Leon Mk1
|
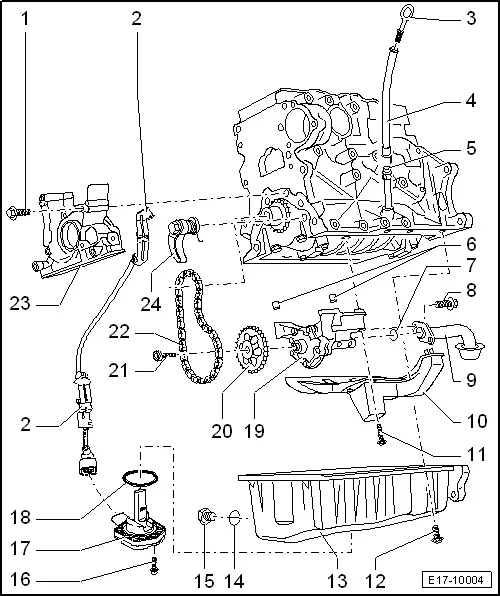
1 - | 15 Nm |
2 - | Retainer |
q | Wiring harness for the oil level and oil temperature sender -G266- |
3 - | Oil dipstick |
q | The oil level must not be above the MAX mark. - Risk of damage to the catalytic converter! |
q | Dip stick marks → Fig. |
4 - | Filling funnel |
q | Remove and evacuate the oil by absorption |
5 - | Guide pipe |
6 - | Dowel sleeves |
7 - | O ring |
q | Renew |
8 - | 15 Nm |
9 - | Suction line |
q | Clean strainer if soiled. |
10 - | Baffle plate |
11 - | 15 Nm |
12 - | 15 Nm |
13 - | Oil sump |
q | Clean sealing surface before fitting. |
q | Removing and fitting → Chapter |
14 - | Seal |
q | Renew |
15 - | Oil drain plug, 30 Nm |
q | With permanent oil seal |
q | Renew |
16 - | 10 Nm |
17 - | Oil level/oil temperature sender -G266- |
q | Depending on design |
q | Removing and fitting → Fig. |
q | Checking: → Vehicle diagnostic, testing and information system VAS 5051 |
18 - | O ring |
q | Renew |
q | Grease before assembly. |
19 - | Oil pump: |
q | For pressure relief valve, approx. 12 bar |
q | Removing and fitting → Chapter |
q | Before fitting check that the dowel pegs are fitted → Item |
q | Replace if there is scoring on the friction surfaces or the gear teeth. |
q | Tightening torque for oil pump cover to oil pump housing: 10 Nm |
20 - | Oil pump chain sprocket: |
q | Note fitting position: |
q | Sprocket can only be fitted on oil pump shaft in one position. |
q | Oil pump chain sprocket: Removing and installing → Chapter |
21 - | 20 Nm + 90° (1/4 turn) |
q | Renew |
22 - | Chain for oil pump |
q | Make a coloured marking for the direction of rotation with before removing |
q | Check for wear. |
23 - | Front sealing flange: |
q | Must be housed correctly in the dowel sleeves for adjusting |
q | Removing and fitting → Chapter |
q | Crankshaft oil seal, pulley end: Renew → Chapter |
24 - | Chain tension device with tensor rail, 15 Nm |
q | Do not dismantle. |
q | Note fitting position: |
q | Pre-tension spring and engage before installing |
|
![]() |
|
![]() |
|
![]() |