Leon Mk1
Drive shaft (drive pinion): Assembly overview |

t | Refer to technical data → Chapter when installing new gear wheels or the final drive gear set. |
t | Lubricate all needle bearings on output shaft with gear oil before installing. |
t | Adjustment work is required when renewing the parts marked with 1). Adjustment overview → Chapter. |
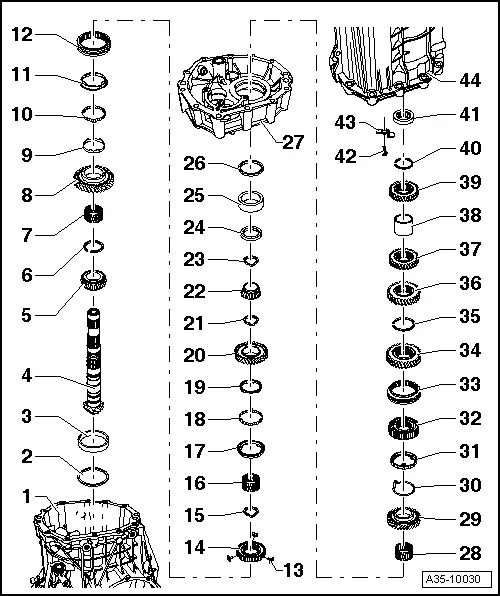
1 - | Gearbox housing 1) |
q | Repairing → Chapter |
2 - | Shim „S3“ |
q | Adjustment overview → Chapter |
3 - | Tapered roller bearing outer race 1) |
q | Remove → Fig. |
q | Pressing in → Fig. and → Fig. |
4 - | Drive shaft (drive pinion) 1) |
q | Is mated with crown wheel, always renew together as a set |
q | Adjusting pinion shaft and crown wheel → Chapter |
5 - | Tapered roller bearing inner race 1) |
q | breaks when removing |
q | replace |
q | Driving out → Fig. |
q | Driving in → Fig. |
6 - | Circlip |
q | Re-determine thickness if tapered roller bearing is renewed → Fig. |
7 - | Needle bearing |
q | For 1st gear |
8 - | 1st speed selector gear |
q | Check axial clearance after installing using feeler gauge → Fig. (0.20 ... 0.50 mm) |
9 - | Inner ring for 1st gear |
q | Installation position → Fig. |
q | Check for wear → Fig. |
q | Renew if scored |
10 - | Intermediate ring for 1st gear |
q | Installation position → Fig. |
q | Check for wear → Fig. |
11 - | Synchro-ring for 1st gear |
q | Installation position → Fig. |
q | Check for wear → Fig. |
q | Renew if scored |
12 - | Locking collar, 1st and 2nd gear |
q | Mark position in relation to synchronising hub prior to removing |
q | Assembling the mobile element/synchroniser body → Fig. |
13 - | Thrust blocks |
q | Installing locking pieces (3x) → Fig. |
14 - | Synchronising hub for 1st and 2nd gear |
q | Installation position: High inside collar faces 2nd gear wheel. |
q | Driving out → Fig. |
q | Driving in → Fig. |
q | Assembling the mobile element/synchroniser body → Fig. |
15 - | Circlip |
q | Mark |
q | Installation position → Fig., -item 1- |
q | Re-determine thickness when renewing 1st and 2nd gear synchronising hub or pinion shaft → Fig. |
16 - | Needle bearing |
q | For 2nd gear |
17 - | Synchroniser ring for 2nd gear |
q | Installation position → Fig. |
q | Check for wear → Fig. |
q | Renew if scored |
18 - | Intermediate ring for 2nd gear |
q | Installation position → Fig. |
q | Check for wear → Fig. |
19 - | Inner ring of 2nd gear |
q | Installation position → Fig. |
q | Check for wear → Fig. |
q | Renew if scored |
20 - | Synchromeshed gear for 2nd gear |
q | Check axial clearance after installing using feeler gauge → Fig. (0.20 ... 0.50 mm) |
21 - | Circlip |
q | Mark |
q | Installation position → Fig., -item 2- |
22 - | Tapered roller bearing inner race 1) |
q | Driving out → Fig. |
q | Driving in → Fig. |
23 - | Circlip |
q | Mark |
q | Installation position → Fig., -item 3- |
24 - | Thrust washer |
q | For reverse gear shaft |
q | Driving out → Fig. |
q | Driving in → Fig. |
25 - | Tapered roller bearing outer race 1) |
q | Remove → Fig. |
q | Driving in → Fig. |
26 - | Shim „S4“ |
q | Adjustment overview → Chapter |
27 - | Bearing housing 1) |
28 - | Needle bearing |
q | For reverse gear shaft |
29 - | Reverse gear mobile pinion |
q | Check axial clearance after installing using feeler gauge (0.20 ... 0.50 mm) |
30 - | Spring |
q | Insert into reverse selector gear → Fig. |
q | Allocation of spring to selector gear → Spare parts catalogue |
31 - | Synchro-ring for reverse gear |
q | Check for wear → Fig. |
32 - | Synchronizer body for the reverse gear |
q | Installation position: High inside collar faces 3rd gear wheel. |
33 - | Reverse gear locking collar |
q | Mark position in relation to synchronising hub prior to removing |
q | Installation position: Taper faces reverse gear synchro-ring |
34 - | 3rd gear wheel |
q | Installation position: Machined side faces reverse gear synchronising hub |
35 - | Circlip |
q | Mark |
q | Installation position → Fig., -item 4- |
q | Re-determine thickness when renewing 3rd gear wheel, reverse gear synchronising hub or pinion shaft → Fig. |
36 - | Gear wheel for 4th gear |
q | Installation position: High inside collar faces 5th gear wheel. |
37 - | 5th gear pinion |
q | Installation position: High inside collar faces 4th gear wheel. |
38 - | Spacer bush |
39 - | Gear wheel for 6th gear |
q | Installation position: High inside collar faces spacer sleeve → Item |
40 - | Circlip |
q | Mark |
q | Installation position → Fig., -item 5- |
q | Re-determine thickness when renewing gear wheels for 4th ... 6th gear, the spacer sleeve or the pinion shaft → Fig. |
41 - | Needle bearing |
q | Bearing for pinion shaft in gearbox cover |
q | removing and fitting → Item |
42 - | Multi-point socket head bolt, 24 Nm |
43 - | Bracket |
q | Secures needle bearing → Item in gearbox cover |
44 - | Gearbox cover |
|
![]() |