Leon Mk1
Piston and conrod - assembly overview |
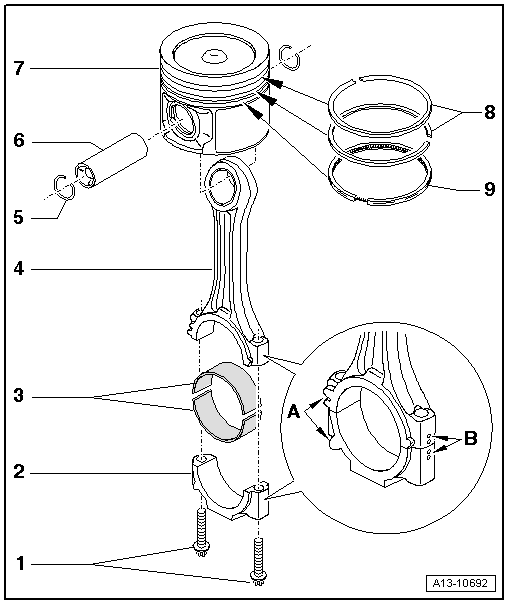
1 - | Bolt. |
q | Replace |
q | Oil threads and contact surface. |
q | 30 Nm + turn +90° further |
2 - | Conrod bearing cap |
q | Due to the cracking method used to separate the bearing cap from the conrod in manufacture, the caps only fit in one position and only on the appropriate conrod |
q | Mark cylinder allocation in colour -B- |
q | Fitting position: Marking -A- towards the pulley end |
3 - | Bearing cap |
q | Installation position → Fig. |
q | Mark used bearing shells for re-installation but not on bearing surface |
q | Renew bearing shells worn down to base layer. |
q | Note design: Upper bearing shell (towards piston) made of wear-resistant material. Distinguishing feature of new bearing shells: Black line on contact surface in area of joint |
q | Check for secure seating. |
4 - | Conrod |
q | Renew as set only. |
q | With industrially cracked conrod bearing cap |
q | Separating parts of new conrod → Fig. |
q | Mark cylinder allocation in colour -B- |
q | Fitting position: Marking -A- towards the pulley end |
q | Axial clearance: Wear limit: 0.37 mm |
q | Measuring radial clearance → Chapter |
5 - | Circlip |
q | Replace |
6 - | Piston pin |
q | If difficult to remove, heat piston to approx. 60 °C |
q | Remove and install with drift -VW 222 A- |
7 - | Piston |
q | with combustion chamber |
q | Mark installation position and cylinder number → Fig. |
q | check → Fig. |
q | Install using piston ring clamp |
q | Piston and cylinder dimensions → Chapter |
q | Measuring cylinder bore → Fig. |
q | Measuring piston projection at „TDC“ → Chapter |
8 - | Piston rings |
q | Compression rings |
q | Offset gaps by 120° |
q | Use piston ring pliers to remove and install |
q | Fitting position: Marking „TOP“ or side with lettering faces towards piston crown |
q | Measuring piston ring gap → Fig. |
q | Measuring axial clearance → Fig. |
9 - | Piston ring |
q | Oil scraping ring |
q | Offset gap 120° from bottom compression ring |
q | Use piston ring pliers to remove and install |
q | Measuring piston ring gap → Fig. |
q | Measuring axial clearance → Fig. |
Piston ring | new mm | Wear limit mm |
1. compression ring | 0,20 … 0,40 | 1,00 |
2. compression ring | 0,20 … 0,40 | 1,00 |
Oil scraping ring | 0,25 … 0,50 | 1,00 |
|
![]() |
Piston ring | new mm | Wear limit mm |
1. compression ring | 0,06 … 0,09 | 0,25 |
2. compression ring | 0,05 … 0,08 | 0,25 |
Oil scraping ring | 0,03 … 0,06 | 0,15 |
![]()
|
![]() |
|
![]() |
|
![]() |
|
![]() |
|
![]() |
|
![]() |
![]()
|
![]() |