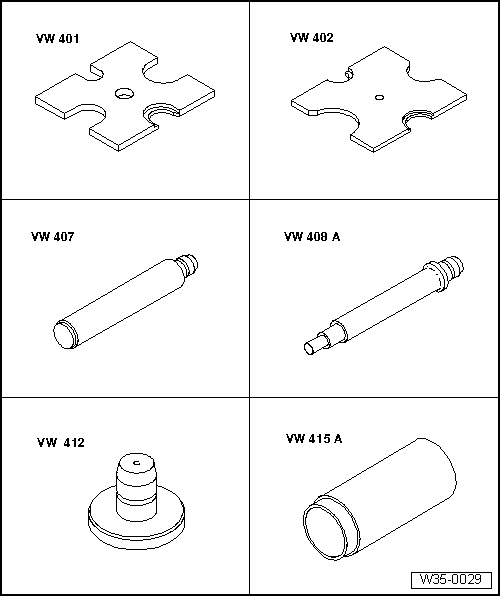
Special tools and workshop equipment required |
t | Thrust plate -VW 401- |
t | Thrust plate -VW 402- |
t | Press tool -VW 407- |
t | Press tool -VW 408 A- |
t | Press tool -VW 412- |
t | Tube -VW 415 A- |
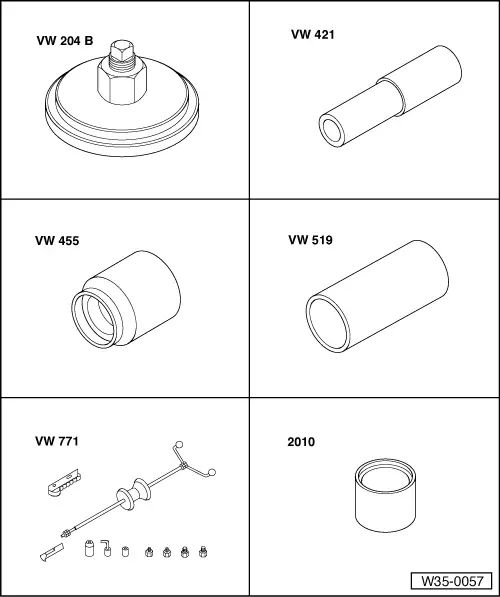
t | Crankshaft seal installing tool -VW 204 B- |
t | Tube -VW 421- |
t | Installing sleeve -VW 455- |
t | Tube -VW 519- |
t | Multi-purpose tool -VW 771- |
t | Tube -2010- |
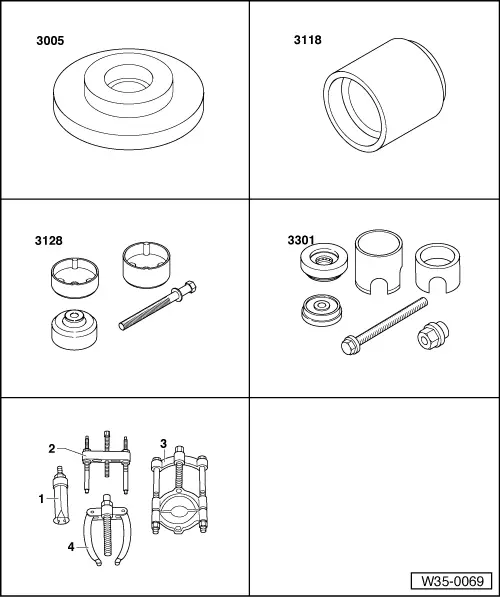
t | Thrust plate -3005- |
t | Press tool -3118- |
t | Fitting tool -3128- |
t | Assembly tool -3301- |
t | -1-Internal puller -Kukko 21/1- |
t | -1-Internal puller -Kukko 21/4- |
t | -3-Splitter -Kukko 17/2- |

t | From 05.03 onwards, a new type of synchromesh for 1st and 2nd gear as well as for 5th and reverse gear is fitted. Dismantling and assembling pinion shaft from 05.03 → Chapter. |
t | Refer to technical data → Chapter when installing new gear wheels or the final drive gear set. |
t | Adjustment work is required when renewing the parts marked with 1) → Chapter „Table of adjustments“. |
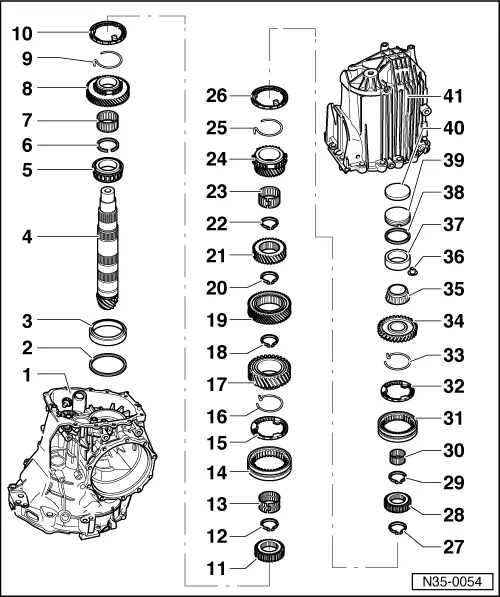
1 - | Gearbox housing 1) |
q | Housing manufactured from aluminium or magnesium → Item |
2 - | Shim “S3” |
q | Table of adjustments → Chapter |
3 - | Outer race for large tapered roller bearing 1) |
q | Pulling out → Fig. |
q | Pressing in → Fig. |
4 - | Pinion shaft 1) |
q | Is mated with crown wheel, always renew together as a set |
q | Adjusting pinion shaft and crown wheel → Chapter |
5 - | Inner race for large tapered roller bearing 1) |
q | Renew |
q | Will be damaged during removal |
q | Pressing off → Fig. |
q | Pressing on → Fig. |
6 - | Circlip |
q | Mark |
q | Installation position → Fig. |
q | Re-determine thickness if tapered roller bearing is renewed → Fig. |
7 - | Needle bearing for 1st gear |
8 - | 1st speed selector gear |
9 - | Spring |
q | Insert in 1st speed selector gear → Fig. |
q | Allocation to selector gear → Electronic parts catalogue |
10 - | Synchro-ring for 1st gear |
q | Checking for wear → Fig. |
11 - | Synchronising hub for 1st and 2nd gear |
