LR3/Disco 3
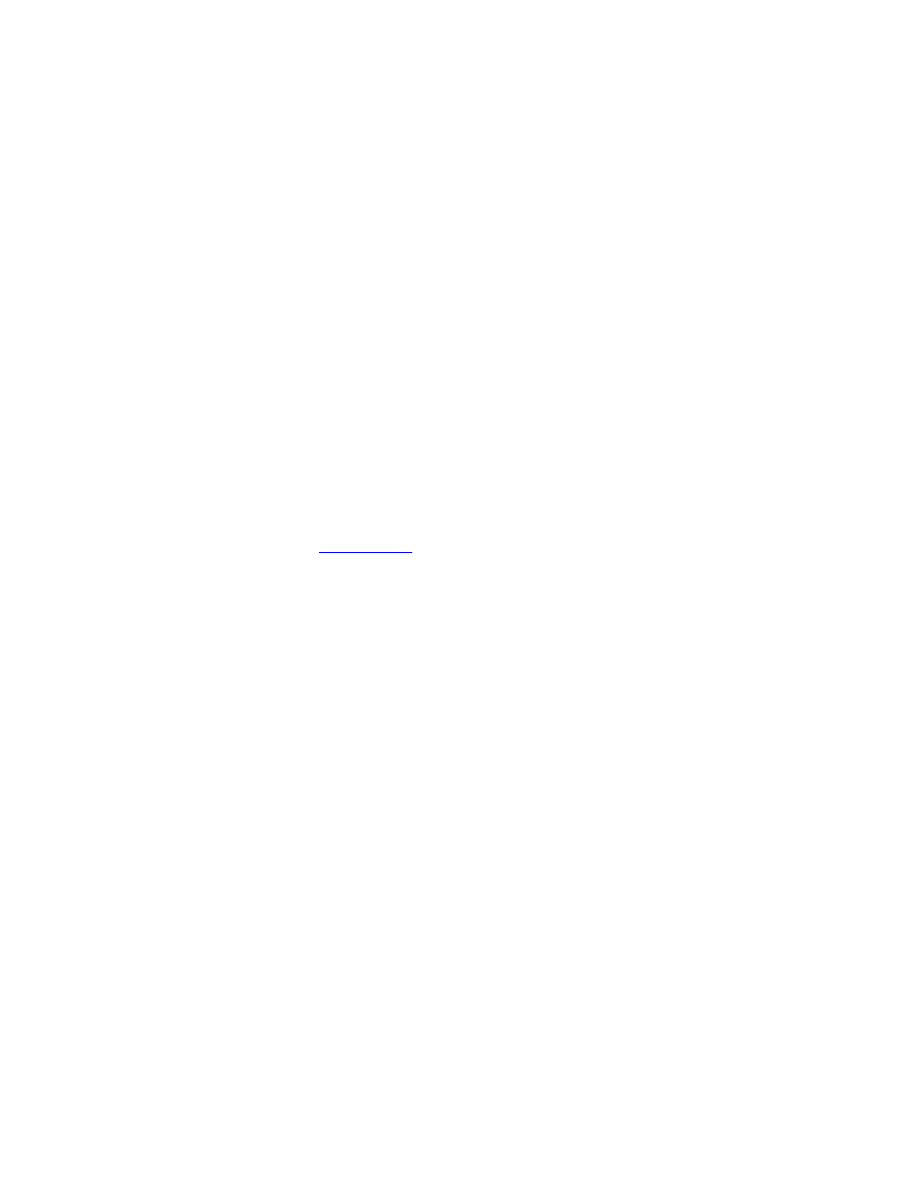
Master Cylinder
The brake master cylinder consists of a cylinder housing containing two pistons in tandem. The rear piston produces
pressure for the primary circuit and the front piston produces pressure for the secondary circuit. The pistons incorporate
center valves with a high flow rate to ensure there is always sufficient fluid available at the hydraulic control unit for
stability control operations.
When the brake pedal is pressed, the front push rod in the brake booster pushes the primary piston along the bore of the
cylinder housing. This produces pressure in the primary pressure chamber which, in conjunction with the primary spring,
overcomes the secondary spring and simultaneously moves the secondary piston along the bore. The initial movement of
the pistons, away from the piston stops, closes the primary and secondary center valves. Further movement of the pistons
then pressurizes the fluid in the primary and secondary pressure chambers, and thus the brake circuits. The fluid in the
chambers behind the pistons is unaffected by the movement of the pistons and can flow unrestricted through the feed
holes between the chambers and the reservoir.
When the brake pedal is released, the primary and secondary springs push the pistons back down the bore of the cylinder
housing. As the pistons contact the piston stops, the primary and secondary center valves open, which allows fluid to
circulate unrestricted between the two hydraulic circuits and the reservoir, through the center valves, the chambers
behind the pistons and the cylinder housing inlets.
Should a failure occur in one of the brake circuits, the remaining brake circuit will still operate effectively, although brake
pedal travel and vehicle braking distances will increase.
Reservoir
The reservoir is installed on top of the master cylinder to provide a supply of brake fluid for the primary and secondary
circuits of the brake system. On manual gearbox models, the reservoir also provides a supply of brake fluid for the clutch.
For additional information, refer to
Clutch Controls
(308-02 Clutch Controls - 2.7L Diesel)
Two straps, integrated onto the sides of the reservoir, engage with lugs on the master cylinder to secure the reservoir in
position. Two outlet spigots on the underside of the reservoir locate in seals installed in the inlet ports of the master
cylinder. An outlet spigot is installed on the left side of the reservoir for the clutch hydraulic circuit, if required. On
automatic gearbox models, the clutch outlet spigot is sealed with a cap, formed during manufacture of the reservoir, which
is only removed if the reservoir is installed on a manual gearbox model.
The reservoir is internally divided to isolate the circuits from each other at low fluid levels, and so prevent a leak in one
circuit from disabling the other circuit(s). The dividing walls support a central well and divide the area around the well into
a further eight separate compartments. The well forms an extension of the filler neck and contains the filter and the fluid
level switch.
The well and the surrounding compartments are interconnected by slots in the dividing walls. The slots are positioned
such that when the reservoir is full, fluid can move between the well and all of the surrounding compartments, but at low
fluid levels the interior forms separate reservoirs for each circuit. The following figure shows the separate reservoirs for
each circuit and the amount retained in each reservoir if there is a leak from one of the other circuits.
Reservoir Interior
NOTE:
A = Clutch reservoir; B = Primary circuit reservoir; C = Secondary circuit reservoir