Leon Mk1
Secondary shaft: Dismounting and assembling |
t | If it is necessary to assemble new pinions, consult section Identification initials, assignation of groups, reductions, amounts for filling → Chapter |
t | The secondary shaft must always be adjusted when parts have been replaced that might affect the position of the tapered roller bearings. Consult the Chart for Adjustments → Chapter. |
t | Dismounting the secondary shaft → Fig. and → Fig. |
Montageübersicht |
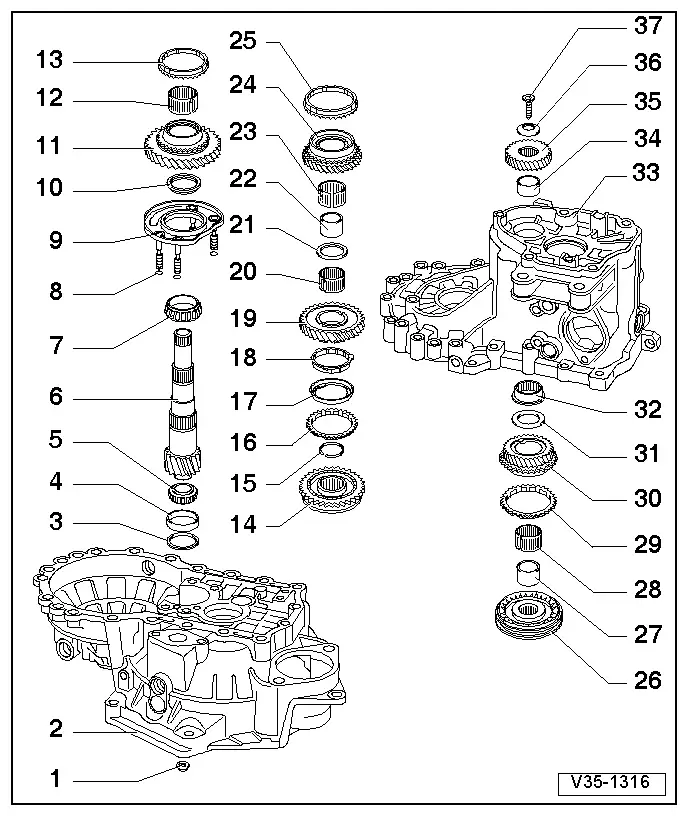
1 - | Nut. 25 Nm + 90º |
q | 4 units |
q | For attaching the secondary shaft |
2 - | Clutch casing |
3 - | Adjustment washer |
q | For the secondary shaft |
q | Finding the thickness → Chapter |
4 - | Outer track, tapered roller bearing |
q | Dismounting → Fig. |
q | Assembling → Fig. |
5 - | Tapered roller bearing |
q | Dismounting → Fig. |
q | Assembling → Fig. |
6 - | Secondary shaft |
q | It is coupled with the pinion for the control drive trains; in the event of replacement they should be changed together. |
q | In the event of replacement → Chapter, Identification initials, assignation of groups, reductions, amounts for filling |
q | Adjustment for the secondary shaft → Chapter |
7 - | Tapered roller bearing |
q | Dismounting → Fig. |
q | Assemble → Fig. |
8 - | Seal ring |
q | 4 units |
q | Always replace |
q | For the bolts for attaching the cover for the secondary shaft bearing → Item |
9 - | Cover for the secondary shaft bearing |
q | It includes the outer track for the tapered roller bearing → Item. |
q | The cover for the secondary shaft bearing must be replaced together with the outer track for the tapered roller bearing and the tapered roller bearing → Item. |
10 - | Stop washer |
q | The edge of the washer must be facing towards the tapered roller bearing. |
11 - | 1st gear pinion |
q | Before assembling the 1st gear pinion assemble the stop washer → Item. |
12 - | Needle bearing for 1st gear pinion |
13 - | Synchroniser ring for 1st gear |
q | Identification → Fig. and → Fig. |
q | Control for wear → Fig. |
q | Check that the flanges have no signs of wear. |
14 - | Synchroniser unit for 1st and 2nd gears |
q | Dismounting the secondary shaft → Fig. |
q | Dismounting → Fig. |
q | Assembling the components → Fig. and → Fig. |
q | Position for assembly → Fig. |
q | Assembly of the secondary shaft → Fig. |
15 - | Safety ring |
q | Use tool -A-81124- for extracting the safety ring. |
q | Always replace. |
16 - | Outer synchroniser ring for 2ndgear |
q | Identification → Fig. and → Fig. |
q | Control for wear → Fig. |
q | Assembly: the trimmings of the synchroniser ring must always be fitted with the pins in the synchroniser unit for 1st and 2nd gear → Item. |
