A4 Mk2
Removing and installing cylinder head |
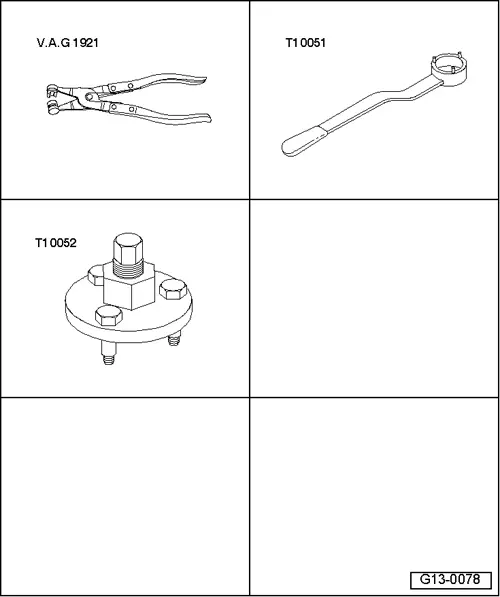
Special tools and workshop equipment required |
t | Hose clip pliers -V.A.G 1921- |
t | Counterhold tool -T10051- |
t | Puller -T10052- |
t | Safety goggles |
t | Protective gloves |
|
|
![]() |
![]()
|
![]() |
|
![]() |
![]()
|
![]() |
![]()
|
![]() |
|
![]() |
|
![]() |
|
![]() |
|
![]() |
|
![]() |
|
![]() |
|
![]() |
|
![]() |
|
![]() |
|
![]() |
|
![]() |
|
![]() |
|
![]() |
![]()
|
![]() |
![]()
|
![]() |
|
![]() |
|
![]() |
|
![]() |
|
![]() |
|
![]() |
|
![]() |
|
![]() |
|
![]() |
![]()
|
![]() |
![]()
|
![]() |
|
![]() |
|
![]() |
![]()
|
![]() |
|
![]() |
|
![]() |
![]()
|
![]() |
|
![]() |
|
![]() |
|
![]()
|
|
![]() |
|
![]() |
|
|
![]() |
|
![]() |
|
![]() |
|
![]() |
|
![]() |
Component | Nm | |||||||
Rocker arm shaft to cylinder head | 20 + 90° 1)2) | |||||||
Rear toothed belt cover to cylinder head | 10 3) | |||||||
Hall sender to cylinder head | 10 3) | |||||||
Stud to cylinder head | 15 | |||||||
Hub to camshaft | 100 | |||||||
Oil supply pipe to turbocharger | 22 | |||||||
Bracket for oil supply pipe to exhaust manifold | 22 | |||||||
Oil supply pipe to oil filter bracket | 22 | |||||||
Oil pressure switch to oil filter bracket | 20 | |||||||
Oil return pipe to cylinder block | 30 | |||||||
Guide tube for | Engine lifting eye | 10 | ||||||
oil dipstick to: | Oil filter bracket | 10 | ||||||
Bracket for | Turbocharger | 20 | ||||||
Turbocharger to: | Cylinder block | 40 | ||||||
Stop for torque reaction support to lock carrier | 28 | |||||||
Hose clips (9 mm wide) | 3 | |||||||
Hose clips (13 mm wide) | 5.5 | |||||||
|