Leon Mk1
![]()
|
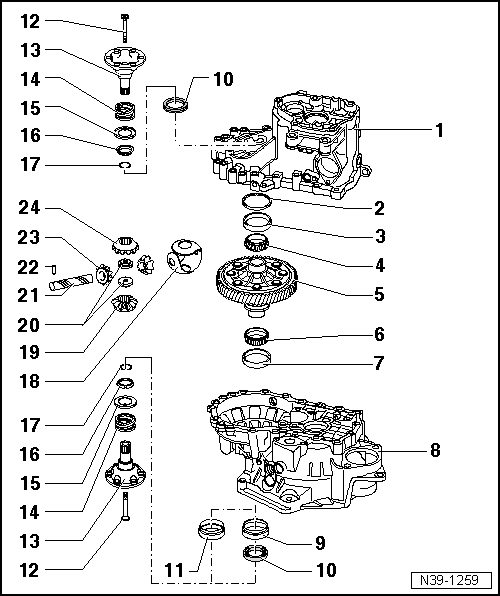
1 - | Gearbox |
2 - | Shim |
q | For differential |
q | Determining thickness → Chapter |
3 - | Outer track, roller bearing |
q | Removing → Fig. |
q | Fitting → Fig. |
4 - | Tapered roller bearing |
q | Removing → Fig. |
q | Fitting → Fig. |
5 - | Differential |
q | With rivet fitted differential crown fitted in the factory |
q | If replaced, the differential crown and the secondary shaft must be replaced together. Refer to Adjustment chart → Chapter |
q | Differential cage adapted to one-piece thrust washer |
q | Hole for spring pin adapted to length of spring pin |
q | Determine according to → Electronic parts catalogue (ETKA) |
6 - | Tapered roller bearing |
q | Removing → Fig. |
q | Fitting → Fig. |
7 - | Outer track, roller bearing |
q | Removing → Fig. |
q | Fitting → Fig. |
8 - | clutch housing |
9 - | Thrust piece |
q | To house the seal for right hand flanged shaft |
q | Removing → Fig. |
q | Fitting → Fig. |
10 - | Flanged shaft oil seal |
q | Renewing oil seal for left flange shaft with gearbox installed → Chapter |
q | Renewing seal for right flange shaft with gearbox installed (two-part seal and sleeve for right flange shaft) → Chapter |
11 - | One-piece oil seal and sleeve |
q | If oil seal is damaged, renew sleeve and oil seal together → Chapter |
q | replace → Fig. |
12 - | Countersunk bolt |
q | 25 Nm |
q | Screw with threaded element to secure the articulation flanges → Item |
13 - | Articulation flange |
q | removing and fitting → Chapter |
14 - | Compression spring for flange shaft |
q | Install it behind the flanged shaft |
15 - | Thrust washer |
q | Installation position: Collar towards the spring, core towards the conical ring |
16 - | Conical ring |
q | With recess for the thrust washer |
q | Installation position: conical side facing the differential casing |
17 - | Circlip |
q | Keep the following in position: conical ring, shim and spring for flanged shaft when it is dismantled |
18 - | Set of thrust washers |
q | Impregnate with gearbox oil before installation |
q | One-piece thrust washer has a projection on some versions → Fig. |
19 - | Large differential bevel gear |
q | Fitting → Fig. |
20 - | Threaded unit for securing articulated flanges |
q | Fitting → Fig. |
21 - | Planet gear shaft |
q | Drive out using drift |
q | Removing in conjunction with shorter spring pin → Fig. |
q | Removing in conjunction with longer spring pin → Fig. |
q | Fitting → Fig. |
22 - | Spring pin |
q | For securing differential pinion pin |
q | Spring pins of different lengths have been installed |
q | Remove with a suitable drift → Fig. |
23 - | Small differential bevel gear |
q | Fitting → Fig. |
24 - | Large differential bevel gear |
q | Fitting → Fig. |