Discovery II
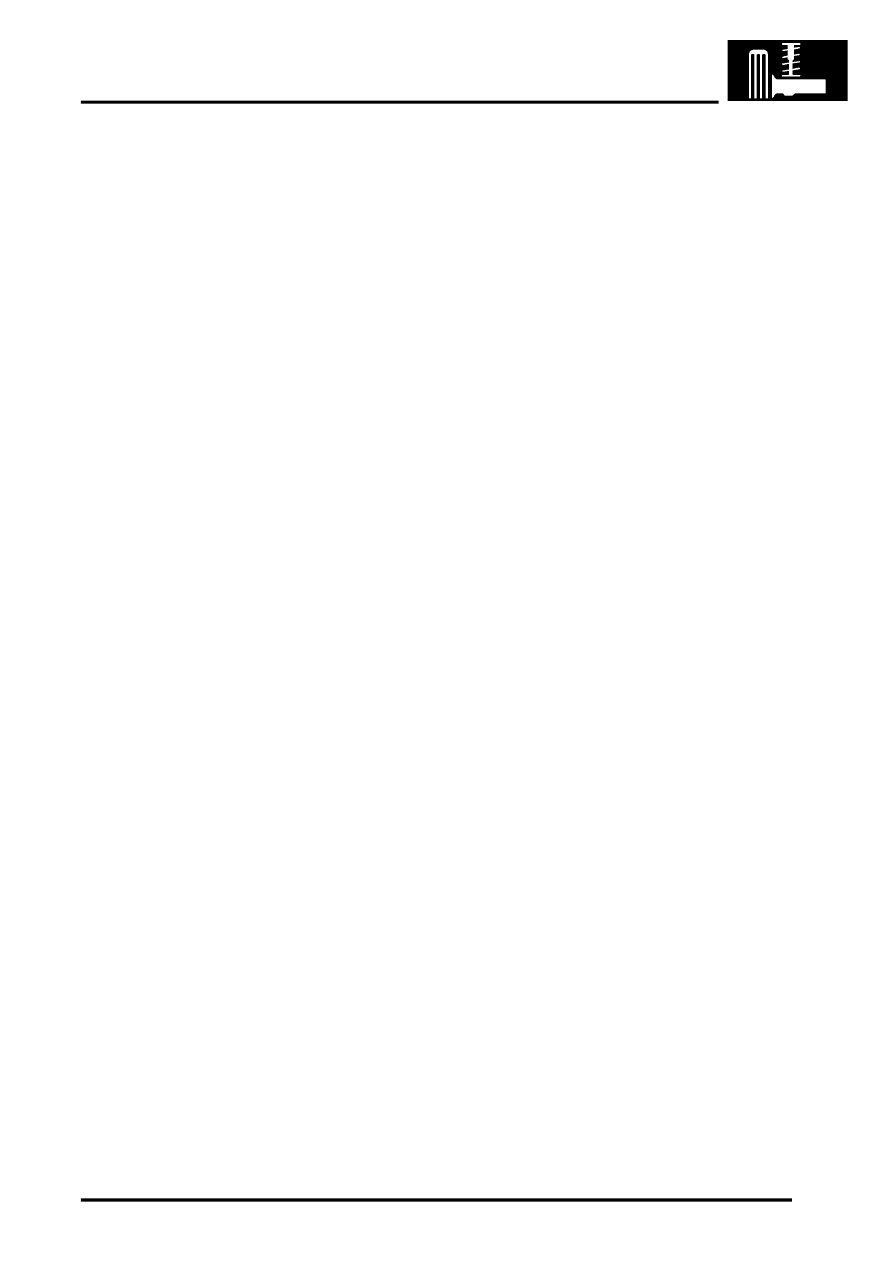
FRONT SUSPENSION
DESCRIPTION AND OPERATION
60-13
The above sequence is applied to each of the six pistons for every revolution of the central shaft and cam. When the
engine is running the sequence occurs rapidly creating a constant flow of fluid. The fluid flow varies with the engine
speed and the rotational speed of the central shaft. The pressure felt at the actuator, created by the flow from the
pump, is controlled by the pressure control valve in the valve block.
The pump has a displacement of 8.5 cm
3
/rev and an operational pressure of 135 bar (1958 lbf.in
2
). The pump output
flow ranges from 7.0 l/min (1.85 US Gallons/min) at 775 rev/min to 9.25 l/min (2.44 US Gallons/min) at 7625 rev/min.
System pipes
Fluid is moved through the ACE system via a series of pipes and hoses. The pipes are mounted on brackets at
strategic points to assure quiet operation of the system.
The pipes from the pump to the valve block and from the valve block to the reservoir are one piece items which are
fitted at the factory before the body is attached to the chassis. If these pipes require replacement in service, the pipes
must be cut to facilitate their removal. 'In service' replacement pipes are available in two parts with a connector to seal
the joint.
The flexible hose which supplies pressure from the pump to the supply pipe attached to the front cross member is
fitted with an attenuator. The attenuator comprises a bullet shaped valve which is located between two spiral wound
springs held at each end of the flexible hose. This valve operates as a restrictor to damp pressure waves of hydraulic
fluid from the pump, reducing noise and strain on components downstream. The attenuator is integral with the supply
hose and pipe and cannot be serviced separately.