Leon Mk1
Piston and conrod - assembly overview |
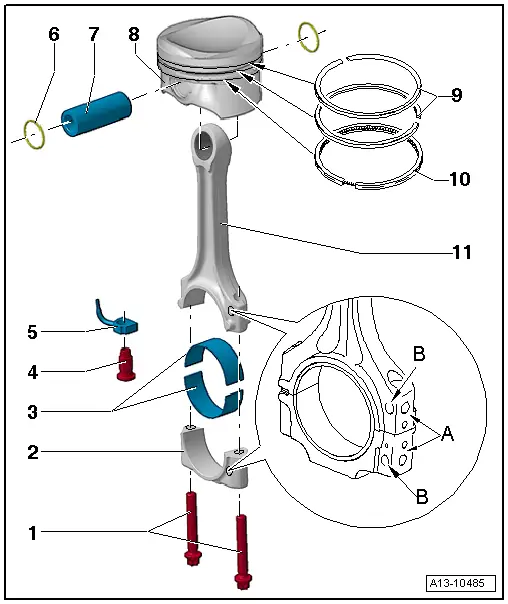
1 - | Conrod bolt |
q | On vehicles with 1.8 ltr. engine: 30 Nm + turn 90° further |
q | On vehicles with 2.0 ltr. engine: 45 Nm + turn 90° further |
q | Replace |
q | Oil threads and contact surface. |
q | Use old bolts when measuring radial clearance |
q | When measuring radial clearance, tighten to 30 Nm but do not turn further |
2 - | Bearing cap |
q | Note fitting position: |
q | Due to the cracking method used to separate the bearing cap from the conrod in manufacture, the caps only fit in one position and only on the appropriate conrod |
q | Mark cylinder allocation -A- |
q | Installation position: Marking -B- faces towards pulley end. |
q | Separate the new piston rod → Chapter |
3 - | Bearing shells |
q | Installation position → Fig. |
q | Do not interchange used bearing shells (mark). |
q | New axial play: 0.10... 00.35 mm Wear limit: 0.40 mm |
q | Checking radial clearance with Plastigage: new: 0.02..0.06 mm Wear limit: 0.09 mm. Do not turn crankshaft when measuring radial clearance. |
4 - | Pressure release valve |
q | 27 Nm |
5 - | Oil spray jet |
q | For piston cooling |
6 - | Circlip |
7 - | Piston pin |
q | If difficult to move, heat piston to approx. 60 °C |
8 - | Piston |
q | Checking → Fig. |
q | Mark installation position and cylinder number. |
q | Arrow on piston crown points to pulley end |
q | Install using piston ring clamp |
q | Piston and cylinder dimensions → Chapter |
q | Checking cylinder bore → Fig. |
9 - | Compression rings |
q | Offset gaps by 120 ° |
q | Use piston ring pliers to remove and install |
q | „TOP“ or „R“ must face towards piston crown |
q | Checking ring gap → Fig. |
q | Checking ring-to-groove clearance → Fig. |
10 - | Oil scraping ring |
q | 2-part |
q | Offset gap of top steel element of piston ring by 120° to next compression ring. |
q | „TOP“ or „R“ must face towards piston crown |
q | Offset gaps of individual parts of oil scraper ring. |
q | Checking ring gap → Fig. |
q | Ring-to-groove clearance cannot be checked. |
11 - | Conrod |
q | Only a complete set may be replaced |
q | Mark cylinder allocation -A- |
q | Installation position: Marking -B- faces towards pulley end. |
q | Separate the new piston rod → Chapter |
Piston ring Dimensions in mm | When new | Wear limit |
compression ring | 0,20...0,40 | 0,80 |
Oil scraping ring | 0,25...0,50 | 0,80 |
|
![]() |
Piston ring Dimensions in mm | When new | Wear limit |
1. compression ring | 0,06 … 0,09 | 0,20 |
2. compression ring | 0,03 … 0,06 | 0,15 |
Oil scraper rings | cannot be measured |
|
![]() |
![]()
|
![]() |
|
![]() |