Leon Mk1
Differential: dismantling and assembling |
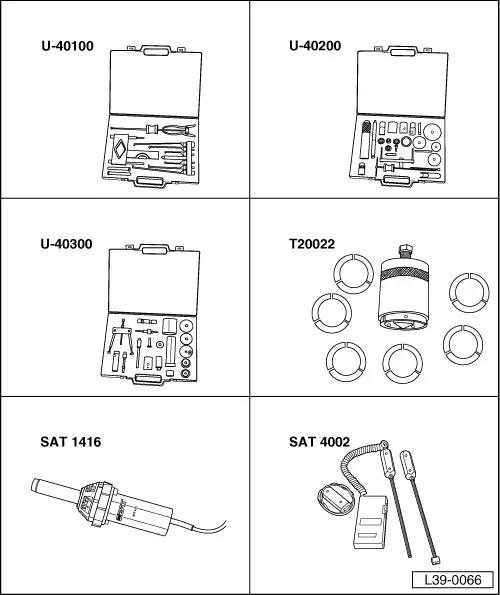
Special tools and workshop equipment required |
t | Gearbox extractor set -U-40100- |
t | Gearbox repair set -U-40200- |
t | Gearbox repair set -U-40300- |
t | Clip extractor with claws -T20022- |
t | Electric blower -SAT 1416- |
t | Digital thermometer -SAT 4002- |

t | The roller bearings and their corresponding outer tracks are matched pairs. They must not be confused or interchanged. |
t | The two roller bearings should be replaced together. |
t | Adjust the differential whenever the roller bearings, differential casing, gearbox casing or clutch housing are replaced. |
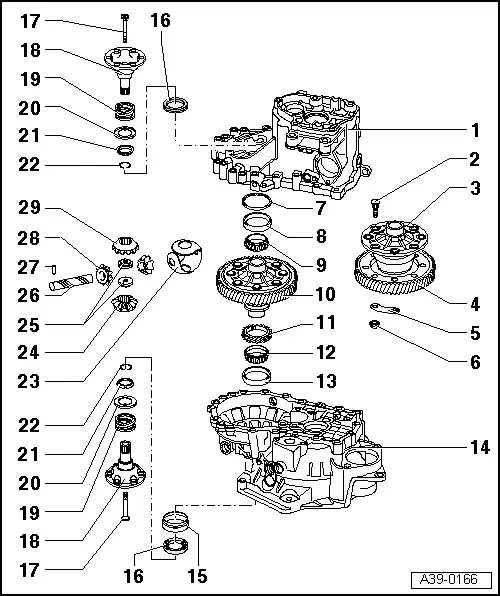
1 - | Gearbox casing |
2 - | Bolt |
3 - | Differential casing |
q | If replaced, refer to Adjustment chart → Chapter |
4 - | Differential crown |
q | Riveted in factory |
q | If renewed, the differential crown and the layshaft must be replaced together |
q | Removing and fitting → Chapter |
5 - | Plate supplement |
6 - | Nut |
q | 70 Nm |
7 - | Shim |
q | For differential |
q | Determine thickness → Anchor |
8 - | Outer track, roller bearing |
q | Remove → Fig. |
q | Fit → Fig. |
9 - | Roller bearing |
q | Remove → Fig. |
q | Fit → Fig. |
10 - | Differential assembly |
q | Crown riveted in factory |
q | If renewed, the differential crown and the layshaft must be replaced together Refer to Adjustment chart → Chapter |
q | Drill the rivets and install with bolts → Chapter, Differential crown: removing and installing |
11 - | Speedometer mechanism sprocket |
q | Remove levering with a flat screwdriver |
q | Installing: fit as far as it will go into the differential casing before installing the roller bearing track → Item |
12 - | Roller bearing |
q | Remove → Fig. |
q | Fit → Fig. |
13 - | Outer track, roller bearing |
q | Remove → Fig. |
q | Fit → Fig. |
14 - | Clutch housing |
15 - | Bush |
q | To house the articulation flange oil seal → Item |
q | Removing and installing → Fig. |
16 - | Articulation flange oil seal |
q | Renew → Chapter |
17 - | Conical bolt |
q | 25 Nm |
q | Bolt with the threaded device for securing the articulation flanges → Item |
18 - | Articulation flanges |
q | Removing and fitting → Chapter |
19 - | Articulation flange spring |
q | Fit behind the articulation flange |
20 - | Thrust washer |
q | Assembly position: Collar towards the spring, core towards the conical ring |
21 - | Conical ring |
q | With recess for the thrust washer |
q | Assembly position: conical side facing the differential casing |
22 - | Safety ring |
q | Maintains the position of the conical ring, washer and spring of the articulation flange when dismantled |
23 - | Set of thrust washers |
q | Impregnate with gearbox oil before installation |
24 - | Planet gear |
q | Fit → Fig. |
25 - | Threaded component to secure the articulation flanges |
q | Fit → Fig. |
26 - | Satellite shaft |
q | Remove with a drift |
q | Fit → Fig. |
27 - | Elastic pin |
q | To hold the satellite shaft |
q | Removing and fitting → Fig. |
28 - | Satellite |
q | Fit → Fig. |
29 - | Planet gear |
q | Fit → Fig. |
![]()
|
![]() |
![]()
|
![]() |
![]()
|
![]() |
|
![]() |
|
![]() |