Freelander System Description and Operation
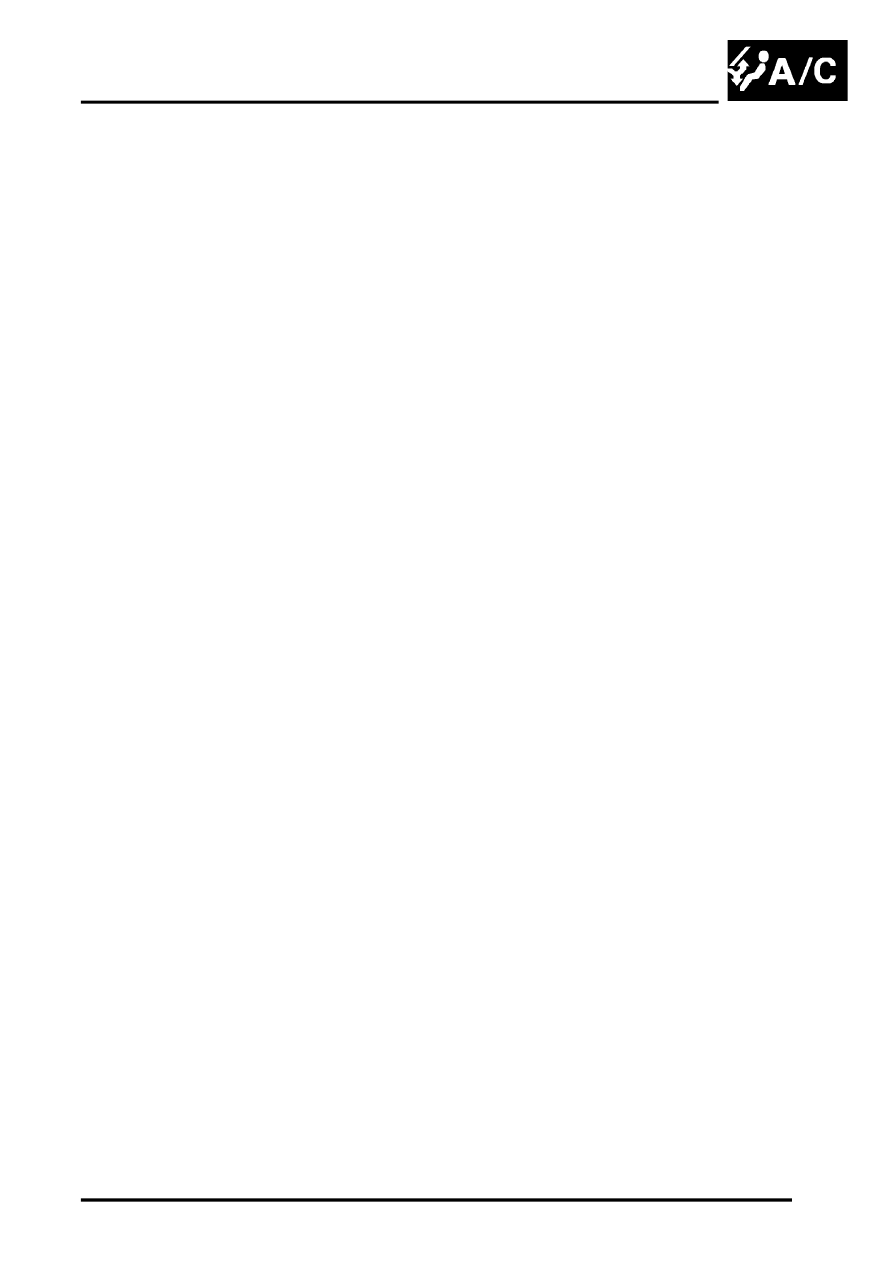
AIR CONDITIONING
DESCRIPTION AND OPERATION
82-9
The control valve assembly consists of a ball valve operated by a push rod connected to a diaphragm. Spring and
atmospheric pressure on one side of the diaphragm are opposed by inlet pressure on the opposite side of the
diaphragm, and also by outlet pressure and a spring acting on the ball valve. The ball valve controls a flow of vapour
from the outlet pressure chamber to produce the servo pressure in the swash plate chamber.
When the engine is running and A/C is off, the clutch is de-energised and the compressor pulley freewheels under
the influence of the drive belt. Vapour pressures are equalised throughout the compressor. The spring between the
lug plate and the swash plate holds the swash plate at the minimum tilt angle (to minimise load during system start-
up).
When A/C is requested, the electro-magnetic clutch is engaged and the pulley turns the central shaft of the
compressor. The lug plate and the swash plate turn with the shaft, and the movement of the angled swash plate
produces reciprocating movement of the pistons. Vapour from the inlet pressure chamber is drawn into the cylinders,
compressed, and discharged into the outlet pressure chamber, producing a flow around the refrigerant circuit.
The flow rate through the compressor is determined by the length of the piston stroke, which is controlled by the tilt
angle of the swash plate. The tilt angle of the swash plate is set by the servo pressure and compressor inlet pressure
acting on the pistons during their induction stroke. A relative increase of inlet pressure over servo pressure moves the
pistons along their cylinders to increase the swash plate tilt angle, the piston stroke and the refrigerant flow rate.
The control valve regulates the servo pressure in the swash plate chamber as a function of inlet pressure, so that the
flow rate of the compressor matches the thermal load at the evaporator, i.e. the more cooling effort that is required in
the cabin of the vehicle, corresponds to a higher thermal load and flow rate. Servo pressure varies between inlet
pressure and inlet pressure + 1 bar (14.5 lbf.in
2
).
On start-up, the compressor inlet pressure is relatively low. In the control valve, the diaphragm and push rod hold the
ball valve open. This allows a restricted flow of outlet pressure through the ball valve into the swash plate chamber,
which maintains the swash plate at a low tilt angle. As the refrigerant flows through the evaporator and absorbs heat
(i.e. as the thermal load increases) the pressure of the vapour entering the compressor increases. In the control valve,
the increased inlet pressure causes the diaphragm and push rod to move to close the ball valve. The resultant
reduction in swash plate chamber pressure, together with the increase in inlet pressure, causes pistons on their
induction stroke to move the swash plate to a higher tilt angle and increase the piston stroke and the refrigerant flow
through the compressor. When the thermal load of the evaporator decreases, the subsequent decrease in pressure
of vapour entering the compressor causes the control valve to open. This increases the swash plate chamber
pressure, which in turn reduces the tilt angle of the swash plate and the refrigerant flow through the compressor.
By matching the refrigerant flow to the thermal load of the evaporator, the variable compressor maintains a relatively
constant evaporator temperature of approximately 3 to 4
°
C (37 to 39
°
F).