Leon Mk1
|
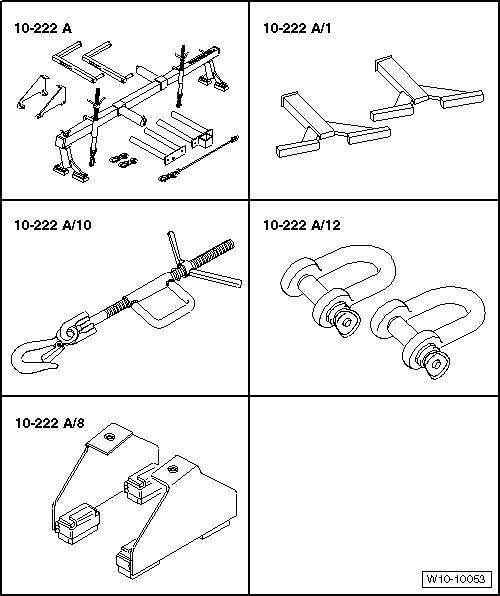
Special tools and workshop equipment required |
t | Suspension tool -10-222 A-, see equivalent → Anchor |
t | Frame -10 222A/1-, see equivalent → Anchor |
t | Additional hook -10-222 A/10-, see equivalent → Anchor |
t | Shackle -10-222 A/12-, see equivalent → Anchor. |
t | Adapter -10 - 222 A /8-, see equivalent → Anchor |
|
|
![]() |
![]()
|
![]() |
|
![]() |
1. | Unscrew bolts -2 + 3-. | |
2. | Removing the top bracket of the particle filter. | |
3. | Unscrew bolts + nuts - 4 + 5- | |
4. | Removing the bottom bracket of the particle filter. |
|
![]()
|
![]() |
|
![]() |
![]()
|
![]() |
![]()
|
![]() |
|
![]() |
|
![]() |