Leon Mk1
Piston and connecting rod: disassembly and assembly |
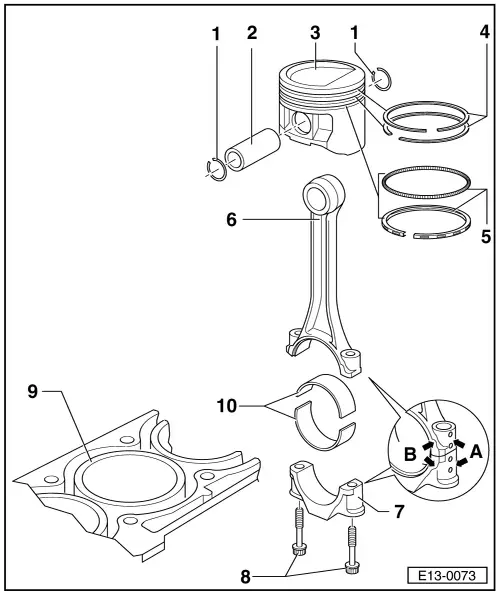
1 - | Safety key |
2 - | Piston pin |
q | If difficult to move, heat the piston to 60 oC |
q | Remove and fit with the -T20019- |
3 - | Piston |
q | Testing → Fig. |
q | Mark the fitting position and correspondence to the respective cylinder |
q | The arrow on the piston head should point towards the pulley |
q | Fit with sleeve for fitting rings |
4 - | Compression rings |
q | Stagger the cuts in 120o |
q | Remove and fit the rings with ring pliers |
q | The “TOP” mark must face the piston head |
q | Check the play between the ends of the rings → Fig. |
q | Check the coupling play between the rings and the piston grooves → Fig. |
5 - | Oil scraper rings |
q | Carefully remove and fit by hand the two parts of the rings |
q | The “TOP” mark must face the piston head |
q | Check the play between the ends of the rings → Fig. |
q | Check the coupling play between the rings and the piston groove → Fig. |
6 - | Connecting rod |
q | Always replace the unit |
q | Mark the correspondence to the cylinder -A- |
q | Fitting position: The marks -B- should point towards the pulley |
q | Axial guide per piston |
7 - | Connecting rod caps |
q | Check the fitting position |
q | Cracked connecting rods can be fitted in only one position and only with the corresponding connecting rod |
8 - | Connecting rod bolt, 20 Nm + 1/4 turn (90o) |
q | Replace |
q | Lubricate the thread and support surface |
q | Too measure the radial play tighten to 20 Nm, without retightening |
q | Retightening may be done in several steps |
q | The retightening angle may be measured with protractor -T20030- |
9 - | Aluminium engine block |
q | Check the bore of the cylinders → Fig. |
q | Piston and cylinder dimensions → Chapter |
10 - | Half bearing |
q | Do not swap used half bearings |
q | Fit the half bearings centred |
q | Measure the radial play with Plastigage: New: 0.020...0.061 mm Wear limit: 0.091 mm When measuring the radial play do not turn the crankshaft |
|
![]() |
Piston ring | Wear limit | |
Compression | 1.0 mm | |
oil scraper | 1.0 mm |
|
![]() |
Piston ring | Wear limit | |
Compression | 1.5 mm | |
oil scraper | 1.5 mm |
|
![]() |
![]()
|
![]() |