q | Pressing off → Fig. |
q | Pressing on → Fig. |
12 - | Circlip |
q | Mark |
q | Installation position → Fig. |
q | Redetermine thickness if synchronising hub is replaced → Fig. |
13 - | Needle bearing for 2nd gear |
14 - | Locking collar for 1st and 2nd gear |
q | Installation position → Fig. |
15 - | Synchro-ring for 2nd gear |
q | Checking for wear → Fig. |
16 - | Spring |
q | Insert in 2nd speed selector gear → Fig. |
q | Allocation to selector gear → Electronic parts catalogue |
17 - | 2nd speed selector gear |
18 - | Circlip |
q | Mark |
q | Installation position → Fig. |
19 - | 3rd gear wheel |
q | Pressing off → Fig. |
q | Groove faces 4th gear |
q | Pressing on → Fig. |
20 - | Circlip |
q | Mark |
q | Installation position → Fig. |
q | If 3rd gear wheel is renewed redetermine thickness → Fig. |
21 - | 4th gear wheel |
q | Pressing off → Fig. |
q | Shoulder faces towards 3rd gear |
q | Pressing on → Fig. |
22 - | Circlip |
q | Mark |
q | Installation position → Fig. |
q | If 4th gear wheel is renewed redetermine thickness → Fig. |
23 - | Needle bearing |
24 - | 5th speed selector gear |
25 - | Spring |
q | Insert in 5th speed selector gear → Fig. |
q | Allocation to selector gear → Electronic parts catalogue |
26 - | Synchro-ring for 5th gear |
q | Checking for wear → Fig. |
27 - | Circlip |
q | Mark |
q | Installation position → Fig. |
28 - | 5th gear and reverse gear synchronising hub |
q | Pressing off → Fig. |
q | Pressing on → Fig. |
29 - | Circlip |
q | Mark |
q | Installation position → Fig. |
q | Redetermine thickness if synchronising hub is replaced → Fig. |
30 - | Needle bearing |
q | For reverse gear |
31 - | Locking collar for 5th and reverse gear |
q | Installation position → Fig. |
32 - | Synchro-ring for reverse gear |
q | Checking for wear → Fig. |
33 - | Spring |
q | Insert in reverse selector gear → Fig. |
q | Allocation to selector gear → Electronic parts catalogue |
34 - | Reverse selector gear |
35 - | Inner race for small tapered roller bearing 1) |
q | Pressing off → Fig. |
q | Pressing on → Fig. |
36 - | Bush |
q | Secures outer race for small tapered roller bearing |
q | Pulling out → Fig. |
