Leon Mk1
Layshaft: dismantling and assembling |
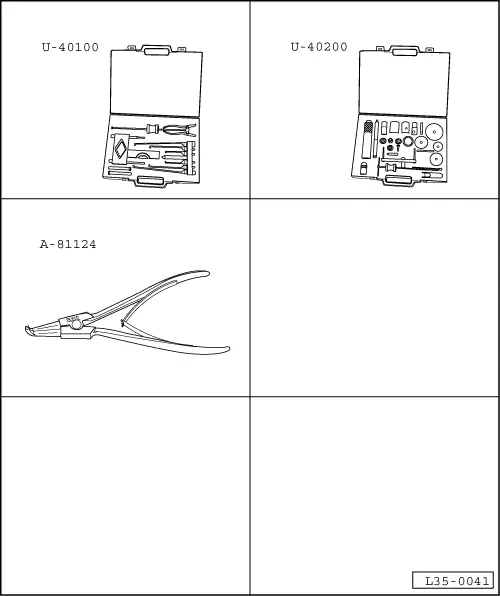
Special tools and workshop equipment required |
t | Gearbox extractor set -U-40100- |
t | Gearbox repair set -U-40200- |
t | Circlip opening pliers -A-81124- |

t | Whenever new gears are fitted consult the technical data → Chapter, Code letters, group numbers, ratios, filling quantities |
t | If the layshaft, roller bearings or clutch housing are replaced, the layshaft should be adjusted → Chapter |

1 - | Gearbox casing cover |
2 - | 5th gear safety ring |
q | Renew |
3 - | Thrust washer |
4 - | Sliding 5th gear |
q | Fit → Chapter, Assembly sequence |
5 - | Gearbox casing |
6 - | Needle roller bearing |
q | Removing and fitting → Chapter, Gearbox casing and gearbox selector shaft: repairing |
7 - | 4th gear safety ring |
q | Renew |
q | Use tool -A-81124- to remove the circlip |
8 - | 4th gear |
9 - | 3rd gear safety ring |
q | Renew |
q | Determine thickness → Chapter, Assembly sequence |
q | Use tool -A-81124- to remove the circlip |
10 - | 3rd gear |
q | Installation position → Chapter, Assembly sequence |
q | Checking axial clearance → Chapter, Assembly sequence |
11 - | Sliding 2nd gear |
12 - | Needle bearing for sliding 2nd gear |
q | Removing the bush → Chapter, Assembly sequence |
q | Fitting the bush → Chapter, Assembly sequence |
13 - | Syncromesh ring 2nd gear |
q | Checking for wear → Fig. |
14 - | Syncromesh assembly for 1st and 2nd gear |
q | Assembly → Fig. and → Fig. |
q | Remove → Chapter, Assembly sequence |
q | Fit → Chapter, Assembly sequence |
15 - | Syncromesh ring 1st gear |
q | Checking for wear → Fig. |
q | Identification → Fig. |
16 - | Sliding 1st gear |
17 - | Spring |
18 - | Sliding sleeve |
19 - | Syncromesh hub |
20 - | Locking keyways |
q | 3 units |
21 - | Needle roller bearing for 1st gear |
22 - | Thrust washer |
q | Installation position → Chapter, Assembly sequence |
23 - | Clutch housing |
24 - | Shim |
q | For layshaft |
q | Adjustment chart → Chapter |
25 - | Outer track, small roller bearing |
q | Remove → Fig. |
q | Fit → Fig. |
26 - | Small roller bearing |
q | Remove → Fig. |
q | Fit → Fig. |
27 - | Layshaft |
q | A matched pair with the driveshaft gear; they must be replaced together |
q | Adjusting → Chapter |
28 - | Large roller bearing |
q | Remove → Fig. |
q | Fit → Fig. |
29 - | Bearing housing |
q | With the external roller bearing track and stop for reverse gear |
q | The external track should only be replaced together with the large roller bearing and the bearing housing |
30 - | Hexagon bolt |
q | 25 Nm + 90° |
|
![]() |
Syncromesh ring | Measurement -a- on a new syncromesh | Wear limit |
1st and 2nd gears | 1.1 … 1.7 mm | 0.5 mm |
|
![]() |
|
![]() |
|
![]() |
|
![]() |
|
![]() |
|
![]() |
|
![]() |
|
![]() |