Leon Mk1
![]()
|
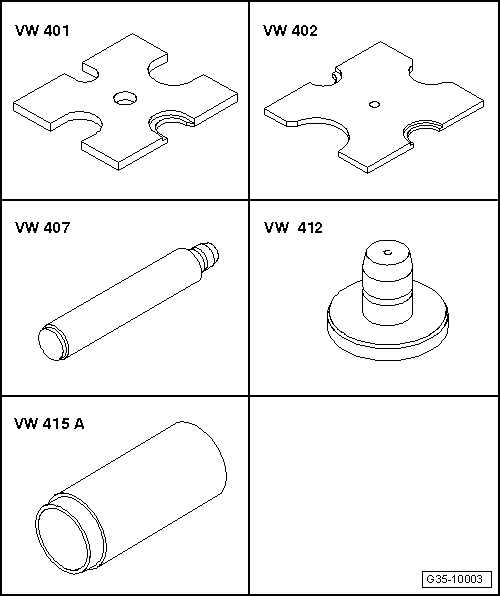
Special tools and workshop equipment required |
t | Clutch press -VW 401-, see equivalent → Anchor |
t | Clutch press -VW 402-, see equivalent → Anchor |
t | Die -VW 407- |
t | Die -VW 412- |
t | Tube element -VW 415 A- |
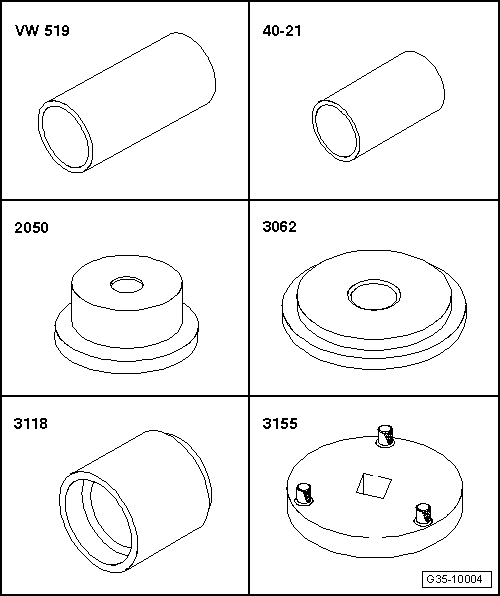
t | Tube element -VW 519- |
t | Press tool -40 - 21- |
t | Thrust blocks -2050- |
t | Thrust pad -3062- |
t | Thrust blocks -3118- |
t | Slotted nut wrench -3155- |
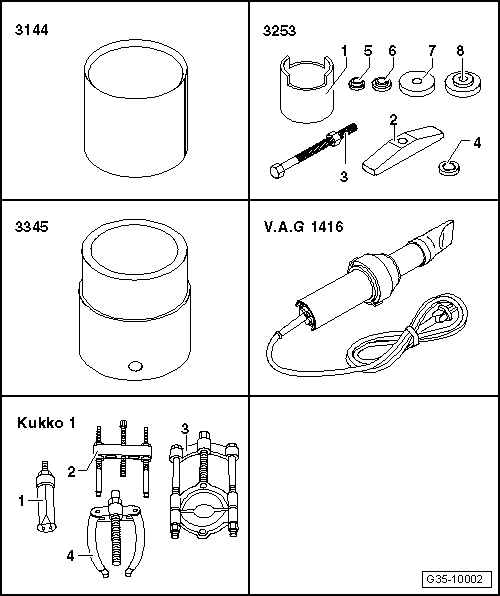
t | Sleeve -3144- |
t | Assembly tool -3253- |
t | Tube for wheel bearing -3345- |
t | Hot air blower -V.A.G 1416-, see equivalent → Anchor |
t | -1-Inside extractor -Kukko 21/8-, see equivalent |
t | -3-Splitter -Kukko 17/2- |
t | -4-Support bracket -Kukko 22/2-, see equivalent |
t | Calibre |
|
![]() |
|
![]() |
|
![]() |
|
![]() |
![]()
|
![]() |
|
![]() |
|
![]() |
|
![]() |
|
![]() |
![]()
|
![]() |
|
![]() |
Retaining ring thickness (mm) | ||
2,50 | 2,56 | 2,62 |
2,53 | 2,59 | 2,65 |
|
Retaining ring thickness (mm) | ||
1,90 | 2,02 | 2,14 |
1,93 | 2,05 | 2,17 |
1,96 | 2,08 | |
1,99 | 2,11 |
|
Retaining ring thickness (mm) | ||
3,50 |
|
Retaining ring thickness (mm) | ||
3,50 |
|
Retaining ring thickness (mm) | ||
1,90 | 1,98 | 2,06 |
1,94 | 2,02 | 2,10 |
|
Retaining ring thickness (mm) | ||
1,90 | 2,02 | 2,14 |
1,93 | 2,05 | 2,17 |
1,96 | 2,08 | 2,20 |
1,99 | 2,11 |
|
![]()
|
![]() |
|
![]() |
Gap -a- | As-new installation value | Wear limit |
1. Gear - inner ring | 1.2 ... 2.0 mm | 0.6 mm |
|
![]() |
Gap -a- | As-new installation value | Wear limit |
1. and 2nd gear | 1,4 ... 2.0 mm | 0.8 mm |
|
![]() |
|
![]() |
|
![]() |
|
![]() |
|
![]() |
|
![]() |