17 - | Intermediate synchroniser ring for 2nd gear |
q | Place it on the outer synchroniser ring → Item |
q | Position for assembly → Fig.. |
q | Replace it if it shows signs of wear or cracks. |
18 - | Inner synchroniser ring for 2nd gear |
q | Identification → Fig. and → Fig. |
q | Control for wear → Fig. |
q | Check that the flanges do not show any signs of wear. |
q | Position for assembly → Fig. |
19 - | 2nd gear pinion |
q | Position for assembly → Fig. |
20 - | Needle bearing for 2nd gear pinion |
21 - | Stop washer |
22 - | Sleeve for needle bearing |
q | Dismounting, together with the 2nd gear pinion → Fig. |
q | Assembling → Fig. |
23 - | Needle bearing for 3rd gear pinion |
24 - | 3rd gear pinion |
25 - | Synchroniser ring for 3rd gear |
q | Check for wear → Fig. |
26 - | Synchroniser unit for 3rd and 4th gears |
q | Dismounting the secondary shaft → Fig. |
Dismounting the synchroniser unit → Fig. |
q | Assembling the components → Fig. and → Fig. |
q | Position for assembly → Fig. |
q | Assembly for the secondary shaft → Fig. |
27 - | Sleeve for needle bearing |
q | Dismounting together with the synchroniser unit for 3rd and 4th gears → Item, → Fig. |
q | Assembling → Fig. |
28 - | Needle bearing for 4th gear pinion |
29 - | Synchroniser ring for 4th gear |
q | Check for wear → Fig. |
30 - | 4th gear pinion |
31 - | Stop washer |
32 - | Needle bearing for the secondary shaft |
q | Dismounting and assembling → Chapter |
33 - | Gearbox casing |
34 - | Sleeve for needle bearing |
q | Dismounting → Fig. |
q | Assembling → Fig. |
35 - | 5th gear pinion |
q | Dismounting and assembling → Chapter |
36 - | Plate spring |
q | Position for assembly: the concave side must remain facing towards the 5th gear pinion. |
37 - | Bolt for attaching the 5th gear pinion |
q | The head of the bolt includes a housing for the plate spring → Item |
q | Assembly → Chapter |
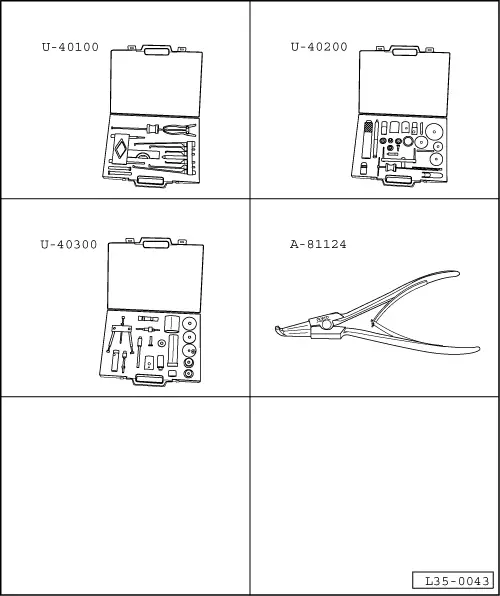
Special tools and workshop equipment required |
t | Case for extractors for gearboxes -U-40100- |
t | Gearbox repair case -U-40200- |
t | Gearbox repair case -U-40300- |
t | Pliers for opening elastic rings -A-81124- |
|
![]() |
|
![]() |
|
![]() |
|
![]() |
|
![]() |
|
![]() |
|
![]() |
|
![]() |
Synchroniser ring | Measurement “a” in a new synchroniser | Wear limit |
1st gear 3rd gear 4th gear | 1.0 … 1.7 mm | 0.5 mm |
|
![]() |
|
![]() |
|
![]() |
|
![]() |
|
![]() |
|
![]() |
|
![]() |
Synchroniser ring | Measurement “a” in a new synchroniser | Limit for wear |
2nd gear | 1.2 … 1.8 mm | 0.5 mm |
|
![]() |
|
![]() |
Synchroniser ring | Measurement “a” in a new synchroniser | Limit for wear |
2nd gear | 0.75 … 1.25 mm | 0.3 mm |
|
![]() |
|
![]() |
|
![]() |
|
![]() |
|
![]() |
|
![]() |
|
![]() |
|
![]() |
|
![]() |