q | Need not be refitted after the small taper roller bearing has been renewed |
37 - | Outer race for small tapered roller bearing 1) |
q | Pulling out → Fig. |
q | Pressing in → Fig. |
38 - | Shim “S4” |
q | Table of adjustments → Chapter |
39 - | Pressure plate |
q | Different thicknesses for aluminium and magnesium gearboxes → Fig. |
40 - | Rubber disc |
q | Compensates length variations |
q | To remove, screw self-tapping screw into centre of disc and use screw to pull out disc |
q | Different thicknesses for aluminium and magnesium gearboxes → Fig. |
q | Select correct version according to gearbox code letters → Electronic parts catalogue → Chapter |
41 - | Gearbox cover |
q | Aluminium version: must only be fitted to an aluminium gearbox housing |
q | Magnesium version: must only be fitted to a magnesium gearbox housing |
q | Note identification markings → Fig. |
q | Coat sealing surfaces lightly with sealing paste -AMV 188 001 02- |
q | Can be renewed with gearbox in vehicle → Chapter |
|
![]() |
|
![]() |
|
![]() |
|
![]() |
|
![]() |
|
![]() |
|
![]() |
|
![]() |
|
![]() |
|
![]() |
|
![]() |
|
![]() |
|
![]() |
![]()
|
![]() |
Circlip thickness (mm) | ||
2.00 | 2.06 | 2.12 |
2.03 | 2.09 | 2.15 |
|
Circlip thickness (mm) | ||
1.90 | 1.96 | 2.02 |
1.93 | 1.99 |
|
Circlip thickness (mm) | ||
2.50 |
|
Circlip thickness (mm) | ||
1.90 | 1.98 | 2.06 |
1.94 | 2.02 |
|
Circlip thickness (mm) | ||
1.86 | 1.94 | |
1.90 | 1.98 |
|
Circlip thickness (mm) | ||
2.00 |
|
Circlip thickness (mm) | ||
1.90 | 1.96 | 2.02 |
1.93 | 1.99 | 2.05 |
|
![]() |
|
![]() |
|
![]() |
|
![]() |
|
![]() |
![]()
|
![]() |
|
![]() |
|
![]() |
|
![]() |
A | Reverse gear wheel with chamfered surface | Both types of locking collar can be installed (with chamfered surface or with large shoulder) |
B | Reverse gear wheel without chamfered surface | Install only locking collar with large shoulder; do not use locking collar with chamfered edge |
|
![]() |
Gearbox housing | Distance -a- |
Aluminium | 14.8 or 15.3 mm |
Magnesium → Chapter | 10.7 mm |
|
![]() |
Gearbox housing | Distance -a- |
Aluminium | 7.0 mm |
Magnesium | 11.0 mm |